Projekty Lean
Od 10 zasad Kaizen do projektu SixSigma
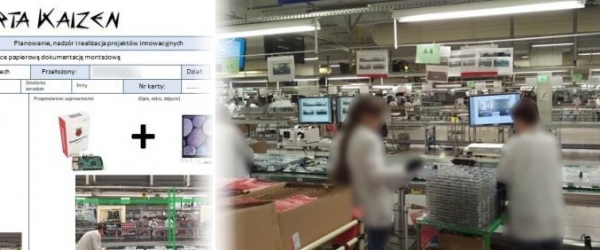
Jeżeli w swoich zespołach nie zauważyliście jeszcze, że drobne usprawnienia, pomysły jak np. Kaizen mogą otworzyć drogę do dużego projektu to ten artykuł jest jak najbardziej dla Was.
Przedstawię w pigułce, jak jeden z pomysłów, który został zgłoszony w zespole, którym zarządzam - uruchomił zaawansowany projekt. Jego efektem były duże oszczędności i zmiana jakościowa w pracy zakładu.
10 zasad Kaizen – na początek
Kaizen to ciągłe doskonalenie, które opiera się na pewnych dziesięciu zasadach przewodnich, zdefiniowanych przez Masaakiego Imai1:
1. Odrzuć konwencjonalny, mało elastyczny sposób myślenia na temat produkcji.
2. Myśl o tym, jak coś zrobić, a nie dlaczego nie można tego wykonać.
3. Nie szukaj wymówek. Zacznij od podania w wątpliwość istniejących praktyk.
4. Nie szukaj ideału. Rozwiązania wdrażaj natychmiast, nawet jeśli osiągniesz cel tylko w 50%.
5. Od razu popraw błędy.
6. Nie wydawaj pieniędzy na Kaizen.
7. Zdobędziesz wiedzę, kiedy zmierzysz się z przeciwnościami losu.
8. Pytaj „Dlaczego?” pięć razy i szukaj przyczyn problemu.
9. Polegaj na mądrości dziesięciu osób bardziej niż na wiedzy jednej osoby.
10. Pamiętaj, że możliwości Kaizen są nieskończone.
Tuż przed inwestycją
W tym
przypadku dokładnie od tego się zaczęło. Wstępnie prosto wyglądająca idea, prosty pomysł usprawniający sposób dystrybucji dokumentacji technicznej. Początkowo wydawało się, że sprawa jest na tyle oczywista, iż można tak po prostu przystąpić do realizacji. Jednak po dłuższym zastanowieniu się stwierdziliśmy, że temat należy dokładniej przeanalizować, tak aby nie popełnić błędu związanego z inwestycją jaka w tym przypadku była konieczna.
W momentach takich jak ten, z pomocą przychodzi nam jedna z metod stosowana w projektach SixSigma. Mowa tu o DMAIC – metodzie optymalizacji procesów pozwalającej rozwiązywać problemy poprzez dogłębną analizę statystyczną w oparciu o fakty.
Mierzymy, sprawdzamy
Do rzeczy zatem… Powołaliśmy zespół, który ostatecznie zdefiniował na czym polega problem związany z dystrybucją dokumentacji. Klientem w tym przypadku jest dział produkcji, który powinien otrzymać dokumentację najwyższej jakości w najkrótszym czasie. To są elementy, które postanowiliśmy zmierzyć. Czas dystrybucji dokumentacji oraz jej jakość. Początkowo bez zebrania danych, wydawało nam się że najkosztowniejszym elementem tego procesu jest ilość papieru jaka jest zużywana w procesie przygotowywania materiałów. Byliśmy w błędzie. Mimo, że zużycie papieru było ogromne kluczowym elementem strat był czas dystrybucji dokumentacji do poszczególnych operatorów oraz jej jakość.
Po zdefiniowaniu faktycznych strat i określeniu CTQ przystąpiliśmy do pomiaru strat. Mimo, że ilość zużywanego papieru nie była kluczowa postanowiliśmy ją także przeliczyć. W końcu, mimo że to niewielki koszt, powinien został całkowicie wyeliminowany. To było dość proste. Większym wyzwaniem był pomiar czasu jaki był potrzebny do przygotowania i rozdystrybuowania dokumentacji. Zebrane dane z całego miesiąca pozwoliły na przeanalizowanie kosztów jakie związane są z tak zorganizowanym procesem.
Wizualizacja on-line
Kolejnym krokiem było dokonanie pewnych założeń związanych z realizacją pomysłu zastąpienia drukowanej dokumentacji wyświetlaniem jej na TV zainstalowanych w gniazdach produkcyjnych. Pozwoliły one na dokonanie kalkulacji i wyliczenie potencjalnego czasu zwrotu inwestycji.

