Baza wiedzy Lean
Wdrożenie TPM – czyli jak regularne działanie pozwala oszczędzać
Niestety powyższy scenariusz nie jest zmyślony, a wynikający z życia polskiego dyrektora Działu Utrzymania Ruchu. TPM jest jedną z tych dziedzin Leanu, której wdrożenie opiera się na postawie całej załogi wobec przyjętych standardów. Dział Utrzymania Ruchu jest tylko jednym z trybów całej „maszynerii”, a wskaźniki OEE nie windują do 90% w ciągu pół roku – przynajmniej u tych, którzy dobrze je mierzą.
Kroki wdrażania TPM znajdują się w kolejnym artykule
Skupmy się na podstawach, czyli na potwierdzeniu czym jest TPM i w jaki sposób przynosi korzyści zakładowi. Produktywne Utrzymanie Maszyn i Urządzeń jest podejściem, które opiera się na ośmiu filarach (zgodnie z wytycznymi japońskiego instytutu JIPM).
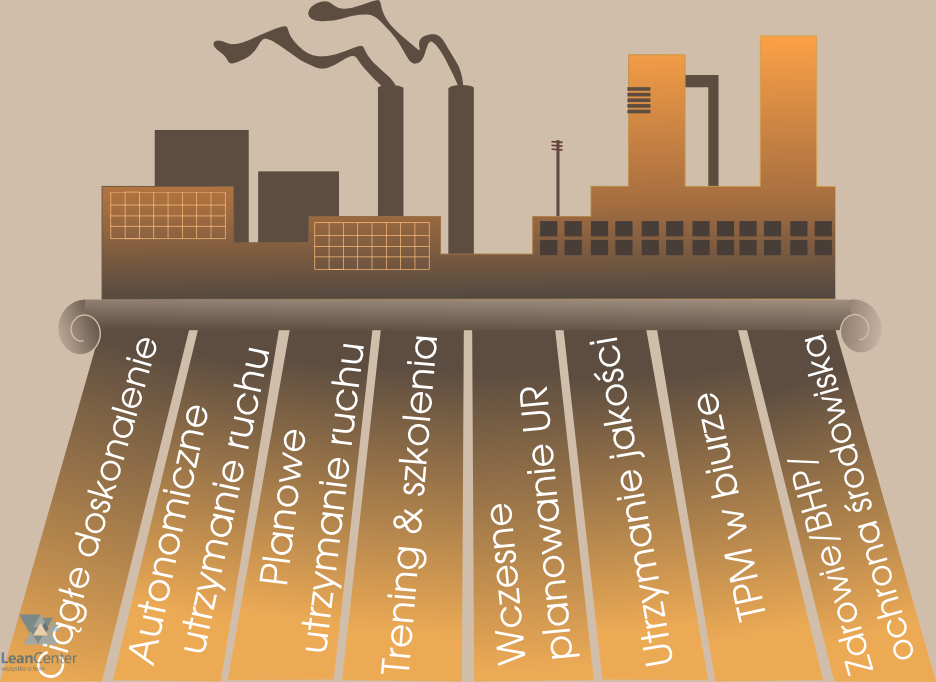
Jak widzimy, nie ma tutaj mowy o sprawnym usuwaniu awarii, a pierwszym filarem jest ciągłe doskonalenie. Skąd my to znamy. Tak, japońscy inżynierowie także w kwestii obsługi maszyn uznali, że nie jest ważne, jak musimy je naprawić, tylko ważne jest jak możemy je obsługiwać, by działały dla nas coraz bardziej niezawodnie. Nie jest ważne, jak szybko możemy je naprawić i zapomnieć o awarii, ale ważne jest, jak możemy zrozumieć, dlaczego awaria się pojawiła. Chcemy to zrozumieć po to, aby w przyszłości do przestojów linii nie dochodziło. Nie ważne jest, aby maszyna zrobiła jak najwięcej dziś, mimo pracy na granicy wytrzymałości, ale ważne jest aby w ogólnym rozrachunku wyprodukowała dla nas tyle produktów i potrzebujemy – właśnie poprzez minimalizację ilości nieplanowych przestojów.
