Projekty Lean
Zatrzymanie linii, to odpowiedzialność przełożonego - wywiad Mikiharu Aoki
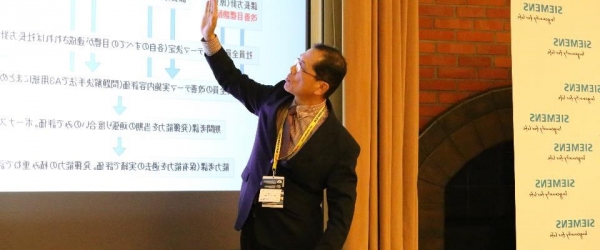
System Produkcyjny Toyoty, to źródło z którego wypływa wiedza na temat unikalnego sposobu zarządzania przedsiębiorstwem, w świecie określanego jako Lean Management. W krótkim wywiadzie z Mikiharu Aoki, wieloletnim pracownikiem Toyoty, dowiadujemy się, co dzieje się, gdy na różne polach od tego źródła odchodzimy.
Krzysztof Bednarz: Myśląc o Toyota Production System, widzimy pewien poukładany system, zestaw narzędzi i nieustanne rozwiązywanie problemów. Pan w swoich wypowiedziach wskazuje na jeszcze jeden ważny czynnik – nieustanną ocenę. Na co szczególnie zwrócić uwagę w tym aspekcie?
Mikiharu Aoki: To jest tak, że owa ocena ma się przekładać na działania prowadzące głównie do obniżenia kosztów. Ma pokazywać miejsca niezgodne ze standardami - w różnym znaczeniu tego słowa - i to ma się przekładać na działania, które zmniejszają koszty przedsiębiorstwa. Dla mnie takim kluczem motywacji w wypełnianiu tego zadania, jest poczucie udziału w zarządzaniu firmą. Pracując w Toyocie jako menadżer czułem, że w ten sposób uczestniczę realnie w zarządzaniu firmą, realizując cele, wspomagając niejako w tym mojego prezesa.
KB: Podróżuje Pan po świecie, wizytując wiele zakładów o różnym poziomie rozwoju organizacyjnego. Jakie błędy najczęściej pojawiają się we wdrożeniach Lean?
MA: Odpowiadając, odwrócę nieco pytanie. Mam takie poczucie, że jeśli ktoś prosi mnie, żebym przyjechał do jego zakładu, to jest to osoba bardzo zaangażowana i bardzo jej się chce. Ja często powtarzam, że System Produkcyjny Toyoty, to nie jest coś bardzo skomplikowanego, to są naprawdę bardzo proste rzeczy i nawet jeśli ktoś robi to po omacku i nie każda decyzja jest właściwa, to nawet wtedy nie mogę powiedzieć, że błądzi. I w tym sensie nie widzę żadnych problemów w tych zakładach, bo widzę że wszystkim tam bardzo się chce.
KB: Niektóre przedsiębiorstwa ulegają tendencji do nadbudowywania zasad wywodzących się z systemu TPS. Przykładowo definiują osiem lub nawet dziewięć marnotrawstw, 6S zamiast 5S. Co Pan myśli o takim rozszerzaniu metod TPS?
MA: Ja nie mam z tym problemu. Prawdę mówiąc, w ogóle mi to nie przeszkadza. Jeżeli tylko dany zakład uchwycił, co jest rdzeniem. Ja przepraszam, że to mówię, ale miałem takie szczęście, że los mnie poprowadził ku pracy w Toyocie, więc uważam, że ja ten rdzeń rozumiem. Jeżeli jakieś firmy rozumieją ów rdzeń, to wszelkie dodawanie elementów, czy rozwijanie tych zasad, nie jest żadną przeszkodą.
Wiem jednak, że są na przykład konsultanci wywodzący się z fabryk produkujących karoserie samochodowe, którzy nauczając systemu produkcyjnego Toyoty, skupiają się tylko i wyłącznie na tej pierwszej warstwie - narzędziowej. Z mojego punktu widzenia, to co staram się podkreślać, bardzo ważne są te dwa pozostałe elementy, czyli zarządzanie kosztami i rozwiązywanie problemów. Bo tak naprawdę, dopiero gdy te trzy elementy są połączone, wtedy ten system funkcjonuje w całości – i przynosi takie rezultaty jak przez lata w Toyocie.