Inwestycja, w naszym przypadku okazała się nie być dużym kosztem. To jest także jeden z elementów, który pozwala na zakończenie powodzeniem prowadzonych w przedsiębiorstwach projektów lean. Multifunkcjonalne zespoły o szerokich kompetencjach, które pozwalają na realizację wypracowanych usprawnień we własnym zakresie. Zaprojektowany system informatyczny, wykonany został przez jedną z osób z zespołu. Uchwyty do TV połączone z półkami, na których układamy komponenty potrzebne w produkcji. To wszystko wpłynęło na stosunkowo niewielką inwestycję.
Ołówek i doskonalenie rozwiązań
Narzędzia CAD nie zawsze są potrzebne. W naszym przypadku posługiwaliśmy się często ołówkiem, długopisem i kartką papieru. Wspólnie wypracowany na spotkaniach zespołu projekt był prostą i tanią konstrukcją, która zapewniała przy okazji wyświetlania dokumentacji, podporę dla komponentów potrzebnych w procesie, o czym wspomniałem powyżej.
Istotną częścią rozwiązania był system informatyczny, który pozwolił na dystrybucję dokumentacji w poszczególne gniazda. Sięgnęliśmy także do prostego i niekosztownego rozwiązania. Wykorzystaliśmy istniejącą infrastrukturę sieci komputerowej, darmowy serwer www oraz prostą stronę internetową.
Kluczem do sukcesu w tym przypadku okazały się proste i tanie rozwiązania, które po wdrożeniu miały pozwolić zaoszczędzić czas. Czas to najbardziej kosztowny element procesu dystrybucji dokumentacji, co potwierdziło się po zakończeniu analizy i policzeniu kosztów.
Wdrożenie w gemba
Tym sposobem dotarliśmy do przedostatniej fazy metodyki, to jest wdrożeniu usprawnień. Zrealizowaliśmy instalację systemu dystrybucji i wyświetlania dokumentacji na jednej linii produkcyjnej. Wdrożenie i szkolenia trwały jeden miesiąc. Po upewnieniu się, że wszystko działa poprawnie, system jest stabilny, podjęliśmy ostatni etap projektu, czyli kontrolę. Należało sprawdzić, czy wdrożone rozwiązanie przynosi korzyści.

Już w pierwszym miesiącu po wdrożeniu wykazaliśmy oszczędności dzięki którym mogliśmy rozpocząć pracę nad wdrożeniem systemu na kolejne linie produkcyjne. Obecnie pracujemy nad wdrożeniem systemu na ostatnią, czwartą linię produkcyjną.

W fazie wdrożenia korzystamy z obu systemów, „starego” i nowego. Ważne w każdym wdrożeniu jest to, aby funkcjonujący proces produkcyjny nie przestawał działać o ile jest to oczywiście możliwe.
Korekta, to nie błąd
Metoda DMAIC, która jest jedną z tych wykorzystywanych w projektach SixSigma, mimo iż jest bardzo rozbudowana świetnie sprawdza się w małych projektach jak ten. Ważnym jest aby nie omijać żadnej z jej faz. Ostatnia, która pozwala kontrolować wdrożone usprawnienia, szybko wskazuje na ewentualne błędy w założeniach teoretycznych. Dzięki temu można szybko wycofać się z wdrożeń nietrafionych rozwiązań i poprawić je, tak aby osiągnąć zakładane poprawienie wcześniej zmierzonych wartości.
Źródło:
1. Masaaki Imai, Gemba Kaizen – Zdroworozsądkowe, niskokosztowe podejście do zarządzania Warszawa: Wydawnictwo MT Biznes, 2006, ISBN 83-88970-77-1, s. 129.
10 zasad Kaizen – na początek
Kaizen to ciągłe doskonalenie, które opiera się na pewnych dziesięciu zasadach przewodnich, zdefiniowanych przez Masaakiego Imai1:
1. Odrzuć konwencjonalny, mało elastyczny sposób myślenia na temat produkcji.
2. Myśl o tym, jak coś zrobić, a nie dlaczego nie można tego wykonać.
3. Nie szukaj wymówek. Zacznij od podania w wątpliwość istniejących praktyk.
4. Nie szukaj ideału. Rozwiązania wdrażaj natychmiast, nawet jeśli osiągniesz cel tylko w 50%.
5. Od razu popraw błędy.
6. Nie wydawaj pieniędzy na Kaizen.
7. Zdobędziesz wiedzę, kiedy zmierzysz się z przeciwnościami losu.
8. Pytaj „Dlaczego?” pięć razy i szukaj przyczyn problemu.
9. Polegaj na mądrości dziesięciu osób bardziej niż na wiedzy jednej osoby.
10. Pamiętaj, że możliwości Kaizen są nieskończone.
Tuż przed inwestycją
W tym

