Projekty Lean
Gdzie jest najsłabsze ogniwo w łańcuchu dostaw?
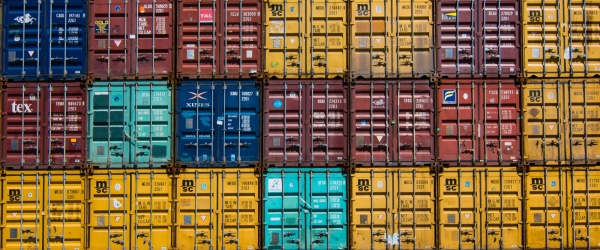
Bieżące, tragiczne skądinąd, wydarzenia wywołują wiele niepokoju i zawirowań w niemal wszystkich obszarach światowej produkcji przemysłowej. Wielu ekspertów w swoich komentarzach próbuje zwrócić naszą uwagę na słabość globalnych łańcuchów dostaw opartych na wytwórcach z Chin. Czy rzeczywiście to jest najsłabszy punkt? A może szczupłe zarządzanie i cała metodologia Lean z naczelnym JIT zawiodła? Zapraszam do zapoznania się z moją opinią i analizą przypadku.
Dla potrzeb przeprowadzenia analizy zacznijmy od zbudowania uproszczonego modelu produkcyjnego, w którym wytwarzamy tylko jeden produkt z wykorzystaniem dwóch komponentów.

Rys.1. Schemat modelu produkcyjnego.
Przyjmijmy przy tym, że dzienna produkcja to 1000 szt., a oba komponenty zużywane są w takim samym stosunku 1:1. Przy czym w komponent "A" zaopatruje nas dostawca z Chin, a komponent "B" można traktować, jako pochodzący ze źródła lokalnego (kraj europejski). Oczywiście pochodzenia danego komponentu w znaczący sposób wpływa na ustalenie parametrów planistycznych dla każdego z nich.
Zabezpieczenie zapasów powiązane z Chińskim Nowym Rokiem
Dla komponentu "A" przyjmujemy, że domyślnym sposobem transportu są dostawy morskie, ale oczywiście mamy świadomość istniejących, choć droższych, możliwości lądowych i powietrznych. Biorąc pod uwagę możliwe tego implikacje (kilkudniowe spóźnienie statku nie jest niczym niezwykłym, opóźnienia wyładunku kontenerów powodowane warunkami atmosferycznymi są wręcz częste, a przecież jeszcze przy polskich portach mamy działające oddziały WIOR) ustalamy zapas bezpieczeństwa na poziomie 14 dni produkcyjnych. Natomiast zakładana częstotliwość dostaw to raz w tygodniu.

Tab.1. Parametry planistyczne i ilościowa analiza zapasu w łańcuchu dostaw dla komponentu "A".
Dla komponentu "B", z uwagi na jego lokalność, możemy pozwolić sobie na utrzymywanie dużo niższego zapasu bezpieczeństwa. Praktyka wskazuje, że w takich sytuacjach dominuje zakres od 3 do 5 dni, przyjmijmy wersję najbezpieczniejszą niż górną granicę tego zakresu. Jednocześnie jako domyślny rodzaj transportu przyjmujemy lądowy z częstotliwością raz na tydzień.

Tab.2. Parametry planistyczne i ilościowa analiza zapasu w łańcuchu dostaw dla komponentu "B".
Wybuch epidemii koronawirusa, najpierw w Chinach a później w pozostałych obszarach, możemy uznać za bardzo wymagający stres test dla naszego łańcucha dostaw. Znając dotychczasowy przebieg wydarzeń możemy spróbować odpowiedzieć na pytanie, która z jego części jest bardziej narażona na zakłócenia. Wszystko rozpoczęło się w Chinach więc tam też zacznijmy.