Jak osiągnąć zero awarii?
Drugim filarem TPM jest autonomiczne utrzymanie ruchu. Znów nie ma tutaj mowy o naprawie maszyn. Co oznacza słowo autonomiczne? Jest to zaangażowanie każdego z pracowników w proces obsługi bieżącej maszyn. Bazując na tym filarze, wychodzimy z założenia, że pracownik, który pracuje przy maszynie osiem godzin dziennie, pięć dni w tygodniu, zna jej pracę lepiej niż kierownik oddziału, albo pracownik utrzymania ruchu mający w swej opiece kilkadziesiąt maszyn. To operator jako pierwszy słyszy zbyt głośną pracę, większe niż zazwyczaj drganie maszyny lub pojawiające się wycieki. Aby maszyna służyła i jemu, i nam, wystarczy pozwolić mu wypowiedzieć się na temat pojawiających się problemów. O autonomicznym utrzymaniu ruchu możemy mówić wtedy, gdy wszyscy operatorzy są zaangażowani w obserwację maszyn zgodnie z wytyczonymi standardami. Standardy kontroli urządzeń określa załoga wytypowana do warsztatów TPM w ramach kolejnych kroków wdrożenia, które opisaliśmy w osobnym artykule. Trzeci filar TPM-u, to planowe utrzymanie ruchu. Znając zachowania maszyny i wnioskując, jak w przyszłości będą zużywać się jej elementy, wprowadzamy planowe konserwacje i naprawy. Dział Utrzymania Ruchu posiada jasno wyznaczone terminy obsługi maszyn. Dyrektorzy Produkcji i Utrzymania Ruchu współpracują wspólnie, aby osiągnąć jak najwyższy współczynnik OPE i OEE. Planowe konserwacje maszyn są równie ważne, jak wyprodukowanie założonej ilości produktu. Jeżeli zakład na poważnie wdraża TPM, traktuje równie poważnie sprawę napięć pomiędzy służbami utrzymania ruchu, a produkcją – między innymi poprzez zmianę premiowania, czy zmianę struktury organizacyjnej. Przede wszystkim jednak opiera się na kolejnym filarze TPM-u i systematycznie realizuje treningi i szkolenia na wszystkich szczeblach załogi.
Nie będzie TPM-u bez treningu i szkolenia
Filar ten jest spójnikiem pierwszych trzech filarów. Jeżeli nie pokażemy operatorom korzyści wynikających z autonomicznego utrzymania, może być ich trudno przekonać, że warto być odpowiedzialnym za swoją maszynę. Jeżeli kierownicy, dyrektorzy produkcji, ale i prezesi firm nie będą świadomi, jakie straty przynoszą wszelkie przestoje maszyn, nie będą skłonni zaangażować się w szerzenie idei TPM w zakładzie. W polskich realiach bardzo często spotykamy przecież sytuację zupełnie odwrotną. To prezesi i dyrektorzy nakazują zaprzestanie wykonywania napraw głównych i okresowych konserwacji, aby zmniejszyć koszty i wykazać lepszy bilans zakładu na koniec roku. Otrzeźwienie przychodzi dopiero wtedy, gdy duży klient rezygnuje z dalszych kontraktów ze względu na ciągłe opóźnienia w realizacji zamówień. Treningi i szkolenia pozwolą nie tylko na zrozumienie, jak zwiększone wydatki na utrzymanie maszyn przekładają się na lepszą jakość i szybszą produkcję, ale także mogą aktywować zarządzających do bezpośredniego udziału w warsztatach TPM. Szkolenia w dziale Utrzymania Ruchu przyczynią się natomiast do wzrostu kompetencji mechaników i techników UR. Poprzez szkolenia uzyskujemy też stałą, powolną zmianę świadomości o tym, że w zakładzie pielęgnuje się ideę ciągłego doskonalenia. Zmieniając ją na wszystkich szczeblach organizacji uzyskujemy zarządzających, którzy stają się przywódcami wzmacniającymi zaangażowanie całej załogi w doskonalenie utrzymania maszyn.
