Baza wiedzy Lean
Pięć kroków 5S dla lepszych warunków pracy
Zobacz także: 5S w pigułce (infografika)
Poniżej omówimy każdy z kroków 5S:
1. Segregacja (jap. Seiri) – najpierw rozejrzyjmy się po stanowisku pracy. Czy są tu narzędzia, których obecność od dawna nas irytowała, albo trzymamy je tylko po to, bo kiedyś mogą się przydać – ale nie użyliśmy ich od roku? Czy półprodukty/detale potrzebne nam do pracy są zawsze łatwo dostępne. Czy musimy ich szukać? Jeśli pracujemy w biurze, to czy dokumenty są pomieszane? Czy łatwo możemy zidentyfikować, których dokumentów mamy najwięcej i które są najbardziej pilne? Czy układ folderów w naszym komputerze ułatwia nam czy utrudnia pracę? Może musimy klikać na kolejne foldery w poszukiwaniu potrzebnych dokumentów. Przejdźmy zatem do działań w ramach pierwszego „S”.
Segregacja może odbywać się zespołowo. Osoby, które w niej uczestniczą są wyposażane np. w czerwone kartki lub kokardy. Przyklejają je na każdy przedmiot, który wg ich opinii nie powinien znajdować się na danym stanowisku pracy. Pracownik, który pracuje na rozpatrywanym stanowisku pracy, może wytłumaczyć, do czego i jak często używa danego narzędzia lub detalu. Następnie przedmioty są usuwane ze stanowiska. Część z nich może być tymczasowo przeniesiona do tzw. czerwonego pola, z którego z powrotem można je zabrać, jeśli okazują się niezbędne do pracy. W tym etapie przyglądamy się także wszelkim detalom (lub w biurach: dokumentom), które w zbyt dużej ilości zostały przesłane z poprzednich operacji. Zrozumienie, dlaczego one leżą na danym stanowisku pomoże w późniejszej eliminacji nadprodukcji i upłynnieniu pracy w danym gnieździe.
