Projekty Lean
Działania na rzecz jakości Dantotsu
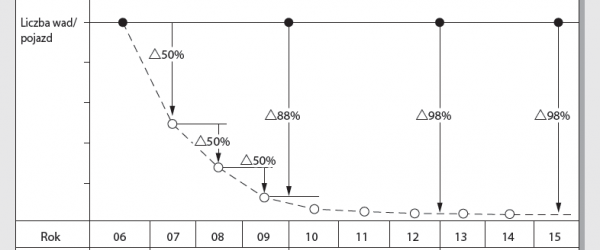
Fragment książki Sadao Nomury „Droga Toyoty do doskonałej jakości”.
Będąc przekonanym, że jakość jest podstawową zasadą Toyoty, przez wiele lat pracowałem nad jej poprawą w Oddziale Pojazdów Przemysłowych Toyota Industries, a następnie wziąłem udział w działaniach na rzecz jakości Dantotsu prowadzonych w całej grupie. Celem było uzyskanie jakości, dzięki której zdecydowanie pokonalibyśmy konkurencję.
Będąc przekonanym, że jakość jest podstawową zasadą Toyoty, przez wiele lat pracowałem nad jej poprawą w Oddziale Pojazdów Przemysłowych Toyota Industries, a następnie wziąłem udział w działaniach na rzecz jakości Dantotsu prowadzonych w całej grupie. Celem było uzyskanie jakości, dzięki której zdecydowanie pokonalibyśmy konkurencję.
Rezultaty podjętych wysiłków sumowały się przez dziewięć lat: podczas Dantotsu-I (2007–2009), Dantotsu-II (2010–2012) i Dantotsu-III (2013–2015) i znacznie przewyższyły oczekiwania każdego, kto w nich uczestniczył. Czerpiąc satysfakcję z tak dobrych wyników, pracownicy zagranicznych zakładów uznali, że działania na rzecz jakości Dantotsu tworzą niezwykle skuteczną metodę poprawy jakości i wspaniałomyślnie nazwali ją „metodą Nomury”. Wyniki przedstawiam poniżej.
1. Cele i wyniki działań na rzecz jakości Dantotsu
(1) Zmniejszenie liczby wad na pojazd podczas kontroli gotowych pojazdów
Za reprezentatywny przykład mogą posłużyć wyniki głównej linii zakładu w Takahamie w Japonii przedstawione na schemacie 16-1.
W okresie Dantotsu-I (2007–2009) nastąpiły poważne zmiany, takie jak uruchomienie produkcji nowego modelu i spadek wielkości produkcji spowodowany kryzysem finansowym z lat 2007–2008 (zwanym w Japonii szokiem Lehmana). Wówczas jakość produktu gwałtownie się pogorszyła. Jednak po roku 2010, kiedy pracownicy zaczęli rozumieć podstawy produkcji, byli już w stanie reagować na zmiany i w końcu osiągnęli cel (schemat 16-2), doprowadzając do zmniejszenia liczby wad wykrytych podczas kontroli gotowych pojazdów o 98%. Dzięki temu możliwe stało się dostarczenie na rynek prawie wszystkich pojazdów schodzących z linii bez przeróbek, co pozwoliło wyeliminować problem opóźnień w dostawach. Marnotrawstwo pracy i materiałów oraz powierzchni niezbędnej na przerabianie lub naprawianie wadliwych pojazdów zostało zdecydowanie zmniejszone, co spowodowało duże obniżenie kosztów produkcji.
Jednym z dużych osiągnięć działań na rzecz jakości Dantotsu było to, że w sześciu zagranicznych zakładach także uzyskano redukcję wad na poziomie od 91 do 98%, co umożliwiło stabilną produkcję w grupie na całym świecie.
