Projekty Lean
Projekt – grupowe zwolnienia. Czy starałem się na darmo?
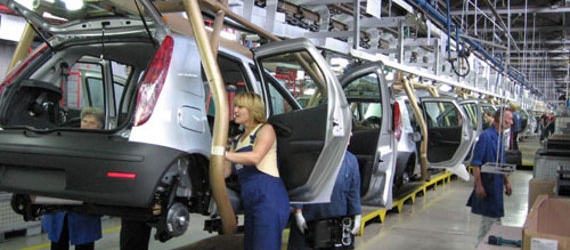
- Nazwa firmy
- Przemysł
- Status
- Wdrażany
Kiedy w zakładach przychodzi fala zwolnień, pracownicy firmy tracą zaufanie do pracodawców i rynku pracy, a także jeszcze mocniej zamykają się na wszelkie nowości, które mają przynieść usprawnienia procesów w firmie. Obecnie głośnym echem odbiły się informacje o zwolnieniach grupowych w jednym z największych zakładów motoryzacyjnych w Europie, zlokalizowanym na śląsku. Pracownicy, którzy w ramach systemu WCM zgłaszali swoje pomysły, obecnie nie są już potrzebni i niestety zadają sobie pytanie: „Czy warto było się starać?”
Wśród zwolnionych osób znajdują się niejednokrotnie pracownicy, którzy wykazywali się pomysłowością, zaangażowaniem, a ich wnioski przyczyniły się do zwiększenia bezpieczeństwa pracy, zmniejszenia ilości wadliwych części, czy uproszczenia procesu produkcji. Zakład, dla którego wytężali swoje ręce oraz umysły, "już ich nie potrzebuje i pozbywa się jak niepotrzebnej maszyny" – takie słowa niestety pojawiają się czasem z ich ust. W zasadzie pisząc ten artykuł, moglibyśmy potwierdzić prawdziwość powyższych stwierdzeń, postawić kropkę i zakończyć pracę. Jednak nie o to chodzi. Zastanówmy się, czy rzeczywiście warto mówić, że nie opłaca się angażować w pracy, jeśli i tak mogą nas zwolnić.
Działania Lean i Kaizen rzeczywiście w pierwszym oglądzie mogą sprawić wrażenie, że w zakładzie jest teoretycznie mniej pracy, a upraszczanie procesów wraz z robotyzacją może stanowić pewien problem. Na skutek zmian zakład nie musi już więcej płacić za to, co dotąd mogło go słono kosztować, a pieniądze te trafiały przecież między innymi do pracującego w danym procesie pracownika. W dodatku często z ust osób, które miały okazję pracować za granicą, słyszy się o tym, że „na zachodzie” pracuje się dużo łatwiej i wolniej niż w Polsce, a przy okazji za swoją pracę możemy otrzymać dużo większe wynagrodzenie. To niestety prawda, jednak już niejednokrotnie przekonaliśmy się o tym, że na dłuższą metę takie działanie nie popłaca. Jasne jest, że Polacy pracując wydajnie powinni zarabiać równie dobrze, jak operatorzy w zachodniej części Europy i musimy do tego dążyć. Jednak nie warto przynosić z zachodu przeświadczenia, że powinniśmy pracować powoli, jak Brytyjczycy. Efekty tego są już niestety widoczne i mało ciekawe dla Europejczyków. Warto tu choćby przytoczyć przenosiny produkcji komputerów z Irlandii do Polski (Dell), czy przesunięcia całych zakładów i linii montażowych między innymi z Francji, Austrii, Wielkiej Brytanii, Niemiec, a nawet Danii do naszego kraju (np. Volvo, Alstom, Nutricia, Danfoss). Dzieje się tak nie tylko dlatego, że jesteśmy jedną z najtańszych sił roboczych w Unii Europejskiej. Korporacje oraz ich klienci doceniają nas także za naszą chęć do pracy oraz produkcję wyrobów dobrej jakości.
