Projekty Lean
Mislabeling - poważny problem branży motoryzacyjnej
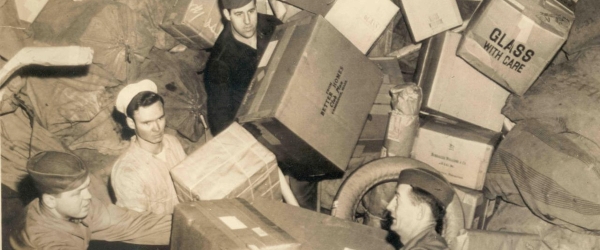
Źle oznaczony towar stał się poważnym problemem, z którym zmaga się cała branża motoryzacyjna. Dotychczas temat mislabelingu pojawiał się jedynie w branży spożywczej i farmaceutycznej. Bowiem błędnie oznaczony produkt, może mieć ogromny wpływ zarówno na zdrowie, jak i życie człowieka. W internecie istnieje sporo artykułów traktujących o żywności, lekach i o zawartości etykiet. Niestety w ślad za mislabelingiem w motoryzacji, na darmo szukać poradników, czy gotowych rozwiązań.
Co prawda w tym przypadku nie stwarza to bezpośredniego zagrożenia dla życia człowieka, niemniej jednak straty marketingowe i finansowe, jakie przynosi - są na tyle ogromne, że każde przedsiębiorstwo skupia się na jak najszybszej eliminacji tegoż problemu.
Ważnym aspektem mislabelingu jest przede wszystkim fakt, iż składa się na niego kilka kategorii błędów, które obrazuje poniższy schemat. W zależności od klienta, problem ze złym oznaczeniem wyrobu gotowego jest definiowany w zupełnie różny sposób. Mimo iż wszystkie są do siebie zbliżone, to jednak w każdym przypadku wpływają na inny proces u klienta.
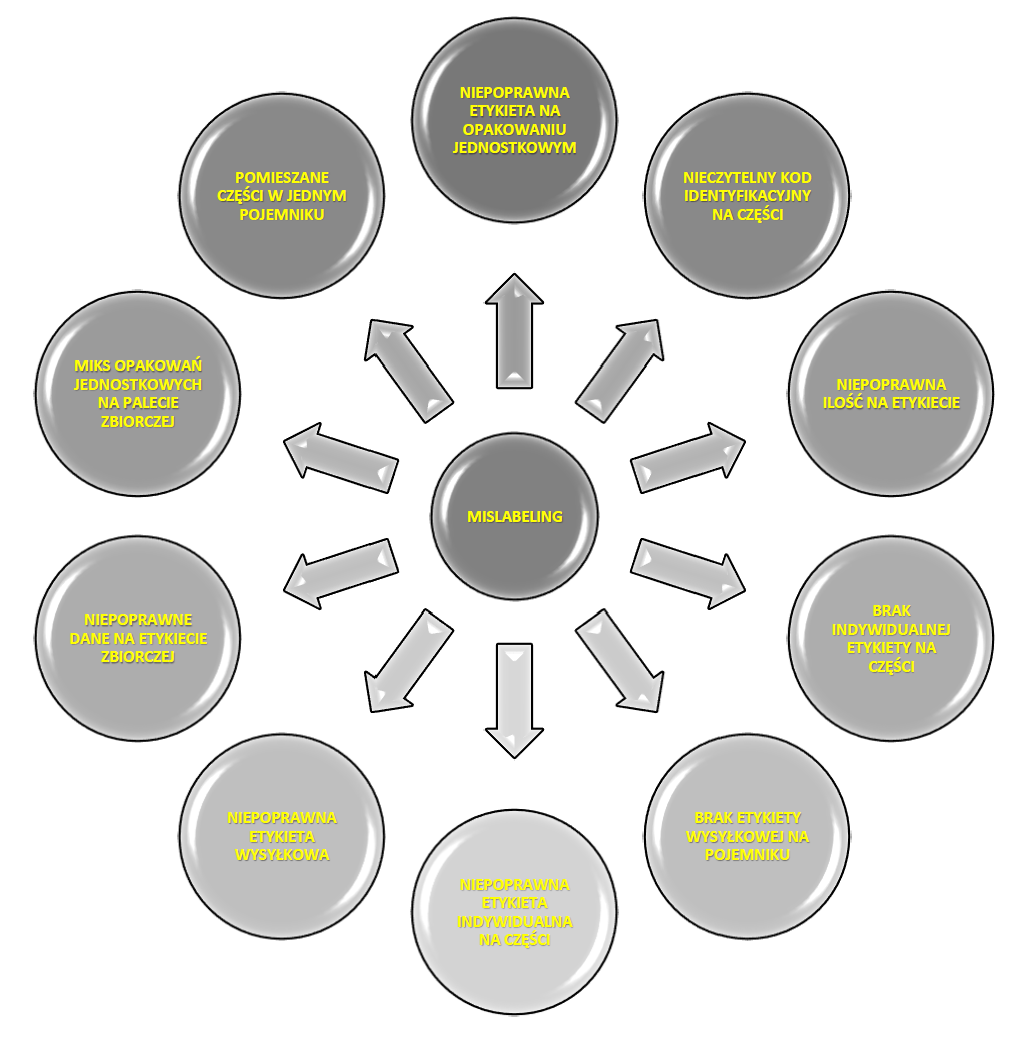
Rys. 1. Lista błędów zawartych w kategorii Mislabeling’u.