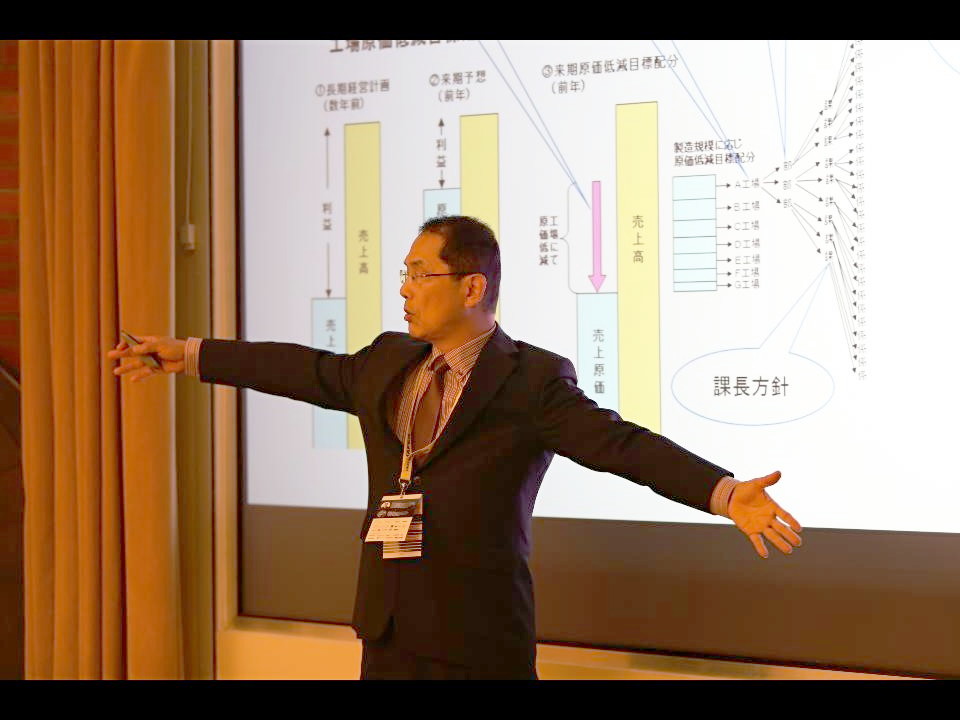
KB: Zasada, która mówi, że żadna wadliwa część nie powinna opuścić stanowiska pracy jest jedną z najważniejszych w TPS. Jednak, gdy rozmawiamy z pracownikami z polskich firm, słyszymy że pracownicy obawiają się zatrzymywać produkcję. Czy również Pan ma takie doświadczenia. Jak temu zapobiegać? Jak budować kulturę wpuszczania zera wad w kolejne etapy procesu?
MA: Sądzę, że jest to kwestia osób nadzorujących, przełożonych i kwestia polityki firmy. To dla mnie oczywiste, że gdy linia w przypadku wystąpienia nieprawidłowości nie jest zatrzymana, to jest duże niebezpieczeństwo, że defekt jakościowy wyjdzie z linii. Jest to kwestia przyjęcia zasady i przekonania pracowników, że jest to niezbędne. Powiedzenia im, że absolutnie nie będą karani za coś za zatrzymanie procesu, a wprost przeciwnie. Kwestia odpowiedzialności nie leży tutaj po stronie operatorów, ale raczej przełożonych.
W Toyocie jest tak, że pracujemy w takcie i ten obszar, za który odpowiada operator jest podzielony np. na 20-sekundowe odcinki. W większości jest to zresztą pracownik tymczasowy, a nie stały. W momencie, gdy pracownik przeczuwa, że coś jest nie tak, ma obowiązek użyć dostępnych przycisków. Włącza się żółte światło - żółty andon. Do odcinka przybiega bezpośredni przełożony, czyli mistrz odpowiedzialny za tę strefę i to on tak naprawdę decyduje. On pomaga pracownikowi, stara się tę sytuację rozwiązać i ostatecznie jest tą osobą, która decyduje o zatrzymaniu linii.