Jeżeli widzimy, że pierwsze trzy filary pomagają przedsiębiorstwu w efektywniejszej produkcji i przyczyniają się do większego zadowolenia klienta, czas pomyśleć także o tym, co będzie w przyszłości. Piąty filar TPM mówi o wczesnym planowaniu utrzymania maszyn i urządzeń. Już podczas projektowania nowej linii produkcyjnej opracowujemy sposób w jaki maszyny będą diagnozowane przez operatorów, planujemy obsługę bieżącą, przewidujemy utrzymanie niezbędnego parku części zamiennych. Maszyny dobieramy tak, aby ich diagnostyka od samego początku pomagała w autonomicznym utrzymaniu ruchu. Znając zasady TPM-u z realizowanych wcześniej warsztatów, stosujemy wzierniki ułatwiające kontrolę wrażliwych elementów, a także opracowujemy czytelne instrukcje stanowiskowe.
Zero wad produkcyjnych i pełne zaangażowanie
Jednym ze składników OEE jest ilość wyprodukowanych poprawnie elementów w stosunku do całkowitej liczby wyprodukowanych na danej maszynie. Dlatego szóstym filarem jest utrzymanie jakości. Ten filar przypomina nam o tym, że powinniśmy rozumieć, jak zużywa się maszyna i jaki wpływ ma jej stan na jakość. Poprzez współpracę z operatorami powinniśmy móc przewidywać potrzebę wymiany poszczególnych jej części. Jednym założeń TPM-u jest zrozumienie, dlaczego na maszynie są produkowane wadliwe detale oraz które z podzespołów maszyny są za te wady odpowiedzialne. Przewidywanie wystąpienia wady ze względu na zużycie się maszyny i prewencyjną wymianę powodującego wady podzespołu zapobiega powstawania błędom. W ramach działań utrzymania jakości wprowadza się także rozwiązania Poka-Yoke, które nie dopuszczają do popełnienia pomyłki po stronie operatora. Celem jest uzyskanie zera reklamacji od klienta.
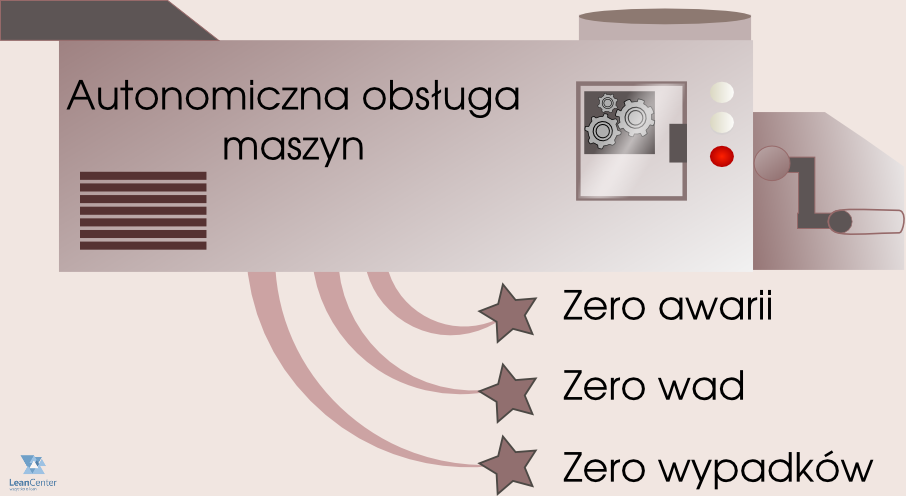
Mimo, że TPM jest kojarzony z utrzymaniem maszyn, to przedstawiciele instytutu JIPM, przekonują, że działa on naprawdę efektywnie tylko wtedy, gdy zaangażowana w jego budowę jest cała organizacja. Stąd w siódmym filarze zawarto tzw. TPM w biurach (z ang. Office TPM). Zarządzający wdrażający TPM w japońskich fabrykach doszli do wniosku, że także pracownicy biurowi oraz przede wszystkim procesy biurowe muszą przyczyniać się do wspierania produktywności, wydajności oraz identyfikacji i eliminacji strat. Muszą one być traktowane jako procesy wspierające produkcję. Poprzez szkolenia personelu biurowego, pozwalamy pracownikom widzieć lepiej relację pomiędzy produkcją, a ich pracą przy komputerach, a na dalszym etapie usprawniać przepływ informacji. W ramach TPM-u w biurach skupiamy się między innymi na wyeliminowaniu powtarzających się prac, zmniejszenia ilości dokumentów, redukcji kosztów ich magazynowania, ale również wprowadzenie zarządzania utrzymania sprzętu biurowego. Zepsuty faks, zawieszający się system, czy zacinająca się drukarka muszą być również zdiagnozowane, a ich awarie utrudniające pracę załodze – wyeliminowane.