Klienci branży motoryzacyjnej, czyli innymi słowy znane marki samochodowe ponoszą z tytułu mislabelingu znacznie większe straty, niż mogłoby się wydawać. Niestety każdy błąd w oznaczeniu wyrobu, dostarczanego przez dostawcę, powoduje milionowe straty, na które duże marki nie mogą sobie pozwalać. Stąd też spora presja na dostawców, by przeciwdziałali tego typu incydentom.
Za podstawowy problem, który prowadzi do błędnego etykietowania, uznaje się bardzo często – człowieka. Firmy bowiem prześcigają się w coraz to nowych odkryciach, których zadaniem jest redukcja jego roli, albo nawet całkowita eliminacja człowieka w procesie etykietowania. Systemy te najczęściej zwane są ”Poka Yoke”, czyli w przełożeniu na język polski – odporne na błędy. Tymczasem wg jednego z twórców tego pojęcia – Shigeo Shingo – ”Poka Yoke to systemy odporne na błędy wynikające ze zmienności procesów, a nie na błędy, które może popełnić człowiek”.
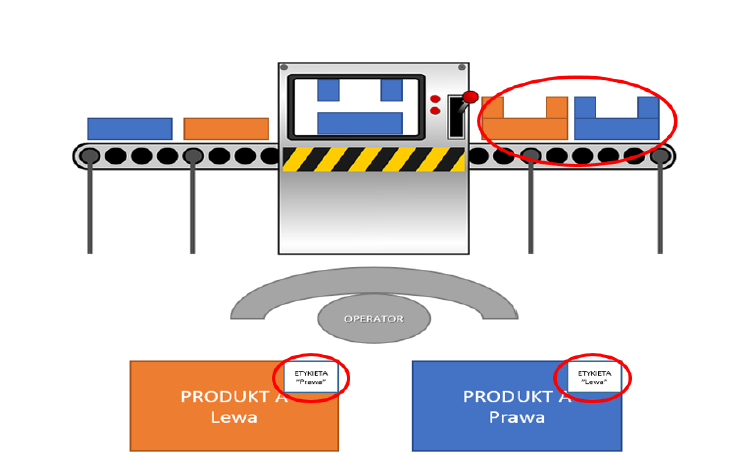
Rys. 2. Mislabeling na stanowiskach produkcyjnych powstaje w momencie, gdy operator np. oznaczając prawą stronę danej części, naklei na paletę - etykietę strony lewej lub gdy w paletę dedykowaną dla strony lewej umieści część prawą i w ten sposób pomiesza towar.
Kolejną najbardziej znaną, a zarazem najczęstszą przyczyną mislabelingu w firmach motoryzacyjnych są maszyny produkujące części, a także ich ustawienie. Dopiero na samym końcu ocenia się całościowy proces.
Właśnie dlatego też każde działania powinny być poprzedzone rzetelną analizą, która pomoże zdefiniować źródło problemu. W tym celu metody ”Problem Solving” zdają się być najlepszymi narzędziami do rozwiązania wszelkich problemów.