Do ok. 22 stycznia chińskie fabryki pracowały na 100% swoich możliwości, przygotowując ostatnie partie przed planowanym wyłączeniem związanym z Chińskim Nowym Rokiem (24.01-02.02). W tym okresie zaczęto tam odnotowywać tam coraz więcej przypadków zachorowań w związku z czym Chińczycy nie wrócili do pracy na początku lutego. Trzeba przyznać, że z punktu widzenia łańcucha dostaw rozwój epidemii pokrywający się z tygodniowym świętowaniem w dużym stopniu niwelował negatywny wpływ na odbiorców. Przerwa bowiem i tak była planowana, wysyłki realizowane w trybie wyprzedzającym, zapasy bezpieczeństwa po obu stronach gotowe. W wyniku decyzji chińskiego rządu wszystkie zakładu produkcyjne pozostały zamknięte do 9 lutego, kiedy to rozpoczęto proces audytów oceniających przygotowanie poszczególnych fabryk w zakresie środków ochrony osobistej i ogólnego przygotowania do wznowienia produkcji w otoczeniu zagrożenia epidemiologicznego. Przymusowa przerwa dla niemal całego chińskiego przemysłu potrwała min. 8 dni. Przy czym w większości przypadków było to miedzy 8 a 21. W moim przypadku, dostawców zlokalizowanych w prowincjach Dongguan, Hangzhou czy Shenyang, postoje trwały maksymalnie 18 dni.
Czy zabrakło komponentów z Chin?
Porównajmy parametry przyjęte na wstępie z rzeczywistymi wydarzeniami. Zakładaliśmy, że utrzymujemy zapas bezpieczeństwa po swojej stronie na poziomie 14 dni produkcyjnych, jak i dostawca utrzymuje gotowy do wysyłki w każdej chwili zapas po swojej stronie odpowiadający kolejnym siedmiu dniom. Mamy więc sumarycznie 3 tygodnie zapasu bezpieczeństwa i 6 tygodni w transporcie. Co to tak właściwie oznacza? Jeśli zakładamy powstanie „wyrwy” w dostawach po 2 lutego, ale z drugiej strony mamy zabezpieczone 9 tygodni, to kiedy powinniśmy odczuć brak dostaw? Z prostej kalkulacji wynika, że między 30.03 a 05.04. Czy rzeczywiście dopiero wtedy pojawił się problem w Europie i komentarze wskazujące chińskich dostawców jako winnych zaburzenia światowego łańcucha dostaw? Proszę zwrócić uwagę, że nie silę się nawet na analizę możliwości jakie stwarzają alternatywne środki transportu. Oczywiste jest, że ośmio-, czy nawet dwudziestodniowa przerwa nie była w stanie tak mocno zachwiać poprawnie zaprojektowanym procesem zaopatrzenia. (Mam świadomość, że istnieją fabryki zlokalizowane w centrum ogniska epidemii, w samym mieście Wuhan, które do aktywności wracały dopiero w połowie marca i w takiej sytuacji rzeczywiście utrzymanie łańcucha dostaw wymagało dodatkowych aktywności i środków związanych z wykorzystaniem niestandardowych środków transportu. Jednak nawet w takich okolicznościach pozostawał zapas czasu na wdrożenie takich rozwiązań.)
Zamrożenie produkcji nie przez brak zapasów...
Spójrzmy teraz na drugą stronę, jak przebiegała sytuacja w Europie w ostatnim miesiącu.
Od połowy marca napływają informacje od kolejnych europejskich producentów o wygaszaniu produkcji. Jak już wiemy, nie mogło to jeszcze wtedy wynikać z braku komponentów wywołanego przez zerwane azjatyckie łańcuchy dostaw. Od 23 marca w wyniku rządowych restrykcji ograniczona zostaje wszelka produkcja przemysłowa m.in. we Francji i Włoszech. 30 marca dołącza m.in. Hiszpania (zakazy te w większości nadal obowiązują). Sprawdźmy zatem jaki wpływ, w kontekście założeń naszego modelu, wywołują wyłączenia w europejskich fabrykach. Przyjęliśmy (bardzo optymistyczne w mojej ocenie) założenie, że całkowity dostępny zapas w lokalnym łańcuchu dostaw pokrywa 12 dniowe zapotrzebowanie. Przyjmując za graniczną datę wyłączenia dostawcy 22 marzec, musimy zgodzić się z wnioskiem, że łańcuch zaopatrzenia zostanie zerwany nie później niż 4 kwietnia. Warto zauważyć, że nie mamy w tym przypadku żadnego pola manewru, nie pomogą inne środki transportu czy dodatkowe zaangażowanie.