Lean może być przyszłością dla operatora produkcji
Mimo trudności, które wynikają ze zwolnień w zakładach, warto dostrzec pewne plusy swojego zaangażowania. Przede wszystkim, jeżeli funkcjonujemy w przedsiębiorstwie, które swój rozwój opiera na systemie Kaizen (lub mu podobnym), w którym to zdanie operatora ma duży wpływ na przyszły kształt procesu, mamy szansę być bardziej wartościowym pracownikiem na rynku pracy. W dobie coraz bardziej uproszczonych operacji mogłoby się wydawać, że operator musi posiadać jedynie zdolność przekładania swojej ręki z jednej na drugą stronę. Otóż jest tak rzeczywiście tylko w przypadku, jeżeli w pracy wyznajemy zasadę: „Wymagają ode mnie przykręcenia śrubki, to przykręcam i niech się dzieje co chce...”. W dłuższej perspektywie czasu, śrubkę najprawdopodobniej będzie jednak przykręcał robot, a nasze stanowisko nie będzie potrzebne.
Warto więc zaangażować się w poznanie narzędzi Lean w swojej pracy z co najmniej kilku powodów:
-Wykorzystując swoje pomysły możemy doprowadzić do pozbycia się irytujących nas czynności z naszej codziennej pracy. Czasem naprawdę jest tak, że źle ustawione zadania, albo stanowiska są obecne tak długo, ponieważ informacja o nich z różnych powodów nie wyszła spoza kręgu brygady. W efekcie nie tylko zakład jest stratny, ale i sam pracownik, który w danym miejscu spędza osiem godzin dziennie. Angażując się w proces Kaizen sami upraszczamy sobie pracę (oczywiście przy założeniu, że nikt procesu poprawy nie utrudnia).
-Jeżeli spojrzymy na ogłoszenia o pracę, zauważymy że coraz częściej firmy starają się pozyskać kierowników, którzy znają działanie Lean. Dlatego nawet jeśli takie wymaganie nie jest zaznaczone w anonsie dla operatora, to ostatecznie wiedza z zakresu Lean Manufacturing będzie naszym atutem podczas rekrutacji dla takiej firmy. Powód jest prosty - kultura i narzędzia Lean mogą rzeczywiście działać tylko wtedy, gdy są one wdrażane przez wszystkich – począwszy od najniższego szczebla, aż po ostatni, dyrektorski. Warto przypomnieć sobie reguły 5S, szybkich przezbrojeń, czy prewencyjnego utrzymania maszyn. Jeszcze lepiej, jeżeli w zanadrzu mamy konkretne projekty usprawnień, które zainicjowano dzięki nam – przedstawmy je przyszłemu pracodawcy.
-Pracownicy działów bezpośrednio związanych z wdrożeniem i utrzymywaniem Lean Manufacturing w zakładzie mają czasem okazję zauważyć zmniejszenie napięcia pomiędzy pracownikami w dobrze zarządzanym zespole. Jeżeli zarządzający brygadą lider (lub kierownik) zgodnie z założeniami Lean, zauważa możliwości i starania swojego zespołu – brygada odwdzięcza mu się dobrze wykonaną pracą. Wystarczy tylko przypomnieć sobie, jak często powodem narzekań operatorów jest zła relacja pomiędzy przełożonym i pracownikiem lub niezdrowa konkurencja pomiędzy działami, które „muszą” ze sobą współpracować. Natomiast po wdrożeniu zmian, niejednokrotnie te same osoby przyznają, że sytuacja na ich odcinku się poprawiła. Jeżeli nie było tak w firmie posiadającej Lean, w której zwolniona osoba pracowała do tej pory – to gdzieś po prostu został popełniony błąd. Jednak te same zasady, oparte na szacunku względem siebie oraz świadomość potrzeby poszukiwania przyczyny problemu, a nie ustalenia winy, może nam pomóc w nowej pracy, a co więcej – także w życiu rodzinnym, osobistym (co jest potwierdzone przykładami z życia konkretnych osób z produkcji).
-Wreszcie patrząc globalnie, widzimy że firmy coraz częściej ryzykują otwarcie swoich fabryk w krajach południowo-wschoniej Europy, w których płace są jeszcze niższe. To może oznaczać, że rynek pracy w Polsce w pewnym momencie zacznie się kurczyć. Jeżeli okaże się, że ryzyko się opłaciło, w przyszłości duże firmy będą chętniej wybierać inwestycje w biedniejszych regionach kontynentu. Wtedy na polskim rynku pozostaną operatorzy produkcji, którzy de facto nie będą umieć nic więcej niż to, czego nauczyli się na swoich stanowiskach. I wtedy będziemy mogli zdobywać kolejne zlecenia jedynie dzięki swojej pomysłowości i najwyższej jakości wykonania.