KB: Chciałbym zadać pytanie, które zadaję wszystkim, którzy odwiedzają Polskę, a mają globalne doświadczenie z Lean Management. Są na terenie naszego kraju firmy, które rozpoczęły działania z Lean, np 5S, bądź TPM, ale po pewnym czasie wszystko legło w gruzach, wyniki spadły. Jednak chciałyby zacząć na nowo. Jaką radę możemy dać tym firmom?
MA: Moja rada jest taka, żeby po mnie zadzwonili. A mówiąc poważnie... nie muszę to być koniecznie ja, ale myślę że konieczna jest tu pomoc osoby, która wie po prostu jaki jest fundament ciągłego doskonalenia i pomoże przeprowadzić taką firmę przez kolejne kroki na tej ścieżce.

Mikiharu Aoki (ur. w 1955 r.) - pracował w Toyocie przez 26 lat, przechodząc przez jej wszystkie szczeble organizacyjne. Zarządzał m.in. fabrykami w Japonii i USA. Autor książek wyjaśniających pracę w Systemie Produkcyjnym Toyoty, w tym książki wydanej na polskim rynku: "Jak działa fabryka Toyoty".
Mikiharu Aoki: To jest tak, że owa ocena ma się przekładać na działania prowadzące głównie do obniżenia kosztów. Ma pokazywać miejsca niezgodne ze standardami - w różnym znaczeniu tego słowa - i to ma się przekładać na działania, które zmniejszają koszty przedsiębiorstwa. Dla mnie takim kluczem motywacji w wypełnianiu tego zadania, jest poczucie udziału w zarządzaniu firmą. Pracując w Toyocie jako menadżer czułem, że w ten sposób uczestniczę realnie w zarządzaniu firmą, realizując cele, wspomagając niejako w tym mojego prezesa.
KB: Podróżuje Pan po świecie, wizytując wiele zakładów o różnym poziomie rozwoju organizacyjnego. Jakie błędy najczęściej pojawiają się we wdrożeniach Lean?
MA: Odpowiadając, odwrócę nieco pytanie. Mam takie poczucie, że jeśli ktoś prosi mnie, żebym przyjechał do jego zakładu, to jest to osoba bardzo zaangażowana i bardzo jej się chce. Ja często powtarzam, że System Produkcyjny Toyoty, to nie jest coś bardzo skomplikowanego, to są naprawdę bardzo proste rzeczy i nawet jeśli ktoś robi to po omacku i nie każda decyzja jest właściwa, to nawet wtedy nie mogę powiedzieć, że błądzi. I w tym sensie nie widzę żadnych problemów w tych zakładach, bo widzę że wszystkim tam bardzo się chce.
KB: Niektóre przedsiębiorstwa ulegają tendencji do nadbudowywania zasad wywodzących się z systemu TPS. Przykładowo definiują osiem lub nawet dziewięć marnotrawstw, 6S zamiast 5S. Co Pan myśli o takim rozszerzaniu metod TPS?
MA: Ja nie mam z tym problemu. Prawdę mówiąc, w ogóle mi to nie przeszkadza. Jeżeli tylko dany zakład uchwycił, co jest rdzeniem. Ja przepraszam, że to mówię, ale miałem takie szczęście, że los mnie poprowadził ku pracy w Toyocie, więc uważam, że ja ten rdzeń rozumiem. Jeżeli jakieś firmy rozumieją ów rdzeń, to wszelkie dodawanie elementów, czy rozwijanie tych zasad, nie jest żadną przeszkodą.
Wiem jednak, że są na przykład konsultanci wywodzący się z fabryk produkujących karoserie samochodowe, którzy nauczając systemu produkcyjnego Toyoty, skupiają się tylko i wyłącznie na tej pierwszej warstwie - narzędziowej. Z mojego punktu widzenia, to co staram się podkreślać, bardzo ważne są te dwa pozostałe elementy, czyli zarządzanie kosztami i rozwiązywanie problemów. Bo tak naprawdę, dopiero gdy te trzy elementy są połączone, wtedy ten system funkcjonuje w całości – i przynosi takie rezultaty jak przez lata w Toyocie.