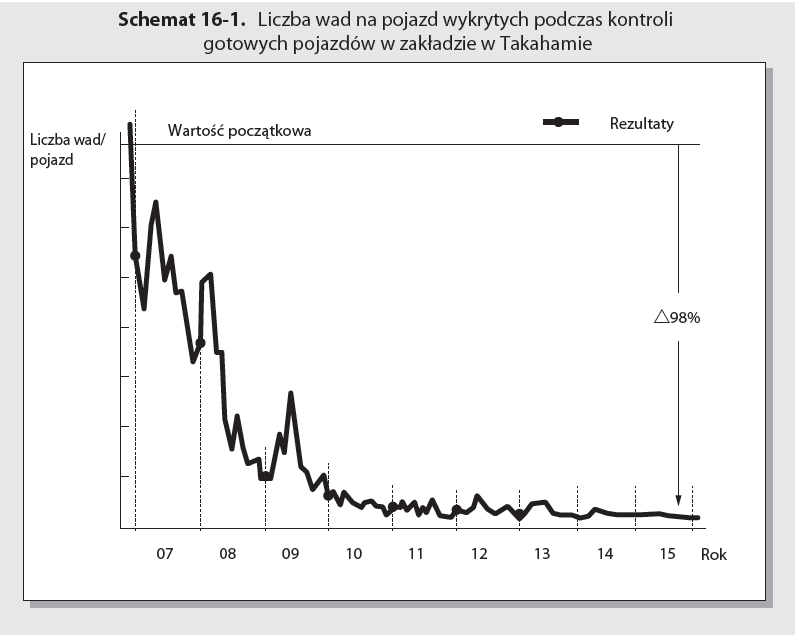
Schemat 16-1. Liczba wad na pojazd wykrytych podczas kontroli gotowych pojazdów w zakładzie w Takahamie
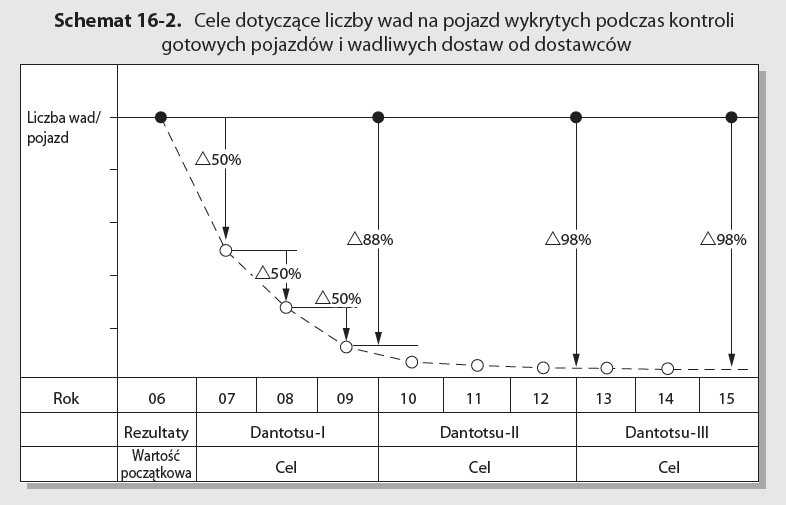
Schemat 16-2. Cele dotyczące liczby wad na pojazd wykrytych podczas kontroli gotowych pojazdów i wadliwych dostaw od dostawców
(2) Liczba wadliwych dostaw od dostawców
Wskaźnik redukcji wad w dostawach do zakładu w Takahamie osiągnął 86%, czyli nieco poniżej docelowego poziomu 98% (schemat 16-3). Mimo że cel nie został jeszcze osiągnięty, zdecydowany spadek liczby wadliwych dostaw doprowadził do znacznej redukcji problemów podczas montażu pojazdów, co umożliwiło płynną pracę linii.
Jednocześnie po stronie dostawców możliwe stało się istotne ograniczenie takich dodatkowych prac, jak ponowna dostawa, naprawa, przegląd pozycji magazynowych, przygotowanie planu/raportu środków zaradczych itp., a zaoszczędzone w ten sposób dodatkowe koszty materiałów, pracy i energii pozwoliły zwiększyć im rentowność.
W Japonii istnieje ścisły związek między zakładami produkującymi pojazdy a dostawcami części, trochę jak w relacji rodzic – dziecko. Dostawcy dobrze wiedzą, że są w stanie stale zmniejszać liczbę wad, stosując się rzetelnie do tego, czego nauczył ich – niczym rodzić – zakład produkujący pojazdy. Natomiast sytuacja jest zgoła inna, jeśli chodzi o zagranicznych dostawców części i zakłady produkujące pojazdy. Tu relacje oparte są na równości i nieczęsto zdarza się, aby zakłady udzielały dostawcom części wskazówek na temat poprawy jakości produktów. Z tego powodu istnieje różnica w przebiegu redukcji wadliwych dostaw między zakładem w Takahamie a zakładami zagranicznymi, co przedstawiono na schemacie 16-4.