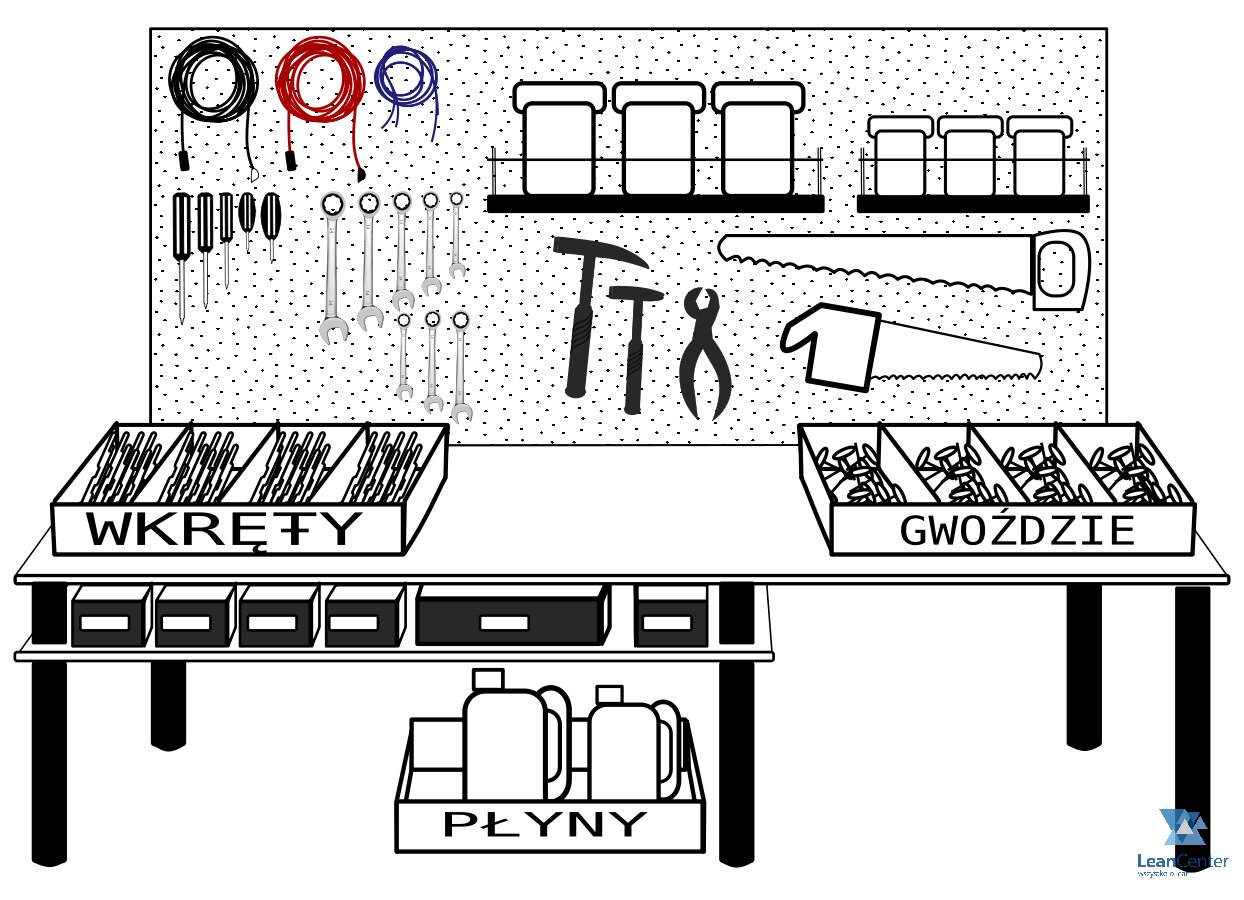
2. Systematyka (jap. Seiton) – W drugim kroku 5S znajdujemy miejsce na wszystkie rzeczy, które pozostały na stanowisku pracy po pierwszym etapie. Musimy potraktować poważnie ten etap Ważne będzie ułożenie każdego narzędzia, każdej skrzynki, detalu, czy butelki z płynem. Na tym stanowisku pracy musi nam się po prostu dobrze pracować, a utrzymanie porządku powinno być naturalne. Miejsca, które przeznaczymy na narzędzia muszą nam jasno pokazywać, czy dane narzędzie jest tam, gdzie powinno leżeć. Musimy wszyscy pomyśleć, jak zorganizować je najlepiej, zobaczyć jak pracuje operator i czy zaproponowane ułożenie będzie optymalne pod względem ergonomii. Przygotowujemy także wstępne opisy miejsc, wyrysowujemy tymczasowe tablice cieni i pola odkładcze.
Jeśli jestem operatorem na danym stanowisku, Jako pracownik zdaję sobie sprawę, że od dzisiaj zawsze po skończonej pracy moje stanowisko pracy będzie wyglądać tak samo. Zamiast położyć narzędzie, gdzie popadnie, będę je odkładał zawsze w to samo miejsce, które jest jasno zaznaczone na moim stanowisku. Brygadzista jednocześnie musi być otwarty na ewentualnie pojawiające się uwagi ze strony pracownika i pracuje z nim nad jeszcze lepszym ułożeniem stanowiska.