W momentach takich jak ten, z pomocą przychodzi nam jedna z metod stosowana w projektach SixSigma. Mowa tu o DMAIC – metodzie optymalizacji procesów pozwalającej rozwiązywać problemy poprzez dogłębną analizę statystyczną w oparciu o fakty.
Mierzymy, sprawdzamy
Do rzeczy zatem… Powołaliśmy zespół, który ostatecznie zdefiniował na czym polega problem związany z dystrybucją dokumentacji. Klientem w tym przypadku jest dział produkcji, który powinien otrzymać dokumentację najwyższej jakości w najkrótszym czasie. To są elementy, które postanowiliśmy zmierzyć. Czas dystrybucji dokumentacji oraz jej jakość. Początkowo bez zebrania danych, wydawało nam się że najkosztowniejszym elementem tego procesu jest ilość papieru jaka jest zużywana w procesie przygotowywania materiałów. Byliśmy w błędzie. Mimo, że zużycie papieru było ogromne kluczowym elementem strat był czas dystrybucji dokumentacji do poszczególnych operatorów oraz jej jakość.
Po zdefiniowaniu faktycznych strat i określeniu CTQ przystąpiliśmy do pomiaru strat. Mimo, że ilość zużywanego papieru nie była kluczowa postanowiliśmy ją także przeliczyć. W końcu, mimo że to niewielki koszt, powinien został całkowicie wyeliminowany. To było dość proste. Większym wyzwaniem był pomiar czasu jaki był potrzebny do przygotowania i rozdystrybuowania dokumentacji. Zebrane dane z całego miesiąca pozwoliły na przeanalizowanie kosztów jakie związane są z tak zorganizowanym procesem.
Wizualizacja on-line
Kolejnym krokiem było dokonanie pewnych założeń związanych z realizacją pomysłu zastąpienia drukowanej dokumentacji wyświetlaniem jej na TV zainstalowanych w gniazdach produkcyjnych. Pozwoliły one na dokonanie kalkulacji i wyliczenie potencjalnego czasu zwrotu inwestycji.

Inwestycja, w naszym przypadku okazała się nie być dużym kosztem. To jest także jeden z elementów, który pozwala na zakończenie powodzeniem prowadzonych w przedsiębiorstwach projektów lean. Multifunkcjonalne zespoły o szerokich kompetencjach, które pozwalają na realizację wypracowanych usprawnień we własnym zakresie. Zaprojektowany system informatyczny, wykonany został przez jedną z osób z zespołu. Uchwyty do TV połączone z półkami, na których układamy komponenty potrzebne w produkcji. To wszystko wpłynęło na stosunkowo niewielką inwestycję.
Ołówek i doskonalenie rozwiązań

Istotną częścią rozwiązania był system informatyczny, który pozwolił na dystrybucję dokumentacji w poszczególne gniazda. Sięgnęliśmy także do prostego i niekosztownego rozwiązania. Wykorzystaliśmy istniejącą infrastrukturę sieci komputerowej, darmowy serwer www oraz prostą stronę internetową.
Kluczem do sukcesu w tym przypadku okazały się proste i tanie rozwiązania, które po wdrożeniu miały pozwolić zaoszczędzić czas. Czas to najbardziej kosztowny element procesu dystrybucji dokumentacji, co potwierdziło się po zakończeniu analizy i policzeniu kosztów.
Wdrożenie w gemba
Tym sposobem dotarliśmy do przedostatniej fazy metodyki, to jest wdrożeniu usprawnień. Zrealizowaliśmy instalację systemu dystrybucji i wyświetlania dokumentacji na jednej linii produkcyjnej. Wdrożenie i szkolenia trwały jeden miesiąc. Po upewnieniu się, że wszystko działa poprawnie, system jest stabilny, podjęliśmy ostatni etap projektu, czyli kontrolę. Należało sprawdzić, czy wdrożone rozwiązanie przynosi korzyści.

Już w pierwszym miesiącu po wdrożeniu wykazaliśmy oszczędności dzięki którym mogliśmy rozpocząć pracę nad wdrożeniem systemu na kolejne linie produkcyjne. Obecnie pracujemy nad wdrożeniem systemu na ostatnią, czwartą linię produkcyjną.