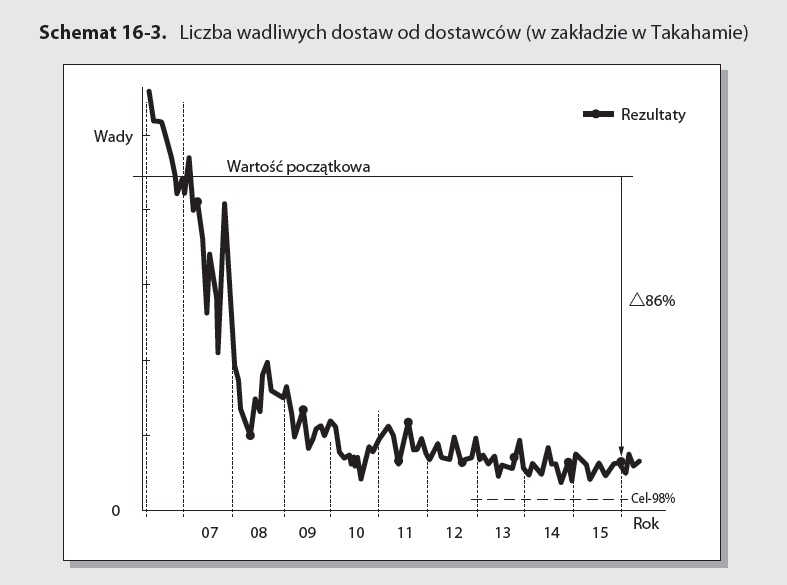
Schemat 16-3. Liczba wadliwych dostaw od dostawców (w zakładzie w Takahamie)

Schemat 16-4. Liczba wadliwych dostaw od dostawców w dwóch zakładach zagranicznych
Poza Japonią powszechną praktyką jest zakup części, jeśli ich jakość jest dobra, a jeśli się pogorszy, kontrakt jest rozwiązywany i części zamawia się u innego dostawcy. W takich miejscach, gdzie zwyczaje różnią się od japońskich, odwiedziłem kilka firm produkcyjnych dostarczających części najgorszej jakości. Towarzyszyli mi członkowie „zespołu wsparcia poprawy jakości dostawców” z naszego działu zapewnienia jakości. Razem zaczęliśmy udzielać im wskazówek na temat wizualizacji, metody 8 kroków itp.
Chociaż przez pierwsze dwa lata efekty były słabo widoczne, ich zainteresowanie działaniami rosło stopniowo, w miarę jak na własne oczy (genchi genbutsu) obserwowali rezultaty (szybki spadek liczby wadliwych pojazdów) w miejscach wykonywania rzeczywistej pracy (zakład produkujący pojazdy). Sprawiło to, że liczba firm prowadzących proaktywne działania na rzecz jakości Dantotsu się zwiększała. Aby jeszcze bardziej wzmocnić ich motywację, najlepszym dostawcom daliśmy możliwość przedstawienia prezentacji na temat ich radykalnego zmniejszenia liczb wad jakościowych podczas corocznych konferencji dostawców. Innymi sposobami wpłynięcia na nich były np. prezentowanie dostawcom rzeczywistych efektów poprawy jakości w naszym zakładzie produkującym pojazdy oraz tworzenie instrukcji tekstowych dotyczących zapewnienia jakości (na podstawie moich notatek), aby nauczyć ich, co i jak powinni robić. W wyniku tych ciągłych wysiłków podejmowanych w Stanach Zjednoczonych i Europie liczba wadliwych dostaw zmniejszyła się w podobny sposób, co widać na obu schematach. Raymond Corporation zdobyła w 2014 roku m.in. Best Plant Award przyznawaną przez amerykański magazyn „Industry Week” i ogłosiła szczegóły swoich działań na rzecz jakości Dantotsu podczas ceremonii wręczenia nagrody, wzbudzając zainteresowanie innych firm i wywołując w nich chęć skorzystania z naszych wskazówek. Dzięki temu udało się zmniejszyć liczbę wadliwych dostaw o 88%. Był to owoc moich szczerych i wytrwałych wysiłków poświęconych działaniom na rzecz jakości Dantotsu przez minione dziewięć lat.
(3) Cel redukcji roszczeń reklamacyjnych z rynku i jego osiągnięcie
Jako punkt odniesienia (100%) wykorzystaliśmy dane dotyczące kosztów roszczeń reklamacyjnych z rynku oraz ich całkowitą sumę z 2006 roku i wyznaczyliśmy cel zmniejszenia jej o połowę co trzy lata. Następnie zachęciliśmy każdy zakład do przeprowadzenia działań od Dantotsu-I do Dantotsu-III, tak aby uzyskać redukcję na poziomie 88%.