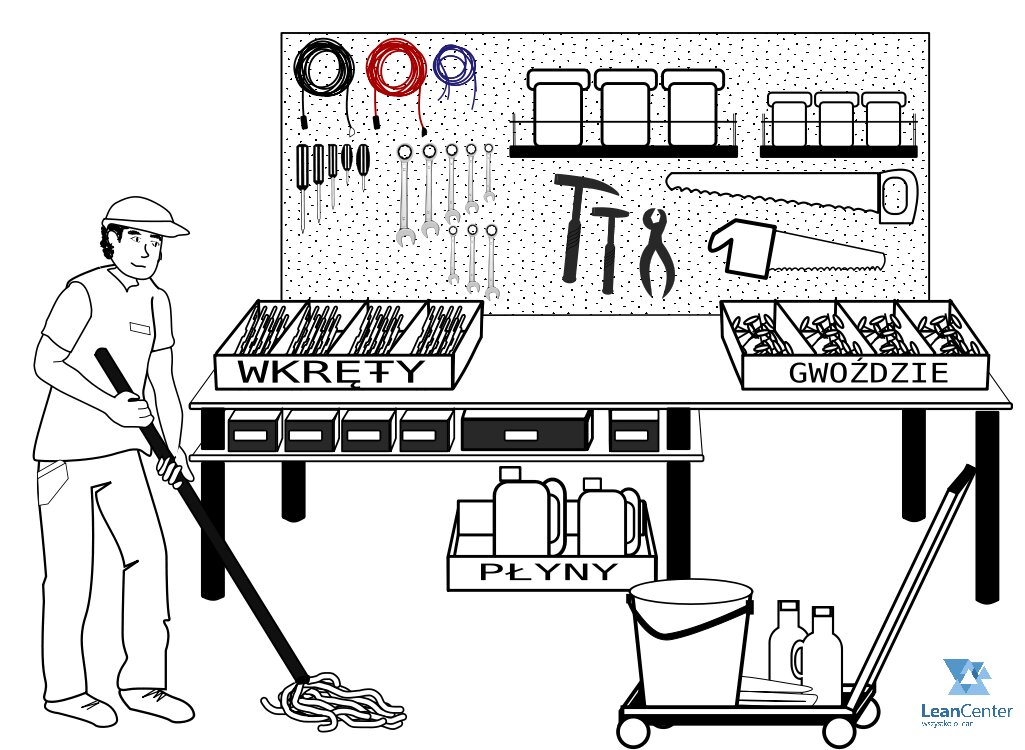
3. Sprzątanie (jap. Seiso) – W końcu pojawia się słowo sprzątanie. Wcześniej skupiliśmy się na wszystkich rzeczach, które znajdowały się na naszym stanowisku pracy, teraz sprawimy, że wszystko będzie lśniło blaskiem nowości. Czyścimy narzędzia, podłogi, stoły, maszynę. Działamy dalej w grupie. Jest razem z nami technik utrzymania ruchu, który widzi ewentualne wycieki na obudowie maszyny, bądź podłodze. Kiedy wyczyścimy maszynę, będziemy mogli obserwować, gdzie się brudzi i zastanowić, czy nie jest to zapowiedź poważniejszej awarii. Być może Dział Utrzymania Ruchu przygotowuje się także do warsztatów TPM, podczas których sprawdzą i opiszą tę maszynę jeszcze dokładniej. W ramach trzeciego kroku 5S można podjąć także malowanie stanowiska pracy. Satysfakcja z przeprowadzonych zmian jest bardzo duża. Raczej będę dbał o swoje „nowe” stanowisko pracy. Od dzisiaj codziennie po skończonej pracy będę je czyścił.
A jak zarządzający mogą pomóc w utrzymaniu porządku? W zakładach o wysokiej świadomości i kulturze ostatnie 5-10 minut pracy poświęcone jest na uprzątnięcie stanowiska (także na liniach produkcyjnych). Pierwsze sprzątanie w ramach 5S trwa najdłużej, następnie jest to już utrzymanie czystości. Jeśli utrzymanie porządku jest trudne, oznacza to, że nie do końca dobrze przemyśleliśmy kwestię organizacji stanowiska pracy. Spróbujmy także pomyśleć o rozwiązaniu, które sprawi, że odpadki z produkcji (wióry) będą spadały od razu tylko w jedno miejsce (do pojemnika). Jeśli podłoga jest poplamiona przez wycieki z maszyn, to znaczy, że czas poszukać także powodów jej nieszczelności. Traktując w ten sposób 5S, sprzątanie nie będzie męczącą koniecznością, ale oczywistym, w miarę krótkim zabiegiem. Aby pomóc gruntownym utrzymaniu porządku, w niektórych zakładach, linia cyklicznie (raz w tygodniu lub raz w miesiącu) staje na 4 lub 8 godzin i wszyscy pracownicy sprzątają swój wydział, a technicy Działu Utrzymania Ruchu mają czas na wykonanie planowej konserwacji maszyn.
