Baza wiedzy Lean
Plan for Every Part - podstawa efektywnej logistyki wg zasad Lean
Dlatego też obecnie managerowie logistyki coraz większą uwagę przywiązują do efektywnej organizacji logistyki wewnętrznej, w oparciu o szeroko pojęte zasady Lean. Płynne i szczupłe przepływy wewnątrz przedsiębiorstwa, organizacja i optymalizacja przestrzeni magazynowych, a także analiza ich wartości, stały się kluczowym elementem dobrze prosperującej logistyki wewnętrznej.
Codzienna, logistyczna rutyna
Mimo iż prowadzenie statystyk i analiz stało się codzienną, logistyczną rutyną, która dzięki systemom ERP jest łatwa i szybka do przygotowania, nie daje ona pełnego obrazu bieżącej sytuacji. W efekcie, nawet przy dobrze sparametryzowanym systemie, każde odchylenie od normy - w przypadku pojedynczych referencji - wymaga sporo wysiłku i zaangażowania zespołu logistyków, aby zweryfikować cały proces, przepływ materiałowy, czy też faktyczne stany magazynowe.
Na przestrzeni wielu lat pracy w dziale logistyki, zdołałam się przekonać, że aby mieć kompleksowe dane dla każdej części z osobna, należy wrócić do źródła logistycznego Lean’u.
Plan for Every Part - jakie korzyści
W tym przypadku tzw. P.F.E.P., czyli Plan Dla Każdej Części jest narzędziem, które pozwala na dokładną weryfikację bieżących potrzeb przedsiębiorstwa, a także na przedstawienie realnego obrazu jakości zarządzania materiałem wewnątrz przedsiębiorstwa.
Przy dobrej organizacji i rzetelności zebranych danych, daje ono pełne spojrzenie na bieżącą sytuację. Co prawda jego przygotowanie wymaga pełnego zaangażowania i dokładności ze strony zespołu, który dostarcza dane, niemniej wysiłek włożony w przygotowanie, opłaca się w trakcie użytkowania PFEPa.
Na czym należy się skupić? Przede wszystkim na podstawowych logistycznych aspektach – oddzielnie dla każdej części. Poniższa ilustracja obrazuje główne części składowe Planu Dla Każdej Części.
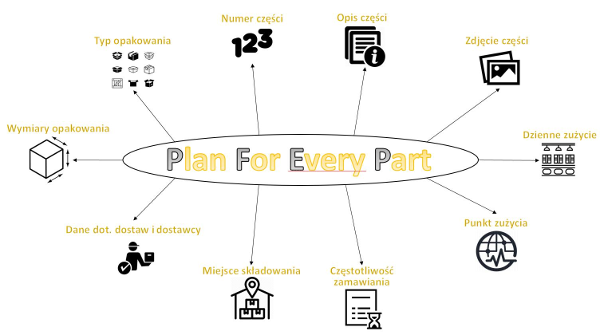
Kluczowe składowe PFEP
Oczywiście ilość danych zależy głównie od docelowego użytkownika, czyli przede wszystkim od pracowników działu, bądź managerów logistyki. Dlatego też bazę można poszerzać o dowolne pozycje. Jednak za podstawowe składowe uważa się: numer części/surowca, jej nazwę, dzienne zużycie, punkt zużycia, dane dot. dostaw i dostawcy, częstotliwość zamawiania, miejsce składowania, typ opakowania oraz jego wymiary itp. Do przydatnych punktów warto zaliczyć zdjęcie części, bądź jej szkic, gdyż ułatwia to znacznie szybszą wzrokową identyfikację.
Do zapisu wszystkich skompletowanych informacji o surowcu/półprodukcie czy wyrobie gotowym, może nam posłużyć zwykły arkusz Excel. Wtedy jednak należy pamiętać, iż mimo że użytkowników pliku będzie kilku, to właściciel, powinien być jeden i wyłącznie on będzie czuwał nad jego bieżącym uaktualnianiem.
Możliwe problemy
Problem pojawia się wówczas, gdy zmiany wewnątrz zakładu zachodzą dynamicznie. Racjonalnym wyjściem w tej sytuacji jest automatyzacja pliku, która na podstawie informacji z systemu ERP - pozwoli na wprowadzanie zmian na bieżąco. Jest to co prawda funkcjonalność, której nie wprowadzi zwykły logistyk, niemniej przy odrobinie fachowej pomocy, pełna automatyzacja pliku PFEP jest bardzo pomocna i okazuje się bardzo często niezbędna.
Wielokrotnie zadawano mi pytanie: do czego służy PFEP? Co on nam da? Otóż do podstawowych zalet tego narzędzia zalicza się: dostęp do wszelkich danych dot. surowców czy produktów w jednym miejscu; możliwości tworzenia lub modyfikowania projektów lean’owych na wewnętrznych, już istniejących przepływach materiałowych; możliwości optymalizacji, w tym także ułatwianie zarządzania przestrzenią magazynową; podstawa do tworzenia nowych systemów dystrybucji surowców, czy wyrobów gotowych wewnątrz jak i na zewnątrz przedsiębiorstwa produkcyjnego.