Każdą analizę wystąpienia mislabelingu rozpoczyna się od wyjaśnienia, na jakim obszarze problem pojawił się w pierwszej kolejności, ponieważ proces produkcji może odbywać się na kilku poziomach, w różnych miejscach. Stąd tak ważne jest odpowiednie wybranie metody do podjęcia dokładnej analizy.
Większość przedsiębiorstw na pierwszy ”rzut oka” wini zawsze człowieka - operatora produkcyjnego, logistycznego, czy też pracowników firm zewnętrznych, którzy przeprowadzają cząstkowe, bądź całościowe selekcje wyprodukowanego towaru. Często zdarza się jednak, że problemy pojawiają się z powodu błędnego procesu, nieodpornego na błędy ludzkie.
Właśnie dlatego ważne jest, aby przed rozpoczęciem zorganizować grupę, na którą składać się będą przedstawiciele różnych działów, na co dzień uczestniczących w rozpatrywanym procesie, np.: Logistyki, Jakości, Produkcji oraz CI (dział Ciągłego Doskonalenia). Następnie zgodnie z pierwszą zasadą Metody 5G, analizę powinno rozpocząć się na tzw. Gembie, czyli w miejscu, gdzie pojawił się dany problem (najczęściej są to obszary produkcyjne), na którym procesy bywają skomplikowane i różnorodne. Następnie za pomocą narzędzi takich jak: diagram Ishikawa, 5Why, czy 5W1H, warto rozpocząć cały proces analizy. Wtedy też powinno paść pierwsze pytanie: ”Czy mamy pewność, że problem pojawił się z powodu błędu ludzkiego”? Mimo, iż najczęściej jako źródło mislabelingu, postrzega się głównie człowieka, warto pamiętać, że tak naprawdę operatorzy są skarbnicą wiedzy. Nikt bowiem lepiej od nich - nie wie, co tak naprawdę sprawia, że problem pojawia się właśnie na ich stanowisku pracy. Dlatego dobry wywiad z operatorami na etapie analizy, może stanowić podstawę każdych kolejnych działań. Wówczas otrzymany obraz istniejącej sytuacji, pozwalających grupie specjalistów na zaplanowanie odpowiednich działań, które po wdrożeniu pozwolą na redukcję błędów, lub jej całkowitą eliminację, obniżając związane z tym straty.
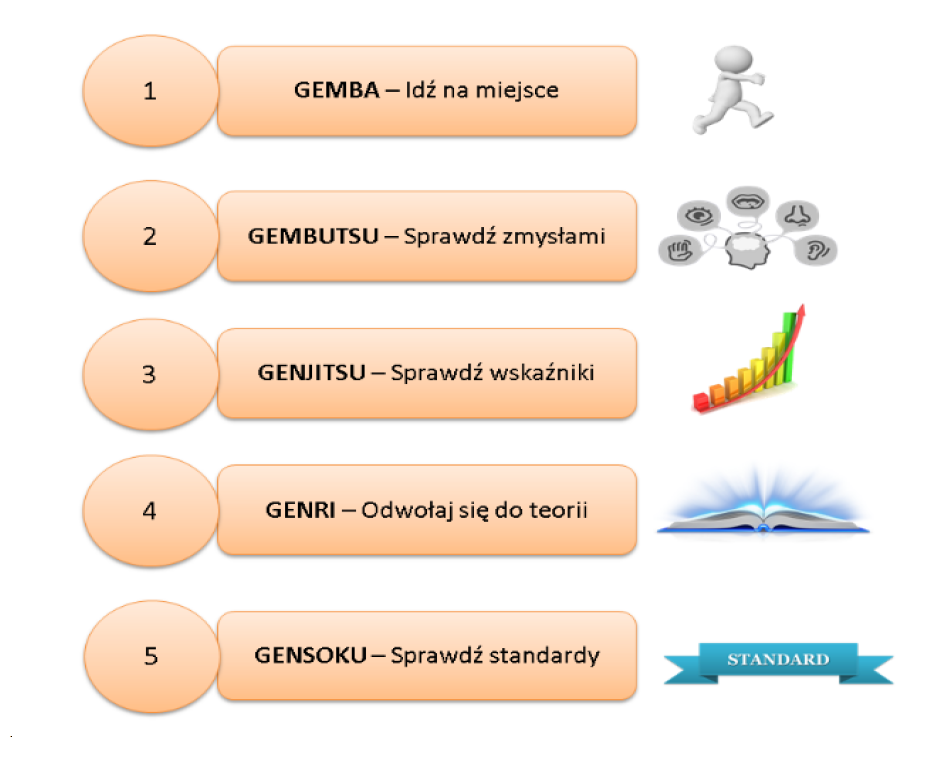
Rys. 3. Metoda 5G.
