Technologie wspierające Lean
Technologia, która wykluczy używanie baterii? W niektórych warunkach... tak.
Dodano: 2021-07-14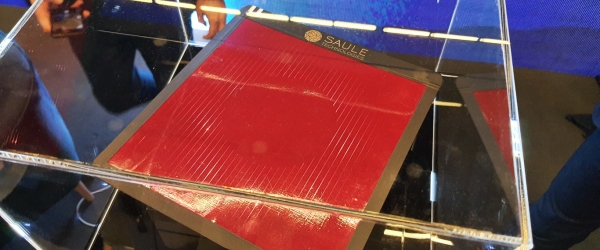
Olga Malinkiewicz: Nikt dotąd nie produkował perowskitowych ogniw fotowoltaicznych. Wcześniej testowaliśmy je co prawda w warunkach naturalnych, na przykład na biurowcu Skanska w Warszawie, a także w Japonii, ale otwarta przez nas w maju we Wrocławiu fabryka jest pierwszą tego typu na świecie. Możemy więc śmiało powiedzieć, że jest to rynkowy debiut technologii perowskitowej.
Otwiera się przed nami duże pole do działania. Jest wiele możliwości zastosowań tej technologii na różnych powierzchniach, które wcześniej nie były dostępne dla tradycyjnych paneli fotowoltaicznych. Przez to, że ogniwa perowskitowe Saule Technologies są elastyczne i bardzo lekkie, mogą pokryć ściany, wszystkie lekkie konstrukcje, akcesoria dla transportu, czy też tkaniny.
Na państwa stronie internetowej czytamy między innymi o zastosowaniach modułów perowskitowych w dziedzinie Internet of Things – a ja od razu przekładam to na systemy produkcyjne, na maszyny w halach. W jaki sposób takie ogniwa będą wykorzystywane w fabrykach, w procesach produkcyjnych?
Zwróciliśmy uwagę na sektor IoT, gdzie perowskitowe ogniwa zmienią sposób zasilania tych urządzeń. Na co dzień nie zdajemy sobie sprawy, jak wiele wokół nas jest różnych czujników. Jak dużo procesów, także w fabrykach, jest zautomatyzowanych. To są setki tysiące różnych, często małych urządzeń, w których wymiana baterii jest problematyczna. Wiele z tych urządzeń jest instalowanych w miejscach, w których nie ma dostępu do dużej ilości energii słonecznej, a nasze ogniwa działają przy minimalnej ilości światła, także światła sztucznego, rozproszonego, na przykład światła z żarówki. Pierwsze korzyści, które widzimy, to oszczędność czasu na pracy związanej z wymianą baterii w setkach tysięcy czujników. Po drugie, dostrzegamy aspekt środowiskowy - zużyte baterie pozostawiają za sobą toksyczne odpady, które mają szkodliwy wpływ na środowisko. Można dzięki temu zapobiec wyrzucaniu ton baterii, ponieważ automatyczne zasilane sensory działałyby bez zarzutu przez wiele lat.
Czy wręcz można wykluczyć używanie akumulatorów i baterii?
To zależy od tego, jak i w jakich warunkach działa dane urządzenie. Jeśli mamy stałe oświetlenie, takie urządzenia nie wymagałyby baterii. Może je zastąpić mały kondensator lub inne rozwiązanie, które gromadzi energię wtedy, kiedy urządzenie nie jest wykorzystywane, po to żeby potem ją wykorzystać, na przykład do transferu danych. Jest również wiele rodzajów prostych czujników, które połączone z ogniwami na bazie perowskitów, mogą pobierać prąd na bieżąco, bez potrzeby magazynowania energii. Właśnie to zwraca uwagę projektantów - że oferujemy de facto nowe, stałe źródło zasilania.
Rozpoczynają państwo proces produkcyjny poza laboratorium - z fazy rozwojowej przechodzicie do masowego wytwarzania. Jakie były wyzwania na drodze do fazy przemysłowej?
Od początku rozwoju technologii w laboratorium myśleliśmy o o masowej produkcji, o skalowalności procesu. Docelowo użyliśmy tych samych głowic drukujących, tych samych tuszy, tych samych procesów, co w laboratorium. Największym wyzwaniem przy wdrażaniu tej technologii było to, że nie istniały inne linie produkcyjne, na których moglibyśmy się wzorować. Tak naprawdę musieliśmy całą linię przemyśleć i zaprojektować od zera, a następnie zlecić podwykonawcom budowę maszyn zgodnie z naszym projektem.Trwało to dłużej niż postawienie produkcji według istniejącego już rozwiązania i na pewno było droższe. Niemniej jestem bardzo zadowolona z efektu, a kolejne linie będą stawiane w dużo krótszym czasie. Potencjał, który drzemie w tej technologii oraz parametry ogniw już teraz są wystarczające do pierwszych komercyjnych instalacji. Nasza technologia jest jednak wciąż rozwijana - poprawiamy wydajność i stabilność ogniw oraz optymalizujemy proces.