Zakład na wysokim poziomie
Ostatni filar trzymający zakład na wysokim poziomie, to skupienie się na ochronie zdrowia, środowiska i utrzymaniu bezpiecznego miejsca pracy. Dobrze zarządzany zakład w ramach ósmego filaru TPM dąży do zera wypadków, zera pożarów i zera zranień pracowników. W ramach tych działań ponownie przyglądamy się ustalonym procesom działającym w naszej fabryce i jeśli, któryś z nich może przyczyniać się do występowania potencjalnych zagrożeń, modyfikujemy go. Jeżeli nasz zakład stoi stabilnie na pierwszym filarze (ciągłego doskonalenia), nasi pracownicy sami podpowiedzą nam, gdzie istnieje możliwość wystąpienia wypadku i jak zaradzić potencjalnie niebezpiecznej sytuacji.
Ostatecznie, możemy uznać, że TPM działa w naszym zakładzie na wysokim poziomie, gdy zgodnie z założeniami instytutu JIPM: „Osiągamy efektywne, prewencyjne utrzymanie ruchu poprzez kompleksowy system oparty na szacunku dla każdego pracownika w zakładzie i całkowitym zaangażowaniu załogi w jego doskonalenie”. Dzięki niemu wskaźnik OEE osiąga wartość minimum 90%, a w efekcie mamy dużo większą szansę na wysoką satysfakcję klienta z naszego produktu oraz zwiększenie zysków przedsiębiorstwa.
Przeczytaj również o Lean
-
Co to jest Lean Management?
Jak najprościej wyjaśnić, co to jest Lean? Skąd się wzięło to określenie? Jakie narzędzia są używane w ramach szczupłego zarządzania? W naszych zakładach coraz częściej pojawiają się nowe metody pracy i obcobrzmiące nakazy postępowania, a kierownicy i dyrektorzy mówią, że „teraz mamy Lean”. Czy tak jest naprawdę?
-
7 marnotrawstw – jak się nimi zająć
Jeśli wiemy już, czym jest 7 marnotrawstw, gdzie ich szukać i co może nam pomóc w ich eliminacji, to ustalmy jeszcze, kto powinien być zaangażowany w szukanie marnotrawstw? Odpowiedź na tak postawione pytanie jest jedna… wszyscy. Zaczynając od prezesa, który ciągnie całą załogę w stronę transformacji Lean, kończąc na podstawowym pracowniku, który podczas swojej pracy ma największą szansę na dostrz ...
-
Zmiana mentalności w procesie Lean
Wprowadzenie filozofii lean w przedsiębiorstwie to proces wieloetapowy, a zbyt pochopne wprowadzanie kolejnych jej elementów może zaważyć na mniejszej trwałości wprowadzanych zmian. Przedstawiciel Capgemini Consulting w rozmowie z dyrektorem fabryki Kellogg – Rainerem Frerichem – wskazuje na kilka istotnych zagadnień związanych ze szkoleniem personelu.