Podwójny łańcuch dostaw rozwiązaniem?
Jedynym rozwiązaniem, które rzeczywiście jest w stanie zabezpieczyć dopływ specyficznych komponentów jest dywersyfikacja poprzez double sourcing, co myślę że bardziej lokalnie moglibyśmy określać jako podwójny łańcuch dostaw. Należy przy tym mieć na uwadze, aby zakłady dostawców zlokalizowane były w różnych rejonach geograficznych a najlepiej, aby dla każdego z nich istniały różne środki transportu. Ujmując to bardziej obrazowo: dla każdego specyficznego komponentu warto zakontraktować jednego dostawcę lokalnego (ze względu na położenie Polski może być to właściwie dowolny kraj europejski), który na co dzień zapewni nam większą elastyczność i szybkość dostaw oraz drugiego dostawcę np. w krajach Azji (oprócz oczywistych zalet związanych z potencjałem wytwórczym, istotna jest również możliwość organizacji transportów drogą lądową – koleją lub nawet drogowo, co zostało wprowadzone do oferty np. CEVA Logistic). W ten sposób oprócz oczywistego balansu między rachunkiem kosztów a elastycznością i możliwościami dostawców w utworzonym łańcuchu dostaw, zapewniamy sobie jego trwałość nawet w przypadku nagłej destabilizacji jednego z regionów, jak np. wybuch epidemii.
A co ze szczupłymi zapasami?
Jednocześnie, nie uważam aby był to wystarczająco dobry powód do porzucenia idei szczupłego zarządzania, ograniczania wartości zapasu, poprawiania cash flow. Należy mieć świadomość, że rozwiązania które świetnie sprawdzają w codziennej praktyce operacyjnej mogą zawodzić w sytuacja ekstremalnych, bo nie do tego zostały stworzone. Sytuacje ekstremalne zawsze mogą wymagać ekstremalnych, kosztownych, dodatkowych działań. Jednakże to dzięki wykorzystaniu technik i narzędzi lean management w codziennej praktyce, jesteśmy w stanie uzyskiwać profity na tyle znaczne, by w sytuacji wyjątkowej móc pozwolić sobie na zapłacenie wyższego rachunku.
Wracając do tytułowego pytania. Najsłabszym ogniwem łańcucha dostaw okazuje się być jego projektant, skupiony tylko na jednym aspekcie, niezależnie czy jest to czynnik kosztowy, wskaźnik elastyczności, lead time, lokalny patriotyzm czy jeszcze coś innego. Tym samym mniej lub bardziej świadomie pominął w swojej analizie pozostałe z nich wraz z implikacjami które wnoszą do całego procesu.

Rys.1. Schemat modelu produkcyjnego.
Przyjmijmy przy tym, że dzienna produkcja to 1000 szt., a oba komponenty zużywane są w takim samym stosunku 1:1. Przy czym w komponent "A" zaopatruje nas dostawca z Chin, a komponent "B" można traktować, jako pochodzący ze źródła lokalnego (kraj europejski). Oczywiście pochodzenia danego komponentu w znaczący sposób wpływa na ustalenie parametrów planistycznych dla każdego z nich.
Zabezpieczenie zapasów powiązane z Chińskim Nowym Rokiem
Dla komponentu "A" przyjmujemy, że domyślnym sposobem transportu są dostawy morskie, ale oczywiście mamy świadomość istniejących, choć droższych, możliwości lądowych i powietrznych. Biorąc pod uwagę możliwe tego implikacje (kilkudniowe spóźnienie statku nie jest niczym niezwykłym, opóźnienia wyładunku kontenerów powodowane warunkami atmosferycznymi są wręcz częste, a przecież jeszcze przy polskich portach mamy działające oddziały WIOR) ustalamy zapas bezpieczeństwa na poziomie 14 dni produkcyjnych. Natomiast zakładana częstotliwość dostaw to raz w tygodniu.