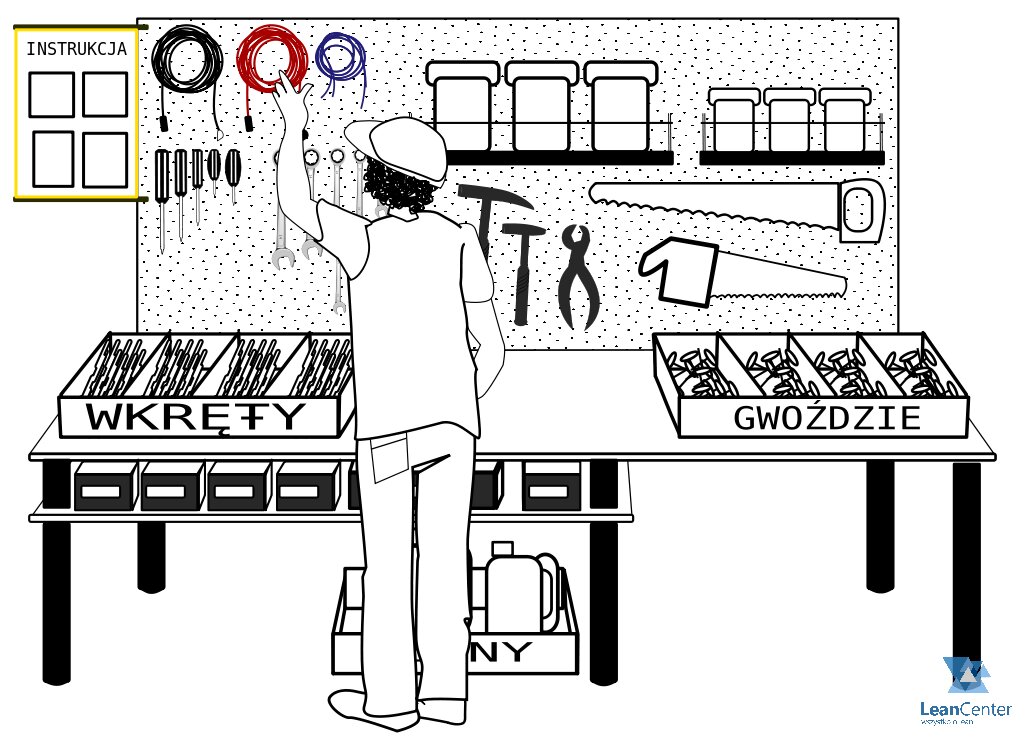
4. Standaryzacja (jap. Seiketsu) – W tym etapie określamy, jak będzie wyglądało stale nasze stanowisko pracy. W pierwszym kroku 5S usunęliśmy niepotrzebne rzeczy ze stanowiska, w drugim zastanowiliśmy się jak będą ułożone te, które na nim pozostały i jak będziemy pracować na naszym stanowisku. W trzecim kroku wszystko umyliśmy i posprzątaliśmy. Widzimy już efekt naszych prac. Jeśli jesteśmy gotowi do czwartego „S”, akceptujemy wszystkie nasze poprzednie prace i staramy się wykonywać wszystko zgodnie z ustaleniami. Na stanowisku wieszamy wizualne informacje na temat sposobu pracy, ułożenia półproduktów i narzędzi. Są to łatwe do zrozumienia i skontrolowania instrukcje w postaci zdjęć. Są to przede wszystkim standardy wykonywania naszej pracy i wyglądu stanowiska.