Redukcja, bądź całkowita eliminacja błędów w etykietowaniu wyrobu gotowego, pozwala nie tylko umocnić firmie swoją pozycję na rynku, czy też stać się rzetelnym dostawcą. Przede wszystkim pomaga w stworzeniu bazy rozwiązań, które z powodzeniem można implementować na nowe projekty, zwiększając tym samym swoją wydajność i tworząc przy tym odpowiednie warunki pracy ludziom, którzy swoją ciężką pracą przyczyniają się do zysków firmy.
Ważnym aspektem mislabelingu jest przede wszystkim fakt, iż składa się na niego kilka kategorii błędów, które obrazuje poniższy schemat. W zależności od klienta, problem ze złym oznaczeniem wyrobu gotowego jest definiowany w zupełnie różny sposób. Mimo iż wszystkie są do siebie zbliżone, to jednak w każdym przypadku wpływają na inny proces u klienta.
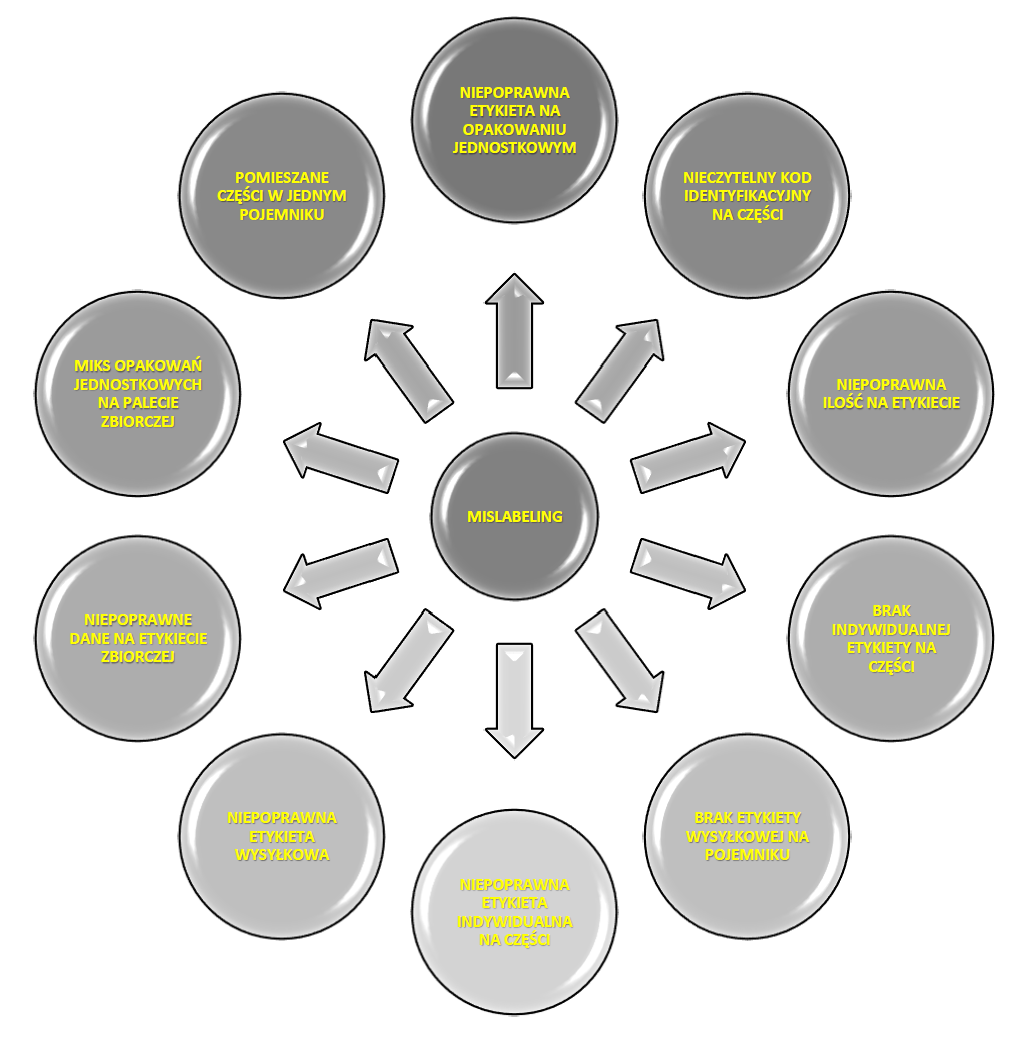
Rys. 1. Lista błędów zawartych w kategorii Mislabeling’u.