Tab.1. Parametry planistyczne i ilościowa analiza zapasu w łańcuchu dostaw dla komponentu "A".
Dla komponentu "B", z uwagi na jego lokalność, możemy pozwolić sobie na utrzymywanie dużo niższego zapasu bezpieczeństwa. Praktyka wskazuje, że w takich sytuacjach dominuje zakres od 3 do 5 dni, przyjmijmy wersję najbezpieczniejszą niż górną granicę tego zakresu. Jednocześnie jako domyślny rodzaj transportu przyjmujemy lądowy z częstotliwością raz na tydzień.

Tab.2. Parametry planistyczne i ilościowa analiza zapasu w łańcuchu dostaw dla komponentu "B".
Wybuch epidemii koronawirusa, najpierw w Chinach a później w pozostałych obszarach, możemy uznać za bardzo wymagający stres test dla naszego łańcucha dostaw. Znając dotychczasowy przebieg wydarzeń możemy spróbować odpowiedzieć na pytanie, która z jego części jest bardziej narażona na zakłócenia. Wszystko rozpoczęło się w Chinach więc tam też zacznijmy.
Do ok. 22 stycznia chińskie fabryki pracowały na 100% swoich możliwości, przygotowując ostatnie partie przed planowanym wyłączeniem związanym z Chińskim Nowym Rokiem (24.01-02.02). W tym okresie zaczęto tam odnotowywać tam coraz więcej przypadków zachorowań w związku z czym Chińczycy nie wrócili do pracy na początku lutego. Trzeba przyznać, że z punktu widzenia łańcucha dostaw rozwój epidemii pokrywający się z tygodniowym świętowaniem w dużym stopniu niwelował negatywny wpływ na odbiorców. Przerwa bowiem i tak była planowana, wysyłki realizowane w trybie wyprzedzającym, zapasy bezpieczeństwa po obu stronach gotowe. W wyniku decyzji chińskiego rządu wszystkie zakładu produkcyjne pozostały zamknięte do 9 lutego, kiedy to rozpoczęto proces audytów oceniających przygotowanie poszczególnych fabryk w zakresie środków ochrony osobistej i ogólnego przygotowania do wznowienia produkcji w otoczeniu zagrożenia epidemiologicznego. Przymusowa przerwa dla niemal całego chińskiego przemysłu potrwała min. 8 dni. Przy czym w większości przypadków było to miedzy 8 a 21. W moim przypadku, dostawców zlokalizowanych w prowincjach Dongguan, Hangzhou czy Shenyang, postoje trwały maksymalnie 18 dni.
Czy zabrakło komponentów z Chin?
Porównajmy parametry przyjęte na wstępie z rzeczywistymi wydarzeniami. Zakładaliśmy, że utrzymujemy zapas bezpieczeństwa po swojej stronie na poziomie 14 dni produkcyjnych, jak i dostawca utrzymuje gotowy do wysyłki w każdej chwili zapas po swojej stronie odpowiadający kolejnym siedmiu dniom. Mamy więc sumarycznie 3 tygodnie zapasu bezpieczeństwa i 6 tygodni w transporcie. Co to tak właściwie oznacza? Jeśli zakładamy powstanie „wyrwy” w dostawach po 2 lutego, ale z drugiej strony mamy zabezpieczone 9 tygodni, to kiedy powinniśmy odczuć brak dostaw? Z prostej kalkulacji wynika, że między 30.03 a 05.04. Czy rzeczywiście dopiero wtedy pojawił się problem w Europie i komentarze wskazujące chińskich dostawców jako winnych zaburzenia światowego łańcucha dostaw? Proszę zwrócić uwagę, że nie silę się nawet na analizę możliwości jakie stwarzają alternatywne środki transportu. Oczywiste jest, że ośmio-, czy nawet dwudziestodniowa przerwa nie była w stanie tak mocno zachwiać poprawnie zaprojektowanym procesem zaopatrzenia. (Mam świadomość, że istnieją fabryki zlokalizowane w centrum ogniska epidemii, w samym mieście Wuhan, które do aktywności wracały dopiero w połowie marca i w takiej sytuacji rzeczywiście utrzymanie łańcucha dostaw wymagało dodatkowych aktywności i środków związanych z wykorzystaniem niestandardowych środków transportu. Jednak nawet w takich okolicznościach pozostawał zapas czasu na wdrożenie takich rozwiązań.)