W rezultacie, jak widać na schemacie 16-5, firma „F” osiągnęła cel redukcji na poziomie 93%, co uważano za nieosiągalne. Następnie firmy „D” i „E” zbliżyły się do poziomów odpowiednio 78% i 80% redukcji.
Jeśli chodzi o całą grupę, udało nam się zmniejszyć łączną kwotę wypłat z tytułu roszczeń reklamacyjnych z rynku o 65%. Szczególnie duży wkład w ten wynik miały spotkania asaichi poświęcone roszczeniom, zainicjowane w 2011 roku. Podczas tych spotkań skutecznie prowadzono m.in. następujące działania: sprawdzanie przez wszystkie właściwe osoby – codziennie rano – reklamowanych części zwracanych przez dealerów, ustalanie osoby odpowiedzialnej za środki zaradcze oraz ich szybkie wdrażanie. Ponadto korzystne zmiany przyniosły także nowe inicjatywy, takie jak działania w celu redukcji zanieczyszczeń (z udziałem dostawców) oraz cotygodniowe spotkania przeglądowe dotyczące kwestii związanych z projektowaniem (części/podzespołów/wyrobów).
Działania opisane w rozdziale 14, mające zapobiegać wydostawaniu się wad na rynek dzięki poprawie jakości projektowania i metod przygotowania produkcji, dopiero się rozpoczęły, ale jestem przekonany, że entuzjastyczne wysiłki w każdej z firm prędzej czy później przyniosą efekty. We wszystkich tych organizacjach powstają indywidualne instrukcje SE dla poszczególnych obszarów, na każdym etapie projektowania, prototypu i produkcji prowadzi się kontrolę jakości przy użyciu list kontrolnych SE, a różnego rodzaju problemy są rozwiązywane w „najlepszym” (etap projektowania) lub „lepszym” (etap prototypu lub przygotowania produkcji) czasie. Jeśli pracownicy będą zdolni do skutecznego rozwiązywania problemów, redukcja kosztów roszczeń reklamacyjnych z rynku na poziomie 90% nie będzie już tylko marzeniem.
Działania na rzecz jakości Dantotsu pozwoliły uzyskać 65-procentowe oszczędności kosztów, jeśli chodzi o roszczenia reklamacyjne z rynku, dzięki czemu usunięto dużą część strat finansowych, a to z kolei przyczyniło się w istotny sposób do poprawy rentowności całej grupy. Ponadto zmniejszenie liczby wad przedostających się na rynek zwiększyło poziom zadowolenia klientów, co doprowadziło do zwiększenia naszego w nim udziału.
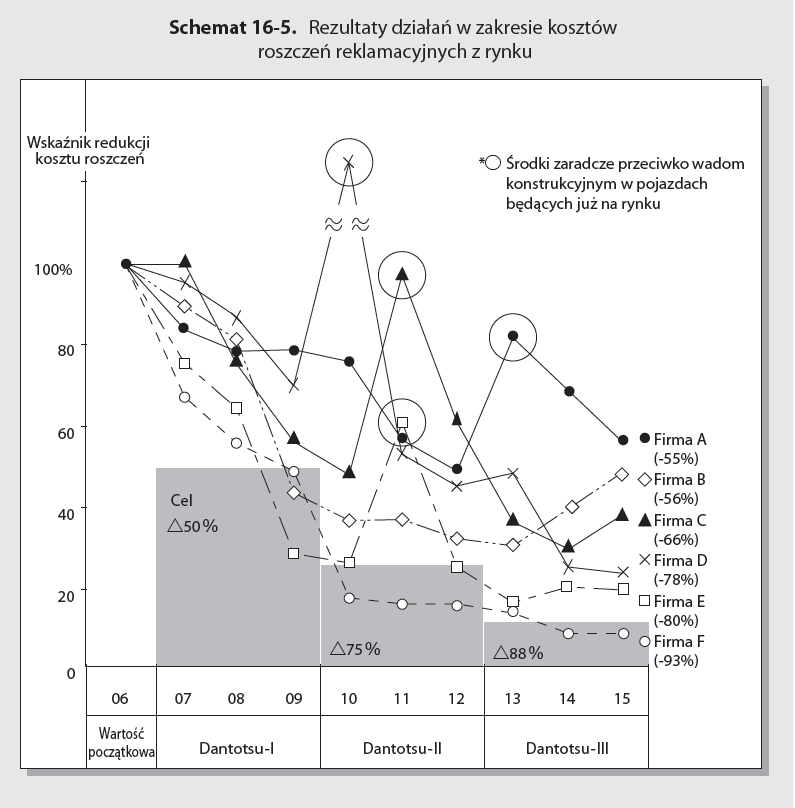
Schemat 16-5. Rezultaty działań w zakresie kosztów roszczeń reklamacyjnych z rynku
2. Ważne wskazówki w działaniach na rzecz jakości Dantotsu
Poniżej przedstawiam wskazówki niezbędne w poprawie jakości, których wielokrotnie udzielałem firmom w ramach działań na rzecz jakości Dantotsu. Jestem przekonany, że te pomysły i zabiegi miały wielką wagę dla działań we wszystkich krajach i dla uzyskania korzystnych rezultatów (schemat 16-6).