Klienci branży motoryzacyjnej, czyli innymi słowy znane marki samochodowe ponoszą z tytułu mislabelingu znacznie większe straty, niż mogłoby się wydawać. Niestety każdy błąd w oznaczeniu wyrobu, dostarczanego przez dostawcę, powoduje milionowe straty, na które duże marki nie mogą sobie pozwalać. Stąd też spora presja na dostawców, by przeciwdziałali tego typu incydentom.
Za podstawowy problem, który prowadzi do błędnego etykietowania, uznaje się bardzo często – człowieka. Firmy bowiem prześcigają się w coraz to nowych odkryciach, których zadaniem jest redukcja jego roli, albo nawet całkowita eliminacja człowieka w procesie etykietowania. Systemy te najczęściej zwane są ”Poka Yoke”, czyli w przełożeniu na język polski – odporne na błędy. Tymczasem wg jednego z twórców tego pojęcia – Shigeo Shingo – ”Poka Yoke to systemy odporne na błędy wynikające ze zmienności procesów, a nie na błędy, które może popełnić człowiek”.
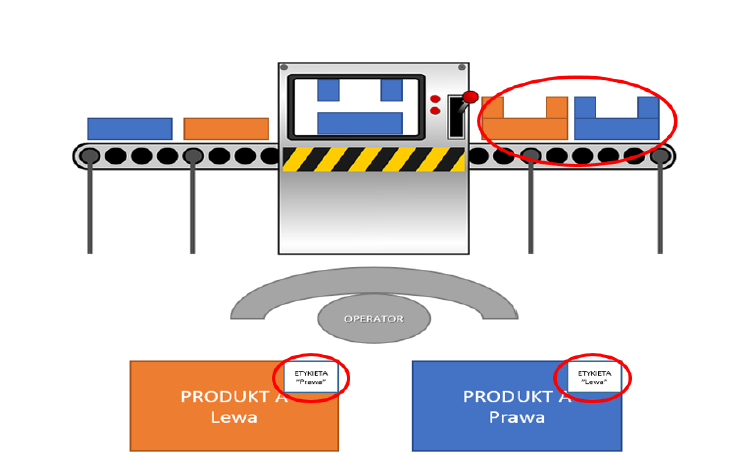
Rys. 2. Mislabeling na stanowiskach produkcyjnych powstaje w momencie, gdy operator np. oznaczając prawą stronę danej części, naklei na paletę - etykietę strony lewej lub gdy w paletę dedykowaną dla strony lewej umieści część prawą i w ten sposób pomiesza towar.
Kolejną najbardziej znaną, a zarazem najczęstszą przyczyną mislabelingu w firmach motoryzacyjnych są maszyny produkujące części, a także ich ustawienie. Dopiero na samym końcu ocenia się całościowy proces.
Właśnie dlatego też każde działania powinny być poprzedzone rzetelną analizą, która pomoże zdefiniować źródło problemu. W tym celu metody ”Problem Solving” zdają się być najlepszymi narzędziami do rozwiązania wszelkich problemów.
Każdą analizę wystąpienia mislabelingu rozpoczyna się od wyjaśnienia, na jakim obszarze problem pojawił się w pierwszej kolejności, ponieważ proces produkcji może odbywać się na kilku poziomach, w różnych miejscach. Stąd tak ważne jest odpowiednie wybranie metody do podjęcia dokładnej analizy.