Jeżeli ktoś nadal ma wątpliwości, czy warto się było angażować – powinien raz i ostatecznie stwierdzić, że mimo wszystko warto, by móc ponownie wykorzystać swoje (nie tylko produkcyjne) umiejętności w ramach przyszłego zatrudnienia, albo wykorzystać je współpracując z ludźmi ze swojej lokalnej społeczności, która w czasach tak zwanego kryzysu, poprzez współpracę i pomysłowość może nie tylko uniknąć kłopotów, ale i wzbogacić się oraz rosnąć w siłę (co pokazują Hiszpanie wprowadzając swoje lokalne waluty i poddźwigając się lokalnie z nędzy i bezrobocia). Dodatkowo powinniśmy pamiętać, że to często przez brak zaangażowania pracowników na wszystkich szczeblach i biurokrację, wiele polskich przedsiębiorstw upadło, bądź zostało sprzedanych. Uproszczenia związane z Lean i wnioskami Kaizen mogą pomóc, co pokazała Japonia, która od biedy oraz zerowego przemysłu i kiepskiej jakości w latach 1945-50, doszła do rangi wielkiego, uznanego producenta już kilkadziesiąt lat później. My zawsze możemy powoływać się na motto „Polak potrafi” i wykorzystać tę cechę także wtedy, gdy wielkie koncerny ogłaszają swoje problemy i wprowadzają grupowe zwolnienia.
Działania Lean i Kaizen rzeczywiście w pierwszym oglądzie mogą sprawić wrażenie, że w zakładzie jest teoretycznie mniej pracy, a upraszczanie procesów wraz z robotyzacją może stanowić pewien problem. Na skutek zmian zakład nie musi już więcej płacić za to, co dotąd mogło go słono kosztować, a pieniądze te trafiały przecież między innymi do pracującego w danym procesie pracownika. W dodatku często z ust osób, które miały okazję pracować za granicą, słyszy się o tym, że „na zachodzie” pracuje się dużo łatwiej i wolniej niż w Polsce, a przy okazji za swoją pracę możemy otrzymać dużo większe wynagrodzenie. To niestety prawda, jednak już niejednokrotnie przekonaliśmy się o tym, że na dłuższą metę takie działanie nie popłaca. Jasne jest, że Polacy pracując wydajnie powinni zarabiać równie dobrze, jak operatorzy w zachodniej części Europy i musimy do tego dążyć. Jednak nie warto przynosić z zachodu przeświadczenia, że powinniśmy pracować powoli, jak Brytyjczycy. Efekty tego są już niestety widoczne i mało ciekawe dla Europejczyków. Warto tu choćby przytoczyć przenosiny produkcji komputerów z Irlandii do Polski (Dell), czy przesunięcia całych zakładów i linii montażowych między innymi z Francji, Austrii, Wielkiej Brytanii, Niemiec, a nawet Danii do naszego kraju (np. Volvo, Alstom, Nutricia, Danfoss). Dzieje się tak nie tylko dlatego, że jesteśmy jedną z najtańszych sił roboczych w Unii Europejskiej. Korporacje oraz ich klienci doceniają nas także za naszą chęć do pracy oraz produkcję wyrobów dobrej jakości.
Lean może być przyszłością dla operatora produkcji
Mimo trudności, które wynikają ze zwolnień w zakładach, warto dostrzec pewne plusy swojego zaangażowania. Przede wszystkim, jeżeli funkcjonujemy w przedsiębiorstwie, które swój rozwój opiera na systemie Kaizen (lub mu podobnym), w którym to zdanie operatora ma duży wpływ na przyszły kształt procesu, mamy szansę być bardziej wartościowym pracownikiem na rynku pracy. W dobie coraz bardziej uproszczonych operacji mogłoby się wydawać, że operator musi posiadać jedynie zdolność przekładania swojej ręki z jednej na drugą stronę. Otóż jest tak rzeczywiście tylko w przypadku, jeżeli w pracy wyznajemy zasadę: „Wymagają ode mnie przykręcenia śrubki, to przykręcam i niech się dzieje co chce...”. W dłuższej perspektywie czasu, śrubkę najprawdopodobniej będzie jednak przykręcał robot, a nasze stanowisko nie będzie potrzebne.