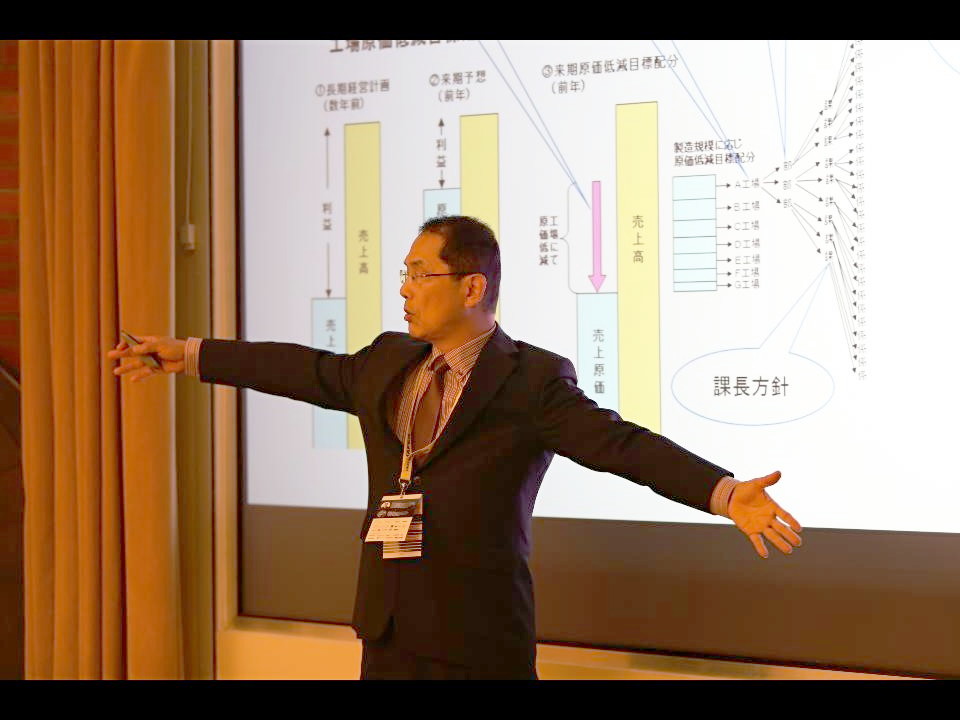
KB: Zasada, która mówi, że żadna wadliwa część nie powinna opuścić stanowiska pracy jest jedną z najważniejszych w TPS. Jednak, gdy rozmawiamy z pracownikami z polskich firm, słyszymy że pracownicy obawiają się zatrzymywać produkcję. Czy również Pan ma takie doświadczenia. Jak temu zapobiegać? Jak budować kulturę wpuszczania zera wad w kolejne etapy procesu?
MA: Sądzę, że jest to kwestia osób nadzorujących, przełożonych i kwestia polityki firmy. To dla mnie oczywiste, że gdy linia w przypadku wystąpienia nieprawidłowości nie jest zatrzymana, to jest duże niebezpieczeństwo, że defekt jakościowy wyjdzie z linii. Jest to kwestia przyjęcia zasady i przekonania pracowników, że jest to niezbędne. Powiedzenia im, że absolutnie nie będą karani za coś za zatrzymanie procesu, a wprost przeciwnie. Kwestia odpowiedzialności nie leży tutaj po stronie operatorów, ale raczej przełożonych.
W Toyocie jest tak, że pracujemy w takcie i ten obszar, za który odpowiada operator jest podzielony np. na 20-sekundowe odcinki. W większości jest to zresztą pracownik tymczasowy, a nie stały. W momencie, gdy pracownik przeczuwa, że coś jest nie tak, ma obowiązek użyć dostępnych przycisków. Włącza się żółte światło - żółty andon. Do odcinka przybiega bezpośredni przełożony, czyli mistrz odpowiedzialny za tę strefę i to on tak naprawdę decyduje. On pomaga pracownikowi, stara się tę sytuację rozwiązać i ostatecznie jest tą osobą, która decyduje o zatrzymaniu linii.
KB: Chciałbym zadać pytanie, które zadaję wszystkim, którzy odwiedzają Polskę, a mają globalne doświadczenie z Lean Management. Są na terenie naszego kraju firmy, które rozpoczęły działania z Lean, np 5S, bądź TPM, ale po pewnym czasie wszystko legło w gruzach, wyniki spadły. Jednak chciałyby zacząć na nowo. Jaką radę możemy dać tym firmom?