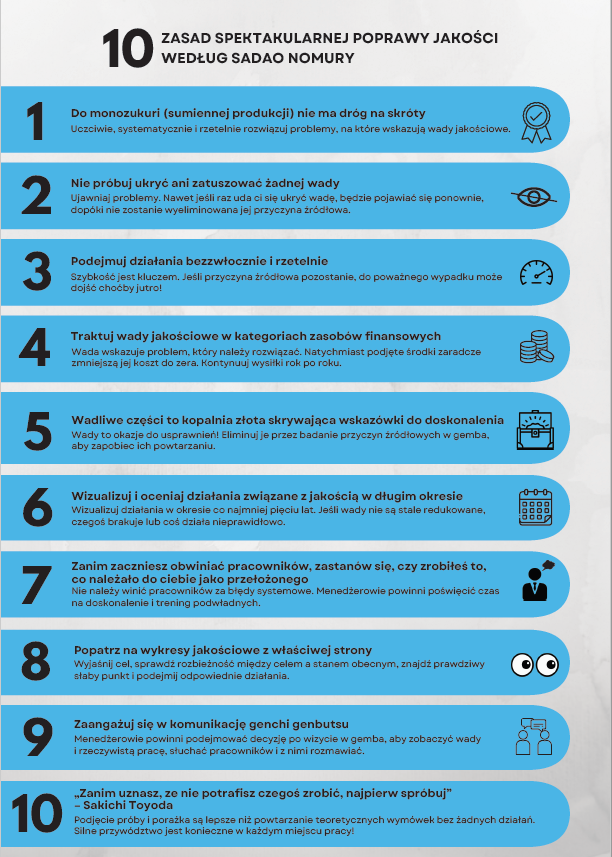
Schemat 16-6. 10 wskazówek w działaniach na rzecz jakości Dantotsu
3. Pomysły i działania zmierzające do uzyskania korzystnych rezultatów
Wysiłki całej firmy muszą prowadzić do satysfakcjonujących rezultatów. Jako doradca ds. jakości opisuję niektóre z pomysłów, które stały się swoistą siłą napędową działań na rzecz jakości Dantotsu i właśnie takie rezultaty przyniosły.
(1) Pobudzanie motywacji poprzez rywalizację w zakresie poprawy jakości między zakładami w różnych krajach
Ustandaryzowaliśmy cele jakościowe i wskaźniki jakościowe dla sześciu zakładów należących do Oddziału Pojazdów Przemysłowych, aby umożliwić uczciwe porównanie, i skłoniliśmy je do wzajemnej rywalizacji w zakresie poprawy jakości (schemat 16-7). Dzięki temu wszyscy pracownicy wiedzieli, czy jakość w zakładzie jest lepsza czy gorsza od innych, co wywołało ich entuzjazm do własnych działań w celu poprawy jakości. Wszyscy bowiem chcieli zdobyć pierwsze miejsce. Kolejną zmianą było usprawnienie komunikacji i zacieśnienie relacji między zakładami. Wcześniej ich pracownicy rzadko się odwiedzali. Po rozpoczęciu działań na rzecz jakości Dantotsu, gdy usłyszano, że jakiś zakład wdraża skuteczne rozwiązania, szybko wybierano się tam z wizytą, aby dowiedzieć się czegoś pożytecznego.