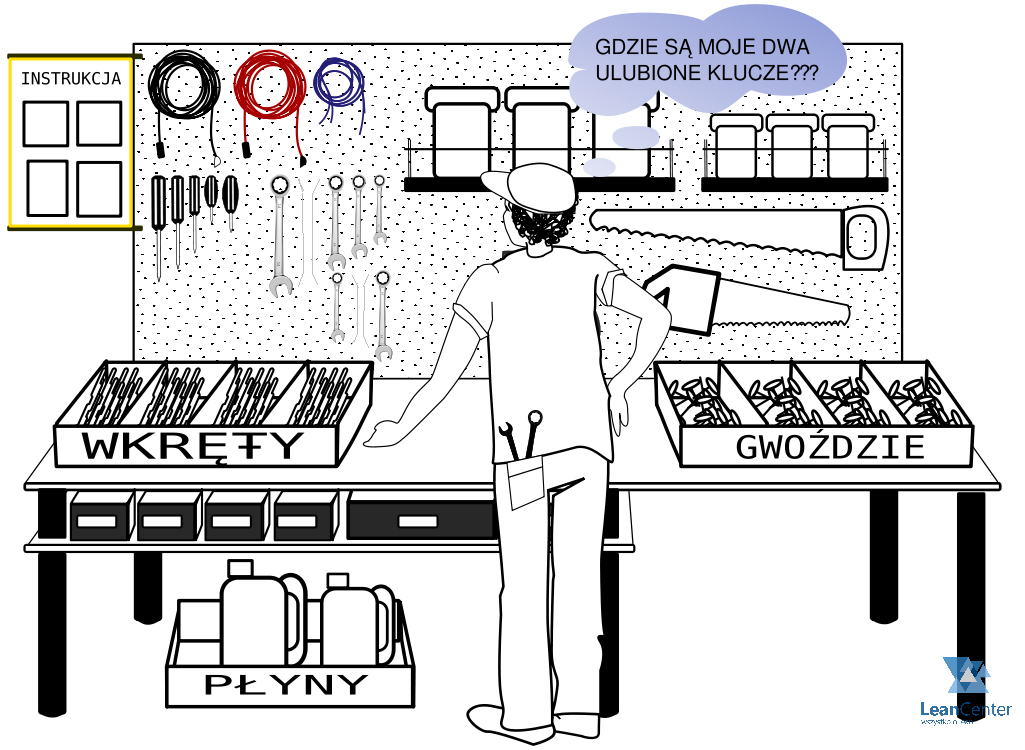
5. Samodyscyplina (jap. Shitsuke) – Piąte „S”. Teoretycznie możemy się cieszyć, że w końcu jesteśmy u celu. Rzeczywiście tak jest, ale tylko częściowo. Przeszliśmy przez wszystkie poprzednie cztery etapy i stanowisko pracy wygląda tak dobrze, że aż chciałoby się pochwalić rodzinie schludnym miejscem pracy. Jednak jednocześnie ostatni etap 5S jest początkiem dalszej drogi. Ostatnie „S” odnosi się bowiem do naszych przyzwyczajeń i naszych starań, aby ustandaryzowane stanowisko pracy wyglądało zawsze tak samo schludnie.
Jeśli na początku nie wychodzi nam utrzymywanie porządku, starajmy sobie częściej przypominać o tym, że przyjęliśmy pewien standard. Nasza praca jest teraz na wysokim poziomie, a mi pracuje się łatwiej i lepiej, gdy wokół jest czysto i wszystko znajduję na miejscu. Trudniej popełnić błędy i łatwiej mogę wykryć marnotrawstwa. Teraz nie muszę już tracić czasu na szukanie narzędzi. Mogę też pomyśleć, jak jeszcze bardziej ułatwić sobie pracę. To nic, że wiszą instrukcje i wszystko wokół jest już oklejone. W ramach piątego „S” mogę to wszystko udoskonalić. To nie tylko samodyscyplina w utrzymywaniu standardu, ale też samodoskonalenie. Jeśli z jakichś powodów nie pracuje mi się dobrze i wiem jak będzie lepiej – zgłoszę pomysł przełożonemu, albo wypiszę wniosek ciągłego doskonalenia Kaizen. Narzędzia, dokumenty lub pojemniki przestawimy z przełożonym. Zrobimy nowe instrukcje. Będzie mi jeszcze łatwiej utrzymać porządek i dobrą jakość mojej pracy.
Przygoda z 5S trwa nadal. Wprowadzone audyty 5S pomagają w utrzymaniu schludnego stanowiska pracy. Wspierający przełożony inspiruje nas do dalszej pracy. Jeśli nie jest tak w twojej firmie, zapoznaj się z poniższym artykułem.
Przeczytaj kolejny artykuł: Rola zarządzających we wdrożeniu 5S
Przeczytaj również o Lean
-
Co Scrum ma wspólnego z Lean?
