Baza wiedzy Lean
Siedem marnotrawstw cz.1 – eliminuj i zyskuj
7 marnotrawstw, to:
- oczekiwanie
- zbędny transport
- zbędny ruch
- nadprocesowość
- zapasy
- wady / braki /defekty
- nadprodukcja.
Poniżej opiszemy każde z nich i podamy przykłady ich występowania.
1. Oczekiwanie
Oczekiwanie to najłatwiejsze do zauważenia marnotrawstwo. Z rozmów z pracownikami wynika, że szczególnie zarządzający zwracają uwagę na to, aby pracownik nie stał bezczynnie, utożsamiając to ze zbyt małą normą. Jednak oczekiwanie nie musi być oznaką lenistwa pracownika, ale kłopotów w firmie. Na co pracownik oczekuje marnotrawiąc cenny czas firmy?
- Na materiał – niecierpliwiąc się, gdy wózkowy nie dotarł z detalami na czas;
- Na zadziałanie systemu komputerowego – za którego wdrożenie zapłaciliśmy milion złotych i na którego nasi pracownicy są „skazani”;
- Na dokumenty, które nie dotarły od dostawcy, klienta lub z innego działu firmy;
- Na pracowników utrzymania ruchu, czy narzędziowni (bądź techników, informatyków i im podobnych) – nie działa maszyna, która zapewnia pracę. To może być zarówno tokarka, robot, podajnik, jak i drukarka, faks czy komputer;
- Na przezbrojenie maszyny – w tym przypadku można pomyśleć o zastosowaniu SMED;
- Na półprodukt z poprzedniego stanowiska pracy – Czy to oznacza, że pracownik na poprzedzającym stanowisku jest zbyt wolny i trzeba go przypilnować? Niekoniecznie. Możliwe jest, że linia jest źle zbalansowana, albo używana przez niego maszyna jest wąskim gardłem.
To tylko niektóre przykłady oczekiwania. Występuje ono za każdym razem, gdy chcemy coś zrobić, lecz nie możemy, bo jesteśmy przyhamowani przez niezależne od nas czynniki. Nie będę odkrywczy, gdy powiem, że przynajmniej połowa z nas w takiej sytuacji zaczyna narzekać. Jednak nie jest to powód do narzekania. W przedsiębiorstwie o dużej świadomości Lean, będzie to temat do dyskusji i rozpoczęcie próby naprawienia problemu – tak, aby nasz klient otrzymał produkt/usługę szybciej niż dotychczas.
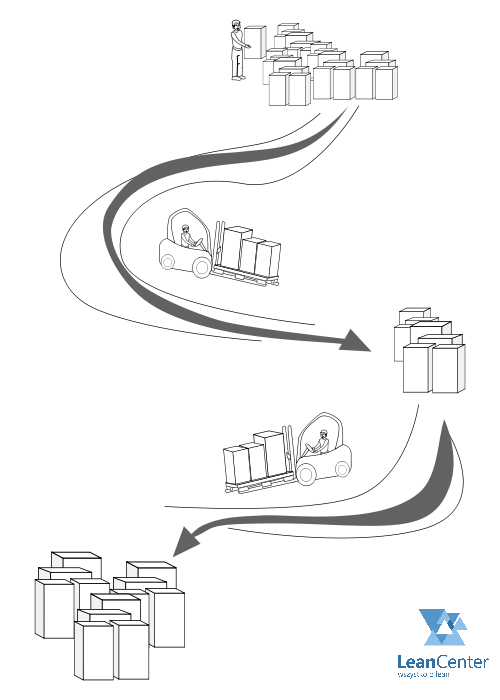
2. Zbędny transport
Co należy rozumieć przez zbędny transport? Właściwie każde przemieszczanie produktów, półproduktów, czy narzędzi. Na transport poświęcamy czas (ludzi) i pieniądze (ludzie i sprzęt). Podczas przemieszczania rzeczy narażamy się na ich zagubienie lub uszkodzenie.
Jaki rodzaj transportu jest zbędny?
- Zbyt dalekie przewożenie materiału pomiędzy magazynem, a stanowiskiem;
- Przewożenie półproduktów pomiędzy dwoma wydziałami (np. pomiędzy spawalnią i montażem);
- Przenoszenie, przewożenie materiałów pomiędzy dwoma stanowiskami pracy;
- Przenoszenie dokumentów dotyczących jednego typu spraw pomiędzy pokojami, piętrami, albo budynkami.