Zamrożenie produkcji nie przez brak zapasów...
Spójrzmy teraz na drugą stronę, jak przebiegała sytuacja w Europie w ostatnim miesiącu.
Od połowy marca napływają informacje od kolejnych europejskich producentów o wygaszaniu produkcji. Jak już wiemy, nie mogło to jeszcze wtedy wynikać z braku komponentów wywołanego przez zerwane azjatyckie łańcuchy dostaw. Od 23 marca w wyniku rządowych restrykcji ograniczona zostaje wszelka produkcja przemysłowa m.in. we Francji i Włoszech. 30 marca dołącza m.in. Hiszpania (zakazy te w większości nadal obowiązują). Sprawdźmy zatem jaki wpływ, w kontekście założeń naszego modelu, wywołują wyłączenia w europejskich fabrykach. Przyjęliśmy (bardzo optymistyczne w mojej ocenie) założenie, że całkowity dostępny zapas w lokalnym łańcuchu dostaw pokrywa 12 dniowe zapotrzebowanie. Przyjmując za graniczną datę wyłączenia dostawcy 22 marzec, musimy zgodzić się z wnioskiem, że łańcuch zaopatrzenia zostanie zerwany nie później niż 4 kwietnia. Warto zauważyć, że nie mamy w tym przypadku żadnego pola manewru, nie pomogą inne środki transportu czy dodatkowe zaangażowanie.
Podwójny łańcuch dostaw rozwiązaniem?
Jedynym rozwiązaniem, które rzeczywiście jest w stanie zabezpieczyć dopływ specyficznych komponentów jest dywersyfikacja poprzez double sourcing, co myślę że bardziej lokalnie moglibyśmy określać jako podwójny łańcuch dostaw. Należy przy tym mieć na uwadze, aby zakłady dostawców zlokalizowane były w różnych rejonach geograficznych a najlepiej, aby dla każdego z nich istniały różne środki transportu. Ujmując to bardziej obrazowo: dla każdego specyficznego komponentu warto zakontraktować jednego dostawcę lokalnego (ze względu na położenie Polski może być to właściwie dowolny kraj europejski), który na co dzień zapewni nam większą elastyczność i szybkość dostaw oraz drugiego dostawcę np. w krajach Azji (oprócz oczywistych zalet związanych z potencjałem wytwórczym, istotna jest również możliwość organizacji transportów drogą lądową – koleją lub nawet drogowo, co zostało wprowadzone do oferty np. CEVA Logistic). W ten sposób oprócz oczywistego balansu między rachunkiem kosztów a elastycznością i możliwościami dostawców w utworzonym łańcuchu dostaw, zapewniamy sobie jego trwałość nawet w przypadku nagłej destabilizacji jednego z regionów, jak np. wybuch epidemii.
A co ze szczupłymi zapasami?
Jednocześnie, nie uważam aby był to wystarczająco dobry powód do porzucenia idei szczupłego zarządzania, ograniczania wartości zapasu, poprawiania cash flow. Należy mieć świadomość, że rozwiązania które świetnie sprawdzają w codziennej praktyce operacyjnej mogą zawodzić w sytuacja ekstremalnych, bo nie do tego zostały stworzone. Sytuacje ekstremalne zawsze mogą wymagać ekstremalnych, kosztownych, dodatkowych działań. Jednakże to dzięki wykorzystaniu technik i narzędzi lean management w codziennej praktyce, jesteśmy w stanie uzyskiwać profity na tyle znaczne, by w sytuacji wyjątkowej móc pozwolić sobie na zapłacenie wyższego rachunku.