Większość przedsiębiorstw na pierwszy ”rzut oka” wini zawsze człowieka - operatora produkcyjnego, logistycznego, czy też pracowników firm zewnętrznych, którzy przeprowadzają cząstkowe, bądź całościowe selekcje wyprodukowanego towaru. Często zdarza się jednak, że problemy pojawiają się z powodu błędnego procesu, nieodpornego na błędy ludzkie.
Właśnie dlatego ważne jest, aby przed rozpoczęciem zorganizować grupę, na którą składać się będą przedstawiciele różnych działów, na co dzień uczestniczących w rozpatrywanym procesie, np.: Logistyki, Jakości, Produkcji oraz CI (dział Ciągłego Doskonalenia). Następnie zgodnie z pierwszą zasadą Metody 5G, analizę powinno rozpocząć się na tzw. Gembie, czyli w miejscu, gdzie pojawił się dany problem (najczęściej są to obszary produkcyjne), na którym procesy bywają skomplikowane i różnorodne. Następnie za pomocą narzędzi takich jak: diagram Ishikawa, 5Why, czy 5W1H, warto rozpocząć cały proces analizy. Wtedy też powinno paść pierwsze pytanie: ”Czy mamy pewność, że problem pojawił się z powodu błędu ludzkiego”? Mimo, iż najczęściej jako źródło mislabelingu, postrzega się głównie człowieka, warto pamiętać, że tak naprawdę operatorzy są skarbnicą wiedzy. Nikt bowiem lepiej od nich - nie wie, co tak naprawdę sprawia, że problem pojawia się właśnie na ich stanowisku pracy. Dlatego dobry wywiad z operatorami na etapie analizy, może stanowić podstawę każdych kolejnych działań. Wówczas otrzymany obraz istniejącej sytuacji, pozwalających grupie specjalistów na zaplanowanie odpowiednich działań, które po wdrożeniu pozwolą na redukcję błędów, lub jej całkowitą eliminację, obniżając związane z tym straty.
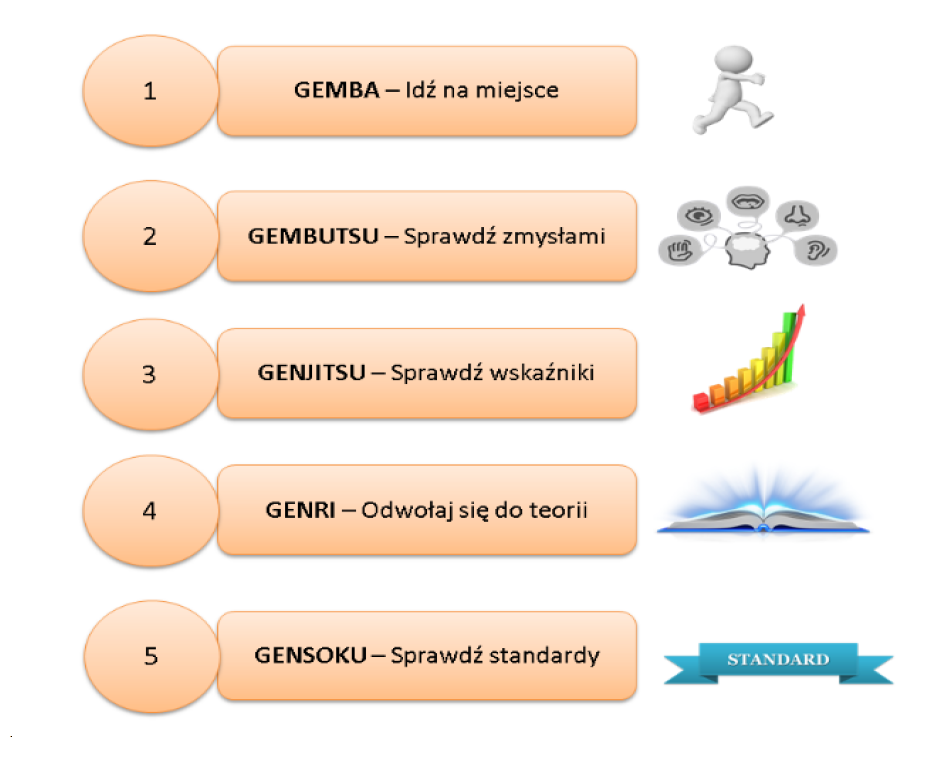
Rys. 3. Metoda 5G.