Początkowo działania związane z jakością Dantotsu w zakładzie w Takahamie nie były zbyt intensywne. Wynikało to z przekonania tamtejszych pracowników, że pod względem jakości ich zakład jest znacznie lepszy od fabryk za granicą. Niemniej niecały rok później, odwiedziwszy kilka zagranicznych zakładów, dyrektor Takahamy stwierdził krótko: „Przegrywamy z nimi”. Odtąd zaczęli poważniej pracować nad poprawą jakości. Najlepszym sposobem, by zmotywować nastawioną mało entuzjastycznie załogę danego zakładu jest pokazanie jej wyników osiąganych przez lepsze zakłady.
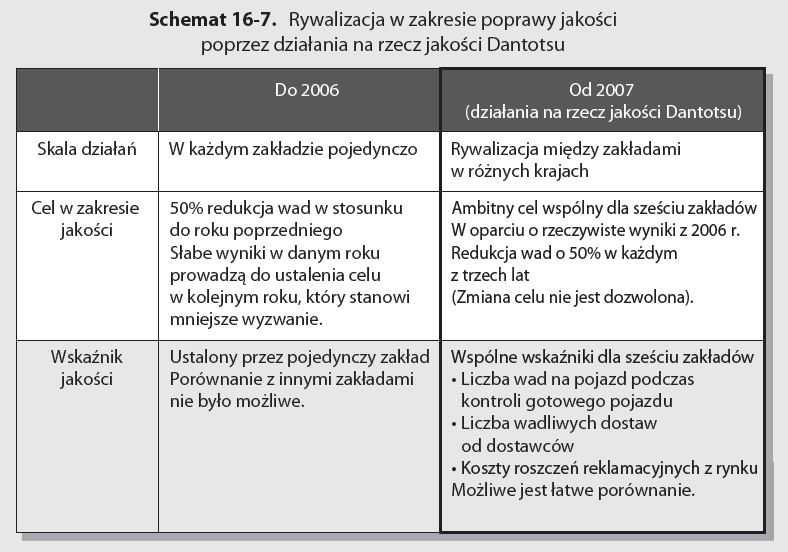
Schemat 16-7. Rywalizacja w zakresie poprawy jakości poprzez działania na rzecz jakości Dantotsu
(2) Ustalenie kolejności kroków doskonalenia jakości i tworzenie instrukcji tekstowych
Na podstawie wiedzy zgromadzonej podczas działań związanych z poprawą jakości w zakładach Toyota Motor Corporation: w zakładzie Motomachi, w Toyota Australia i Toyota South Africa ustaliłem priorytety wśród działań na rzecz jakości Dantotsu i ręcznie zapisałem każdą pozycję na kartce formatu A3. Każdorazowo, kiedy odwiedzałem zagraniczne zakłady (raz na cztery miesiące), wyjaśniałem wszystkie te teksty i instruowałem pracowników, co mają robić na ich podstawie. Działania były prowadzone w następującej kolejności: wizualizacja (rozdział 2), metoda 8 kroków (rozdział 3), standaryzacja (rozdziały 4, 5 i 6), edukacja i trening (rozdział 7) oraz zarządzanie słabymi punktami (rozdział 8). Jeśli chodzi o te kwestie, których trudno nauczyć tylko za pomocą tekstu i wskazówek w miejscu pracy, wyjaśnialiśmy je na rzeczywistych przykładach podczas szkolenia z TPS w Japonii. Pozwalało to pracownikom dogłębnie je zrozumieć.
Bardzo ważne jest, aby krok po kroku podnosić poziom szkolenia. Dołączam do niniejszej książki, na końcu tego rozdziału, swoje odręczne notatki nr 124 i 220, dotyczące metody 8 kroków. Chciałbym, aby czytelnicy poczuli energię i zapał, które towarzyszyły mi podczas ich tworzenia.