W fazie wdrożenia korzystamy z obu systemów, „starego” i nowego. Ważne w każdym wdrożeniu jest to, aby funkcjonujący proces produkcyjny nie przestawał działać o ile jest to oczywiście możliwe.
Korekta, to nie błąd
Metoda DMAIC, która jest jedną z tych wykorzystywanych w projektach SixSigma, mimo iż jest bardzo rozbudowana świetnie sprawdza się w małych projektach jak ten. Ważnym jest aby nie omijać żadnej z jej faz. Ostatnia, która pozwala kontrolować wdrożone usprawnienia, szybko wskazuje na ewentualne błędy w założeniach teoretycznych. Dzięki temu można szybko wycofać się z wdrożeń nietrafionych rozwiązań i poprawić je, tak aby osiągnąć zakładane poprawienie wcześniej zmierzonych wartości.
Źródło:
1. Masaaki Imai, Gemba Kaizen – Zdroworozsądkowe, niskokosztowe podejście do zarządzania Warszawa: Wydawnictwo MT Biznes, 2006, ISBN 83-88970-77-1, s. 129.
Technologie wspierające Lean
PARTNERZY SEKCJI:
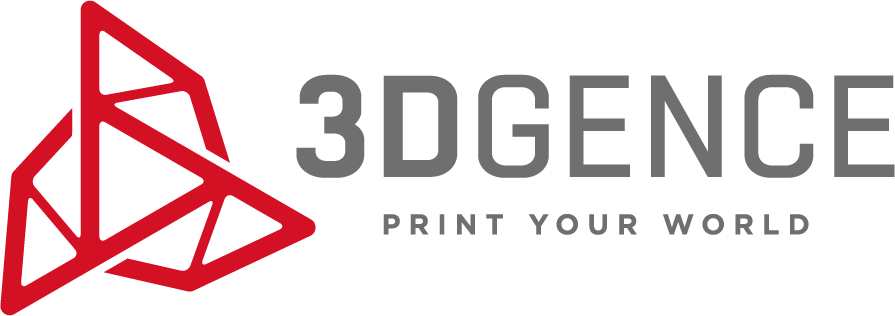
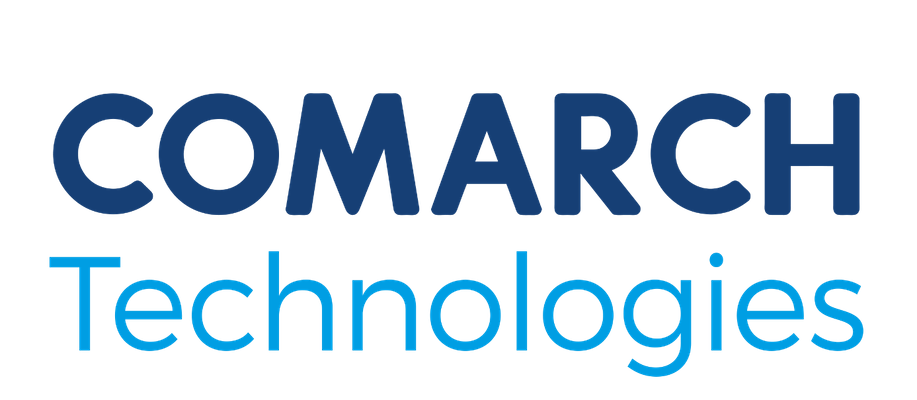
Śledź nas w social media
Aktualności
Ogólnopolski Kongres Jakościowy 2025: Wiedza. Relacje. Biznes.
Nowoczesne podejście do doskonalenia procesów - relacja z IX Europejskiego Kongresu Lean
PolecamyW dniach 14-16 maja 2025 roku w Centrum Edukacyjno-Kongresowym Politechniki Śląskiej odbędzie się Ogólnopolski Kongres Jakościowy 2025. To największe wydarzenie w Polsce poświęcone jakości, łączące wiedzę, relacje i biznes. Kongres stanowi unikalną o ...
Dziewiąta edycja Europejskiego Kongresu Lean przyniosła uczestnikom ogromną dawkę wiedzy na temat wdrażania efektywnych procesów i innowacji w różnych branżach. Organizatorzy podkreślali, że kluczowym przesłaniem wydarzenia jest przekonanie, że to, c ...
Kalendarz konferencji Lean
Patronujemy Wyszukiwarka
Śledź nas na Facebooku