Ile trwał cały proces budowania linii i uruchamiania produkcji?
Proces ten składał się z kilku etapów. Patrząc na całość, od momentu, kiedy wróciłam z Hiszpanii do Polski i wraz z Piotrem Krychem i Arturem Kupczunasem założyliśmy firmę, do momentu kiedy z linii produkcyjnej wyszedł pierwszy moduł fotowoltaiczny, minęło sześć lat. W tym czasie, około roku trwała sama budowa budynku, a trzy lata projektowanie i dostarczenie gotowych urządzeń. Nasi inżynierowie projektu jeszcze przed etapem projektowania odwiedzali fabryki w różnych miejscach świata i testowali, jakie rozwiązania będą odpowiednie dla produkcji w fabryce Saule Technologies.
Tematem przewodnim naszego portalu jest Lean Management, czyli koncepcja zarządzania produkcją i przedsiębiorstwem o japońskich korzeniach. Jednym z pierwszych dużych inwestorów Saule Technologies był właśnie inwestor z Japonii, stąd moje końcowe pytanie. Czy korzystają Państwo z metody Lean i czy wraz z inwestorem przyszły jakieś sugerowane metody zarządzania?
Nie, nie narzucono nam z góry określonego postępowania. Nasz japoński inwestor jest inwestorem biernym. Zainwestował, mając dużą wiarę w nas i w tworzoną przez nas technologię. Oczywiście, regularnie dostarczamy naszemu inwestorowi raporty. Jest on zadowolony z postępów, w związku z czym nie ingeruje w sposoby prowadzenia firmy, czy prowadzenia badań – ponieważ to, co obiecaliśmy, że zostanie wykonane, wykonaliśmy. Założenia metody Lean są jednak bardzo intuicyjne i na pewno, jak każde przedsiębiorstwo wykorzystujemy elementy koncepcji, metryk i narzędzi Lean.
![]() Dr. Olga Malinkiewicz jest współzałożycielką i CTO - Chief Technology Officer w Saule Technologies. Ukończyła Politechnikę Katalonii w 2010 roku (mgr Fotoniki). W 2017 roku obroniła doktorat w Instytucie Nauk Molekularnych Uniwersytetu w Walencji pod kierownictwem dr. Henka Bolinka, z tezą na temat tanich, wydajnych hybrydowych ogniw słonecznych. Olga opracowała nowatorską architekturę ogniw perowskitowych, umożliwiającą wytwarzanie wydajnych ogniw perowskitowych. |
Pozostałe technologie wspierające Lean
-
Nietypowy proces logistyczny - jak sobie z nim poradzić bez umiejętności programistycznych?
Nietypowe procesy logistyczne od dawna stanowią wyzwanie dla przedsiębiorstw, których model biznesowy polega na wykonywaniu krótkich serii produktów na zamówienie. Do tej pory w większości przedsiębiorstw konieczne było ręczne obsługiwanie każdego etapu procesu.
-
Comarch: Intralogistyka 4.0 w praktyce, czyli poprawa wydajności zakładu produkcyjnego dzięki automatycznej lokalizacji i identyfikacji zasobów
Postęp czwartej rewolucji przemysłowej sprawia, że wprowadzanie rozwiązań IoT, które opierają się na zbieraniu danych i przetwarzaniu ich w czasie rzeczywistym, staje się koniecznością. Wiąże się to z analizą informacji dostarczanych przez systemy oparte na najnowszych technologiach.
-
Jak usprawnić intralogistykę w firmie w oparciu o lokalizację zasobów?
Wyzwania, jakie stawia przed nami czwarta rewolucja przemysłowa, skłaniają przedsiębiorców do poszukiwania rozwiązań, które znacznie uproszczą i zautomatyzują procesy produkcyjne i logistyczne.
Komentarze
W dniach 14-16 maja 2025 roku w Centrum Edukacyjno-Kongresowym Politechniki Śląskiej odbędzie się Ogólnopolski Kongres Jakościowy 2025. To największe wydarzenie w Polsce poświęcone jakości, łączące wiedzę, relacje i biznes. Kongres stanowi unikalną o ...
Dziewiąta edycja Europejskiego Kongresu Lean przyniosła uczestnikom ogromną dawkę wiedzy na temat wdrażania efektywnych procesów i innowacji w różnych branżach. Organizatorzy podkreślali, że kluczowym przesłaniem wydarzenia jest przekonanie, że to, c ...