MA: Moja rada jest taka, żeby po mnie zadzwonili. A mówiąc poważnie... nie muszę to być koniecznie ja, ale myślę że konieczna jest tu pomoc osoby, która wie po prostu jaki jest fundament ciągłego doskonalenia i pomoże przeprowadzić taką firmę przez kolejne kroki na tej ścieżce.

Mikiharu Aoki (ur. w 1955 r.) - pracował w Toyocie przez 26 lat, przechodząc przez jej wszystkie szczeble organizacyjne. Zarządzał m.in. fabrykami w Japonii i USA. Autor książek wyjaśniających pracę w Systemie Produkcyjnym Toyoty, w tym książki wydanej na polskim rynku: "Jak działa fabryka Toyoty".
Technologie wspierające Lean
PARTNERZY SEKCJI:
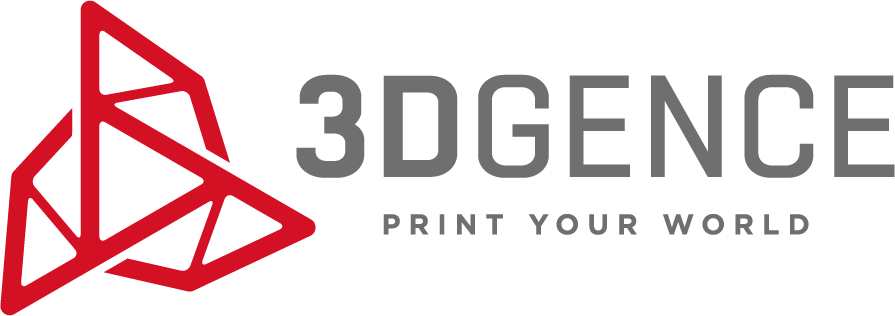
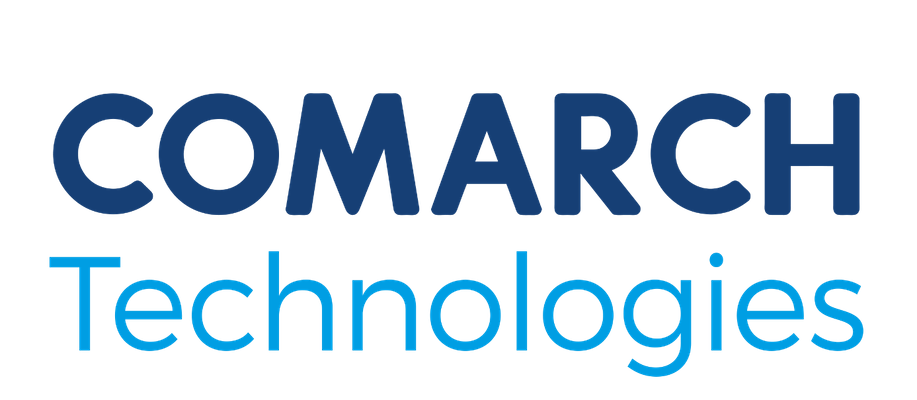
Śledź nas w social media
Aktualności
Ogólnopolski Kongres Jakościowy 2025: Wiedza. Relacje. Biznes.
Nowoczesne podejście do doskonalenia procesów - relacja z IX Europejskiego Kongresu Lean
PolecamyW dniach 14-16 maja 2025 roku w Centrum Edukacyjno-Kongresowym Politechniki Śląskiej odbędzie się Ogólnopolski Kongres Jakościowy 2025. To największe wydarzenie w Polsce poświęcone jakości, łączące wiedzę, relacje i biznes. Kongres stanowi unikalną o ...
Dziewiąta edycja Europejskiego Kongresu Lean przyniosła uczestnikom ogromną dawkę wiedzy na temat wdrażania efektywnych procesów i innowacji w różnych branżach. Organizatorzy podkreślali, że kluczowym przesłaniem wydarzenia jest przekonanie, że to, c ...
Kalendarz konferencji Lean
Najbliższe szkolenia Lean
Patronujemy Wyszukiwarka
Śledź nas na Facebooku