Jak eliminować zbędny transport? Może on być całkowicie wyeliminowany, jeżeli zastanowimy się nad ułożeniem stanowisk zgodnie ze strumieniem dodawania wartości (dodawanie wartości – to wykonywanie takich czynności, które są zgodne z oczekiwaniami klienta). Jeżeli chcemy do tematu podejść poważnie, powinniśmy być przygotowani na radykalne zmiany – na likwidację działów funkcyjnych (dział przyjmujący wniosek, dział rozpatrujący poprawność wniosku, dział rozpatrujący zasadność wniosku, itp.). Poszczególne działy powinny tworzyć jeden zespół (np. rozpatrywania kredytów), a wniosek powinien przepływać z rąk do rąk, bez tworzenia niepotrzebnych serii, przenoszonych po kilku godzinach lub dniach w kolejne miejsce. Czy mniej radykalne podejście przyniesie korzyści? Owszem, może przynieść – jednak nie osiągniemy rezultatów, które możemy uzyskać przez ustawienie stanowisk obok siebie.
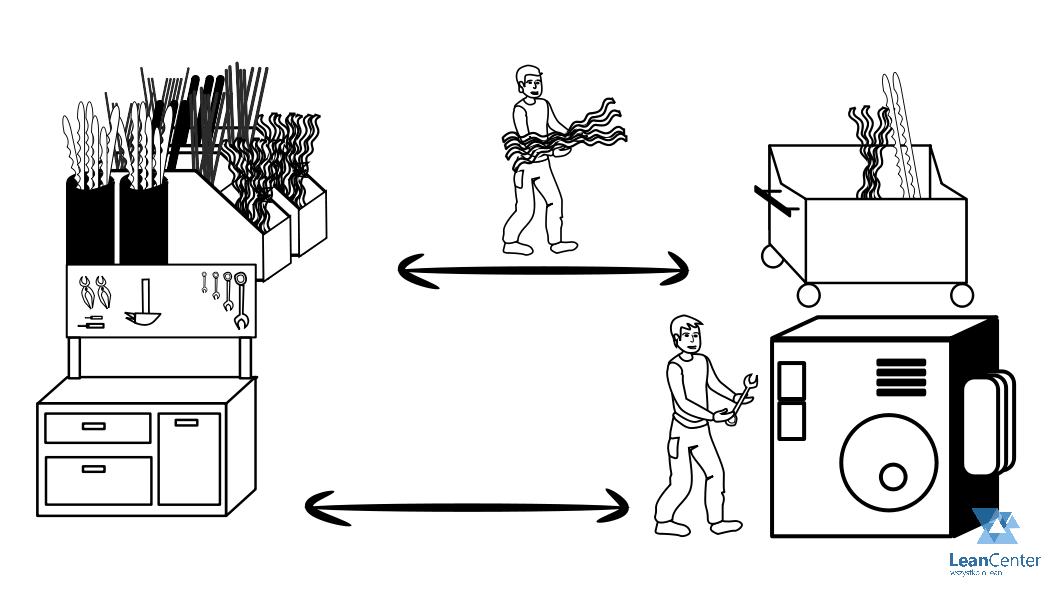
3. Zbędny ruch
To marnotrawstwo dotyczy zachowań pracownika, który każdego dnia musi wykonywać wiele ruchów lub przechodzić z miejsca na miejsce, aby realizować powierzone mu zadania. Patrząc na te zadania od strony klienta, bardzo łatwo przyznamy, że klient nie chciałby płacić za chodzenie do ksera lub krążenie po korytarzach biurowca. Jeżeli spytamy naszego pracownika, czy przeszkadza mu coś w jego pracy, może pojawić się odpowiedź dotycząca ciągłego schylania się, czy chodzenia po narzędzia lub po kolejne teczki, którymi musi się zająć. Jeżeli po pracy przychodzimy i mówimy: „Ale muszę się nagonić w tej robocie”, to znaczy, że na naszym stanowisku również można wyeliminować zbędne przemieszczanie się.
Jak możemy się go pozbyć? Całościowym podejściem będzie ponownie skupienie się na procesie wytwarzania jednego produktu/usługi (lub rodziny produktów/usług) i zlokalizowanie stanowisk w gnieździe „U”. W przypadku pojawiających się problemów w trakcie pracy są one wtedy rozwiązywane w ramach jednego wydziału. Rozpatrując zbędne przemieszczanie pod kątem jednego stanowiska pracy, sprawdźmy, czy pracownik musi ciągle się schylać lub podchodzić setki razy po dwa kroki do niezbędnych materiałów. Sytuacja może być podobna zarówno w biurach jak i na hali produkcyjnej, a zmiany wpłyną korzystnie zarówno na zadowolenie klienta, jak i pracownika.
W części drugiej przedstawiamy Nadprocesowość i wady.