Wracając do tytułowego pytania. Najsłabszym ogniwem łańcucha dostaw okazuje się być jego projektant, skupiony tylko na jednym aspekcie, niezależnie czy jest to czynnik kosztowy, wskaźnik elastyczności, lead time, lokalny patriotyzm czy jeszcze coś innego. Tym samym mniej lub bardziej świadomie pominął w swojej analizie pozostałe z nich wraz z implikacjami które wnoszą do całego procesu.
![]() Marcin Magda | Specjalista planowania produkcji i materiałów, obecnie w branży automotive, wcześniej FMCG. Zawodowo, od ponad 10 lat związany z logistyką i gospodarką magazynową. |
Technologie wspierające Lean
PARTNERZY SEKCJI:
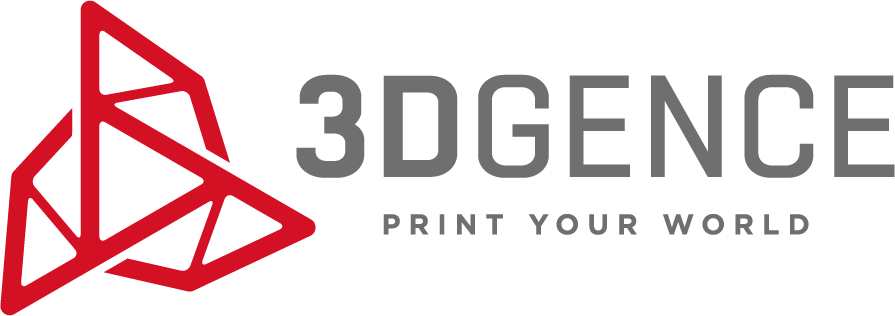
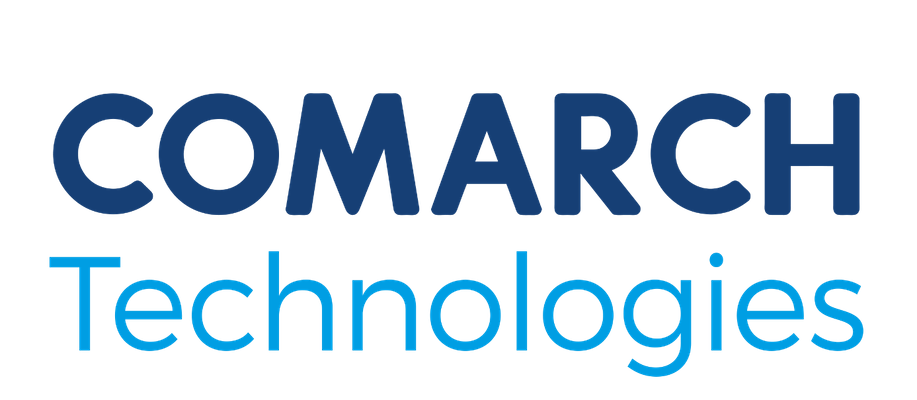
Śledź nas w social media
Aktualności
Ogólnopolski Kongres Jakościowy 2025: Wiedza. Relacje. Biznes.
Nowoczesne podejście do doskonalenia procesów - relacja z IX Europejskiego Kongresu Lean
PolecamyW dniach 14-16 maja 2025 roku w Centrum Edukacyjno-Kongresowym Politechniki Śląskiej odbędzie się Ogólnopolski Kongres Jakościowy 2025. To największe wydarzenie w Polsce poświęcone jakości, łączące wiedzę, relacje i biznes. Kongres stanowi unikalną o ...
Dziewiąta edycja Europejskiego Kongresu Lean przyniosła uczestnikom ogromną dawkę wiedzy na temat wdrażania efektywnych procesów i innowacji w różnych branżach. Organizatorzy podkreślali, że kluczowym przesłaniem wydarzenia jest przekonanie, że to, c ...
Kalendarz konferencji Lean
Najbliższe szkolenia Lean
Patronujemy Wyszukiwarka
Śledź nas na Facebooku