Redukcja, bądź całkowita eliminacja błędów w etykietowaniu wyrobu gotowego, pozwala nie tylko umocnić firmie swoją pozycję na rynku, czy też stać się rzetelnym dostawcą. Przede wszystkim pomaga w stworzeniu bazy rozwiązań, które z powodzeniem można implementować na nowe projekty, zwiększając tym samym swoją wydajność i tworząc przy tym odpowiednie warunki pracy ludziom, którzy swoją ciężką pracą przyczyniają się do zysków firmy.
Technologie wspierające Lean
PARTNERZY SEKCJI:
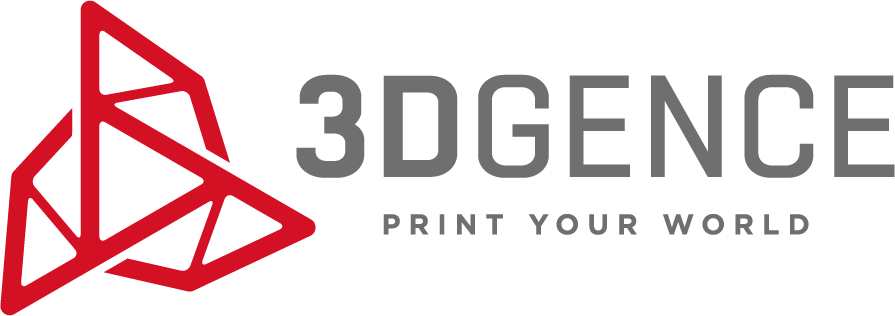
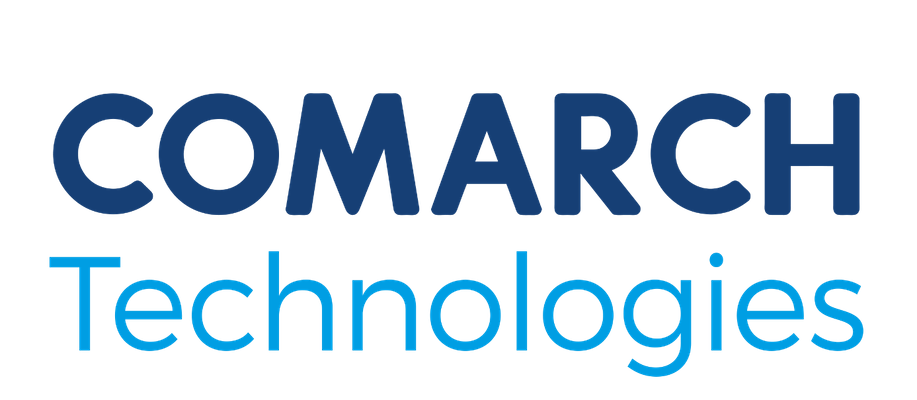
Śledź nas w social media
Aktualności
Ogólnopolski Kongres Jakościowy 2025: Wiedza. Relacje. Biznes.
Nowoczesne podejście do doskonalenia procesów - relacja z IX Europejskiego Kongresu Lean
PolecamyW dniach 14-16 maja 2025 roku w Centrum Edukacyjno-Kongresowym Politechniki Śląskiej odbędzie się Ogólnopolski Kongres Jakościowy 2025. To największe wydarzenie w Polsce poświęcone jakości, łączące wiedzę, relacje i biznes. Kongres stanowi unikalną o ...
Dziewiąta edycja Europejskiego Kongresu Lean przyniosła uczestnikom ogromną dawkę wiedzy na temat wdrażania efektywnych procesów i innowacji w różnych branżach. Organizatorzy podkreślali, że kluczowym przesłaniem wydarzenia jest przekonanie, że to, c ...
Kalendarz konferencji Lean
Najbliższe szkolenia Lean
Patronujemy Wyszukiwarka
Śledź nas na Facebooku