Warto pamiętać, że czasami narzędzia uważane za niepotrzebne i przestarzałe - a Plan for Every Part może być jednym z takich - dają w efekcie końcowym większą wartość dodaną, niż zautomatyzowane, nowoczesne programy optymalizujące procesy.
Przeczytaj również o Lean
-
Dostawy Milk Run – etap planowania
Dobry plan to podstawa skutecznego projektu, dobrze zaprojektowany Milk Run to spokój w zaopatrywaniu naszej produkcji. Jak w każdym przypadku, tak i w sytuacji dostaw w układzie mleczarza powodzenie tkwi w szczegółach i w dobrym planowaniu. W niniejszym artykule przedstawione zostaną elementy, na które należy zwrócić uwagę podczas projektowania efektywnych tras Milk Run.
-
Nie taki DMAIC straszny, jak go malują…
W drugiej odsłonie wprowadzenia do Six Sigma zapraszam do szybkiego spojrzenia na główny oręż, jakim Six Sigma dysponuje, czyli na metodykę DMAIC.
-
7 marnotrawstw – cz. 3
Ostatnie dwa marnotrawstwa związane są z przeszacowanymi zamówieniami i nadmierną produkcją. Są to marnotrawstwa w fabrykach niestosujących zasad Lean w zarządzaniu postrzegane są jako dobrobyt. Przyglądnijmy się bliżej zapasom i nadprodukcji.
-
Obliczanie czasu taktu (T/T)
W poniższym artykule opiszemy, co to jest czas taktu oraz podamy wzór niezbędny do jego obliczenia. Przedstawimy również, w dlaczego warto znać jego wartość.
Technologie wspierające Lean
PARTNERZY SEKCJI:
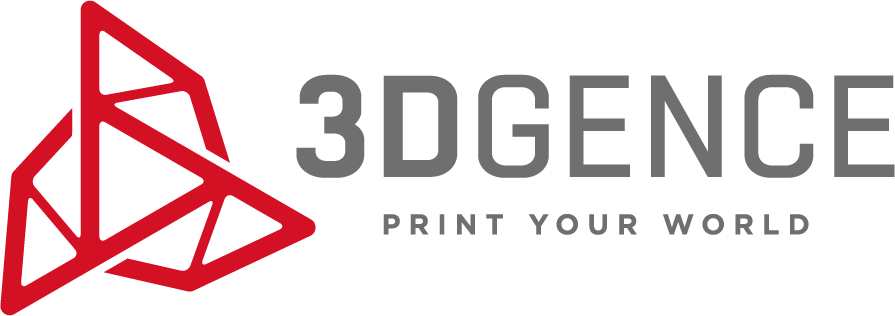
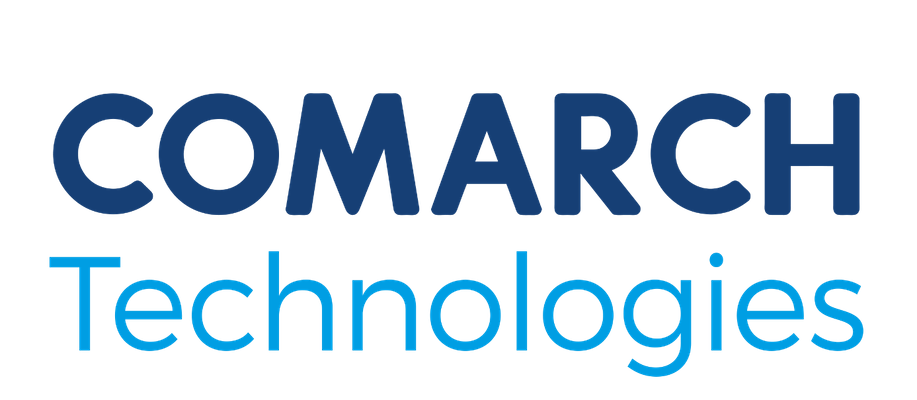
Komentarze
W dniach 14-16 maja 2025 roku w Centrum Edukacyjno-Kongresowym Politechniki Śląskiej odbędzie się Ogólnopolski Kongres Jakościowy 2025. To największe wydarzenie w Polsce poświęcone jakości, łączące wiedzę, relacje i biznes. Kongres stanowi unikalną o ...
Dziewiąta edycja Europejskiego Kongresu Lean przyniosła uczestnikom ogromną dawkę wiedzy na temat wdrażania efektywnych procesów i innowacji w różnych branżach. Organizatorzy podkreślali, że kluczowym przesłaniem wydarzenia jest przekonanie, że to, c ...