Przeczytaj również o Lean
-
Kaizen - czym jest i jak działa w polskich firmach
Kaizen z jest podstawowym filarem doskonalenia firmy w ramach Lean Manufacturing - przedstawiamy przykład działania programu kaizen w przedsiębiorstwie oraz główne problemy i błędy, które pojawiają się w jego wdrożeniu?
-
Sprawna logistyka, a redukcja zapasów magazynowych
Redukcja bieżących zapasów jest jednym z etapów organizacji przedsiębiorstwa opartych na założeniach lean manufacturing. Zmniejszenie kosztów magazynowania osiągniemy między innymi przez usprawnienie procesów logistycznych. Jednym ze sposobów na oszczędności jest zlecenie organizacji logistyki firmie zewnętrznej.
-
Dostawy Milk Run – etap planowania
Dobry plan to podstawa skutecznego projektu, dobrze zaprojektowany Milk Run to spokój w zaopatrywaniu naszej produkcji. Jak w każdym przypadku, tak i w sytuacji dostaw w układzie mleczarza powodzenie tkwi w szczegółach i w dobrym planowaniu. W niniejszym artykule przedstawione zostaną elementy, na które należy zwrócić uwagę podczas projektowania efektywnych tras Milk Run.
-
Opłacalna inwestycja w Lean Healthcare. W szpitalach w Kanadzie, jak w Toyocie.
Ministerstwo Zdrowia w Quebecu zorganizowało projekt inwestycyjny "Lean Healthcare Six Sigma". Wybrano trzy szpitale, które otrzymały prawie 10 milionów dolarów na realizację „szczupłego” zarządzania metodą Systemu Produkcyjnego Toyoty.
Technologie wspierające Lean
PARTNERZY SEKCJI:
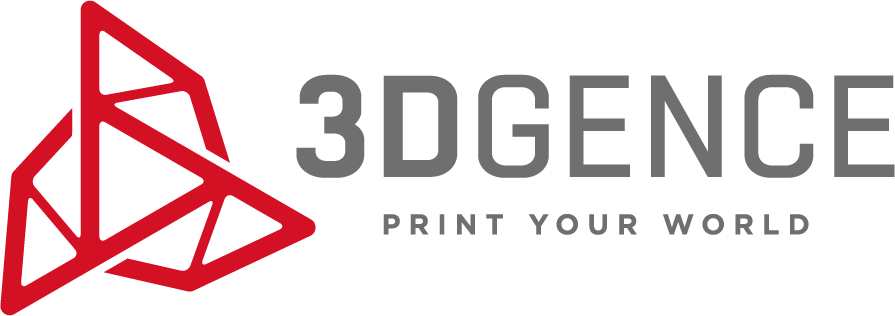
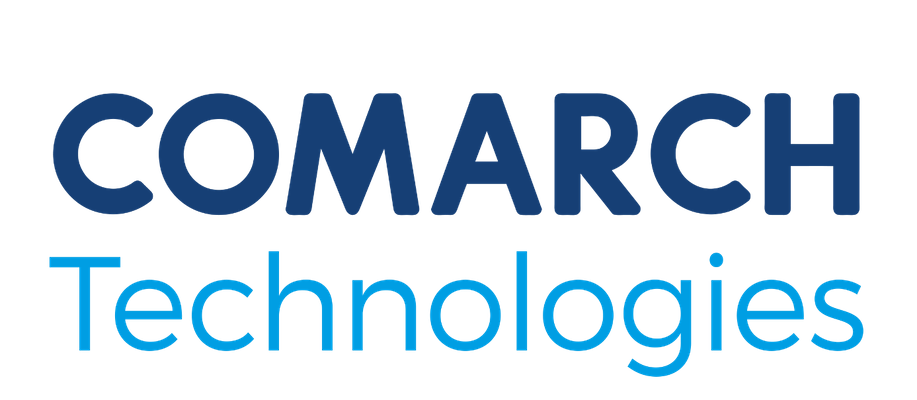
Komentarze
W dniach 14-16 maja 2025 roku w Centrum Edukacyjno-Kongresowym Politechniki Śląskiej odbędzie się Ogólnopolski Kongres Jakościowy 2025. To największe wydarzenie w Polsce poświęcone jakości, łączące wiedzę, relacje i biznes. Kongres stanowi unikalną o ...
Dziewiąta edycja Europejskiego Kongresu Lean przyniosła uczestnikom ogromną dawkę wiedzy na temat wdrażania efektywnych procesów i innowacji w różnych branżach. Organizatorzy podkreślali, że kluczowym przesłaniem wydarzenia jest przekonanie, że to, c ...