Warto więc zaangażować się w poznanie narzędzi Lean w swojej pracy z co najmniej kilku powodów:
-Wykorzystując swoje pomysły możemy doprowadzić do pozbycia się irytujących nas czynności z naszej codziennej pracy. Czasem naprawdę jest tak, że źle ustawione zadania, albo stanowiska są obecne tak długo, ponieważ informacja o nich z różnych powodów nie wyszła spoza kręgu brygady. W efekcie nie tylko zakład jest stratny, ale i sam pracownik, który w danym miejscu spędza osiem godzin dziennie. Angażując się w proces Kaizen sami upraszczamy sobie pracę (oczywiście przy założeniu, że nikt procesu poprawy nie utrudnia).
-Jeżeli spojrzymy na ogłoszenia o pracę, zauważymy że coraz częściej firmy starają się pozyskać kierowników, którzy znają działanie Lean. Dlatego nawet jeśli takie wymaganie nie jest zaznaczone w anonsie dla operatora, to ostatecznie wiedza z zakresu Lean Manufacturing będzie naszym atutem podczas rekrutacji dla takiej firmy. Powód jest prosty - kultura i narzędzia Lean mogą rzeczywiście działać tylko wtedy, gdy są one wdrażane przez wszystkich – począwszy od najniższego szczebla, aż po ostatni, dyrektorski. Warto przypomnieć sobie reguły 5S, szybkich przezbrojeń, czy prewencyjnego utrzymania maszyn. Jeszcze lepiej, jeżeli w zanadrzu mamy konkretne projekty usprawnień, które zainicjowano dzięki nam – przedstawmy je przyszłemu pracodawcy.
-Pracownicy działów bezpośrednio związanych z wdrożeniem i utrzymywaniem Lean Manufacturing w zakładzie mają czasem okazję zauważyć zmniejszenie napięcia pomiędzy pracownikami w dobrze zarządzanym zespole. Jeżeli zarządzający brygadą lider (lub kierownik) zgodnie z założeniami Lean, zauważa możliwości i starania swojego zespołu – brygada odwdzięcza mu się dobrze wykonaną pracą. Wystarczy tylko przypomnieć sobie, jak często powodem narzekań operatorów jest zła relacja pomiędzy przełożonym i pracownikiem lub niezdrowa konkurencja pomiędzy działami, które „muszą” ze sobą współpracować. Natomiast po wdrożeniu zmian, niejednokrotnie te same osoby przyznają, że sytuacja na ich odcinku się poprawiła. Jeżeli nie było tak w firmie posiadającej Lean, w której zwolniona osoba pracowała do tej pory – to gdzieś po prostu został popełniony błąd. Jednak te same zasady, oparte na szacunku względem siebie oraz świadomość potrzeby poszukiwania przyczyny problemu, a nie ustalenia winy, może nam pomóc w nowej pracy, a co więcej – także w życiu rodzinnym, osobistym (co jest potwierdzone przykładami z życia konkretnych osób z produkcji).
-Wreszcie patrząc globalnie, widzimy że firmy coraz częściej ryzykują otwarcie swoich fabryk w krajach południowo-wschoniej Europy, w których płace są jeszcze niższe. To może oznaczać, że rynek pracy w Polsce w pewnym momencie zacznie się kurczyć. Jeżeli okaże się, że ryzyko się opłaciło, w przyszłości duże firmy będą chętniej wybierać inwestycje w biedniejszych regionach kontynentu. Wtedy na polskim rynku pozostaną operatorzy produkcji, którzy de facto nie będą umieć nic więcej niż to, czego nauczyli się na swoich stanowiskach. I wtedy będziemy mogli zdobywać kolejne zlecenia jedynie dzięki swojej pomysłowości i najwyższej jakości wykonania.