-
Kaizen - czym jest i jak działa w polskich firmach
Kaizen z jest podstawowym filarem doskonalenia firmy w ramach Lean Manufacturing - przedstawiamy przykład działania programu kaizen w przedsiębiorstwie oraz główne problemy i błędy, które pojawiają się w jego wdrożeniu?
Technologie wspierające Lean
PARTNERZY SEKCJI:
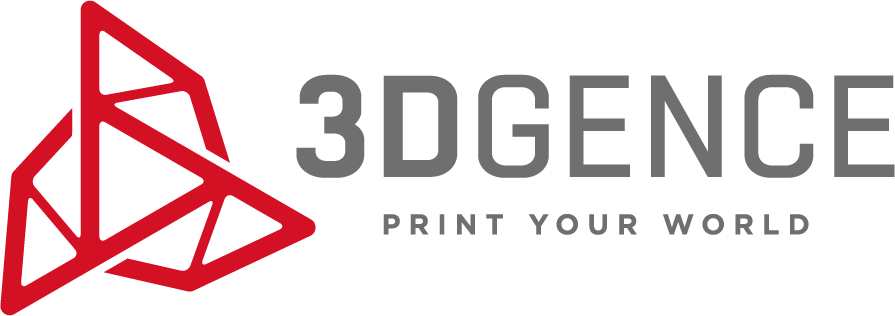
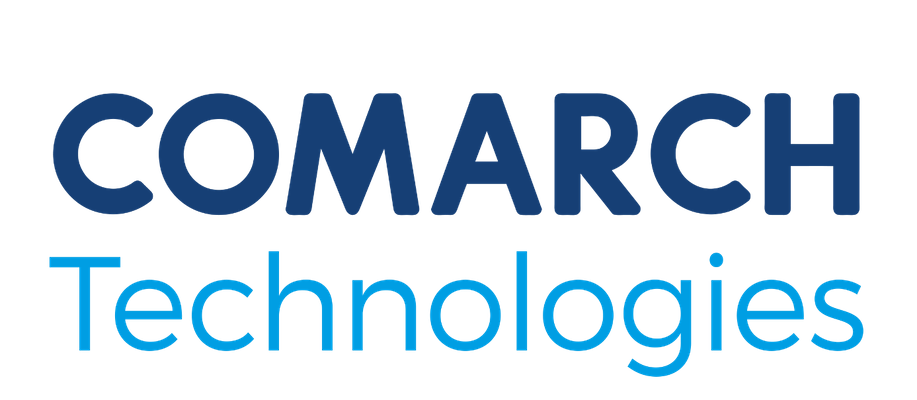
Komentarze
W dniach 14-16 maja 2025 roku w Centrum Edukacyjno-Kongresowym Politechniki Śląskiej odbędzie się Ogólnopolski Kongres Jakościowy 2025. To największe wydarzenie w Polsce poświęcone jakości, łączące wiedzę, relacje i biznes. Kongres stanowi unikalną o ...
Dziewiąta edycja Europejskiego Kongresu Lean przyniosła uczestnikom ogromną dawkę wiedzy na temat wdrażania efektywnych procesów i innowacji w różnych branżach. Organizatorzy podkreślali, że kluczowym przesłaniem wydarzenia jest przekonanie, że to, c ...
PON | WT | ŚR | CZW | PT | SOB | NDZ |
---|---|---|---|---|---|---|
1 | 2 | 3 | 4 | 5 | 6 | 7 |
8 | 9 | 10 | 11 | 12 | 13 | 14 |
15 | 16 | 17 | 18 | 19 | 20 | 21 |
22 | 23 | 24 | 25 | 26 | 27 | 28 |
29 | 30 | 1 | 2 | 3 | 4 | 5 |