Scrum (z ang. młyn w rugby) powstał na początku lat 90 XX wieku. Wywodzi się ze świata programistów komputerowych borykających się ze zmiennością potrzeb i wymagań klienta, niską terminowością realizowanych projektów, a także rozbieżnościami między wynikiem projektu a oczekiwaniami klienta. Obecnie Scrum przenika także do innych branż ciesząc się dużym powodzeniem z powodu swej skuteczności. ...
-
Lean Green – zredukuj koszty odpadów, energii i wody
Wzrost cen odbioru odpadów, zakupu energii, wody oraz surowców staje się wyzwaniem dla wielu firm tym bardziej, że przy globalnym rynku i masowej konsumpcji napędzanej przez rodzące się kolejne miliardy nowych klientów z klasy średniej nie ma co liczyć na obniżki cen. Aby mimo to zachować konkurencyjność cen oferowanych produktów, przedsiębiorcy powinni rozbudowywać swoje systemy Lean o elementy s ...
-
5S w pigułce - infografika
Przedstawiamy kroki 5S, w krótkiej, łatwej do zapamiętania formie. Jakie są kroki 5S? Co daje nam ich utrzymywanie? Odpowiedź na poniższej infografice.
-
Metoda A3
A3 wedlug John Shook’a w książce „ Zarządzać znaczy uczyć”.
Technologie wspierające Lean
PARTNERZY SEKCJI:
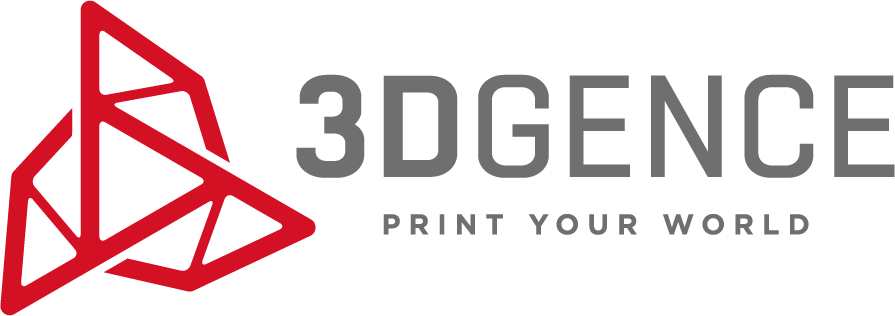
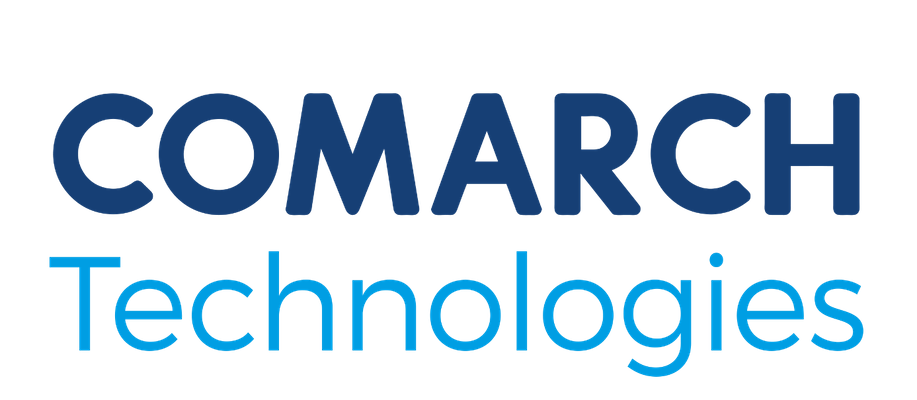
Komentarze
W dniach 14-16 maja 2025 roku w Centrum Edukacyjno-Kongresowym Politechniki Śląskiej odbędzie się Ogólnopolski Kongres Jakościowy 2025. To największe wydarzenie w Polsce poświęcone jakości, łączące wiedzę, relacje i biznes. Kongres stanowi unikalną o ...
Dziewiąta edycja Europejskiego Kongresu Lean przyniosła uczestnikom ogromną dawkę wiedzy na temat wdrażania efektywnych procesów i innowacji w różnych branżach. Organizatorzy podkreślali, że kluczowym przesłaniem wydarzenia jest przekonanie, że to, c ...