Jeżeli ktoś nadal ma wątpliwości, czy warto się było angażować – powinien raz i ostatecznie stwierdzić, że mimo wszystko warto, by móc ponownie wykorzystać swoje (nie tylko produkcyjne) umiejętności w ramach przyszłego zatrudnienia, albo wykorzystać je współpracując z ludźmi ze swojej lokalnej społeczności, która w czasach tak zwanego kryzysu, poprzez współpracę i pomysłowość może nie tylko uniknąć kłopotów, ale i wzbogacić się oraz rosnąć w siłę (co pokazują Hiszpanie wprowadzając swoje lokalne waluty i poddźwigając się lokalnie z nędzy i bezrobocia). Dodatkowo powinniśmy pamiętać, że to często przez brak zaangażowania pracowników na wszystkich szczeblach i biurokrację, wiele polskich przedsiębiorstw upadło, bądź zostało sprzedanych. Uproszczenia związane z Lean i wnioskami Kaizen mogą pomóc, co pokazała Japonia, która od biedy oraz zerowego przemysłu i kiepskiej jakości w latach 1945-50, doszła do rangi wielkiego, uznanego producenta już kilkadziesiąt lat później. My zawsze możemy powoływać się na motto „Polak potrafi” i wykorzystać tę cechę także wtedy, gdy wielkie koncerny ogłaszają swoje problemy i wprowadzają grupowe zwolnienia.
Technologie wspierające Lean
PARTNERZY SEKCJI:
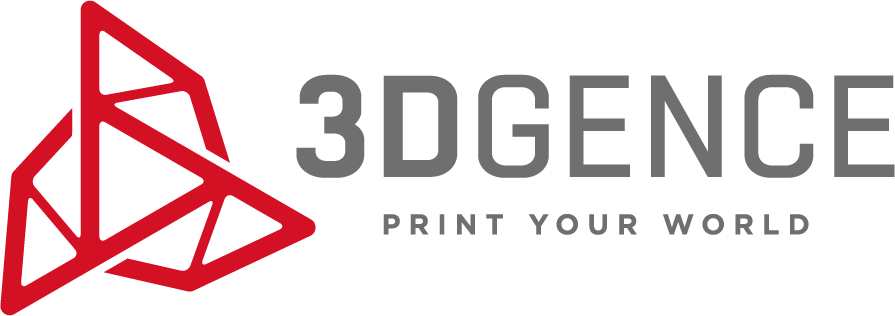
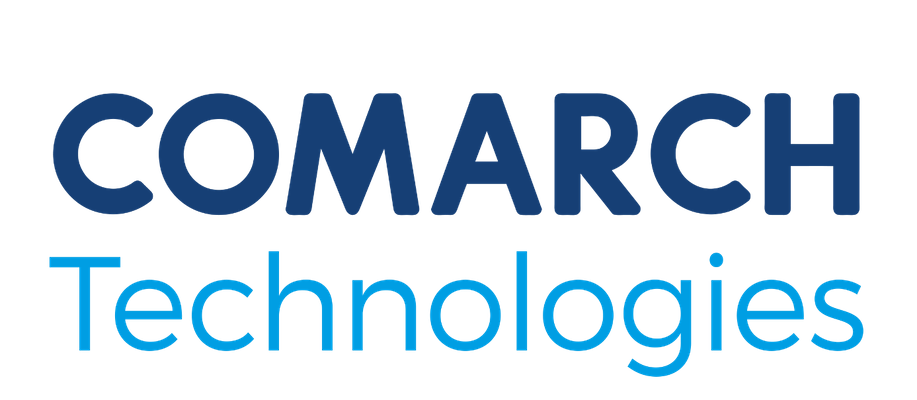
Śledź nas w social media
Aktualności
Ogólnopolski Kongres Jakościowy 2025: Wiedza. Relacje. Biznes.
Nowoczesne podejście do doskonalenia procesów - relacja z IX Europejskiego Kongresu Lean
PolecamyW dniach 14-16 maja 2025 roku w Centrum Edukacyjno-Kongresowym Politechniki Śląskiej odbędzie się Ogólnopolski Kongres Jakościowy 2025. To największe wydarzenie w Polsce poświęcone jakości, łączące wiedzę, relacje i biznes. Kongres stanowi unikalną o ...
Dziewiąta edycja Europejskiego Kongresu Lean przyniosła uczestnikom ogromną dawkę wiedzy na temat wdrażania efektywnych procesów i innowacji w różnych branżach. Organizatorzy podkreślali, że kluczowym przesłaniem wydarzenia jest przekonanie, że to, c ...
Kalendarz konferencji Lean
Najbliższe szkolenia Lean
Patronujemy Wyszukiwarka
- 08.07.2025 Otwarte szkolenie Lean Koromo
- 06.08.2025 Szkolenie Lean z grą Koromo w firmie Scanfil
Śledź nas na Facebooku