(3) Staranne wdrożenie działań następczych
Odwiedzałem każdy zakład co cztery miesiące i sprawdzałem postępy w realizacji tego, czego nauczyłem ich załogi poprzez genchi genbutsu. Przez kilka dni po osiem godzin dziennie w każdym zakładzie sprawdzałem stan aktualny i w danym miejscu wskazywałem, czego brakuje lub gdzie popełnia się błędy. Następnie, z wykorzystaniem notatek w formacie A3, uczyłem ludzi kolejnych kroków. Po powrocie do hotelu musiałem podsumować problemy znalezione tego dnia, zastanowić się nad środkami zaradczymi, a następnie na kartce A3 zapisać po angielsku kolejne wyzwania. Kartka ta stanowiła dla nich kolejne zadanie. Aby stworzyć tekst o takiej objętości, długo zastanawiałem się, jak sformułować myśli, jakie wykorzystać fotografie i jakich użyć tabel, by łatwo było wszystko zrozumieć. W rezultacie brakowało mi czasu na porządny sen. Ale taka była moja praca. W ostatnim dniu wizyty przekazywałem im kopię swojej notatki (arkusza tekstu), wyjaśniałem szczegóły i potwierdzałem, co muszą zrobić. Następnie wracałem do Japonii.
Wizualizując zobowiązania złożone przez pracowników na piśmie (notatka z zadaniami domowymi) oraz wdrażając rzetelnie działania następcze, do pracy nad poprawą jakości można zmotywować pracowników nawet w tych zakładach, w których są oni nastawieni mniej entuzjastycznie.
1. Cele i wyniki działań na rzecz jakości Dantotsu
(1) Zmniejszenie liczby wad na pojazd podczas kontroli gotowych pojazdów
Za reprezentatywny przykład mogą posłużyć wyniki głównej linii zakładu w Takahamie w Japonii przedstawione na schemacie 16-1.
W okresie Dantotsu-I (2007–2009) nastąpiły poważne zmiany, takie jak uruchomienie produkcji nowego modelu i spadek wielkości produkcji spowodowany kryzysem finansowym z lat 2007–2008 (zwanym w Japonii szokiem Lehmana). Wówczas jakość produktu gwałtownie się pogorszyła. Jednak po roku 2010, kiedy pracownicy zaczęli rozumieć podstawy produkcji, byli już w stanie reagować na zmiany i w końcu osiągnęli cel (schemat 16-2), doprowadzając do zmniejszenia liczby wad wykrytych podczas kontroli gotowych pojazdów o 98%. Dzięki temu możliwe stało się dostarczenie na rynek prawie wszystkich pojazdów schodzących z linii bez przeróbek, co pozwoliło wyeliminować problem opóźnień w dostawach. Marnotrawstwo pracy i materiałów oraz powierzchni niezbędnej na przerabianie lub naprawianie wadliwych pojazdów zostało zdecydowanie zmniejszone, co spowodowało duże obniżenie kosztów produkcji.
Jednym z dużych osiągnięć działań na rzecz jakości Dantotsu było to, że w sześciu zagranicznych zakładach także uzyskano redukcję wad na poziomie od 91 do 98%, co umożliwiło stabilną produkcję w grupie na całym świecie.
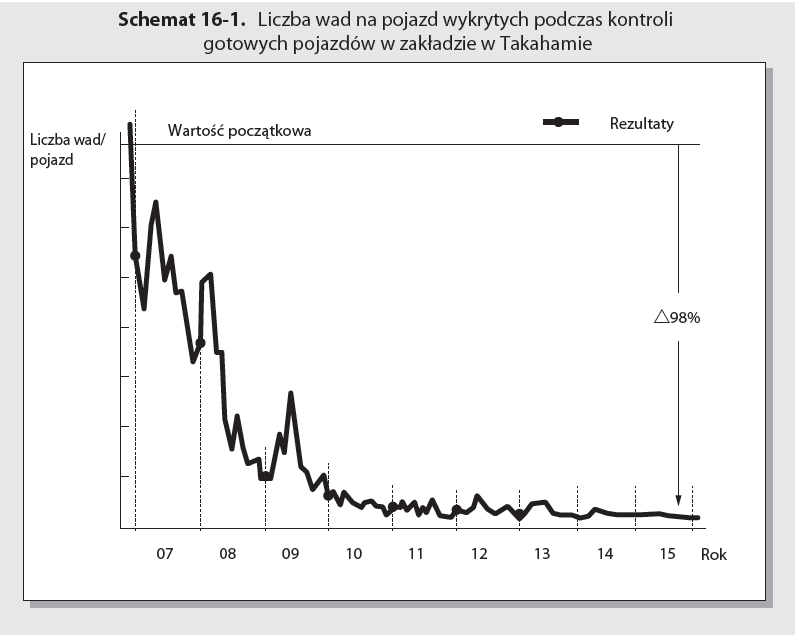
Schemat 16-1. Liczba wad na pojazd wykrytych podczas kontroli gotowych pojazdów w zakładzie w Takahamie
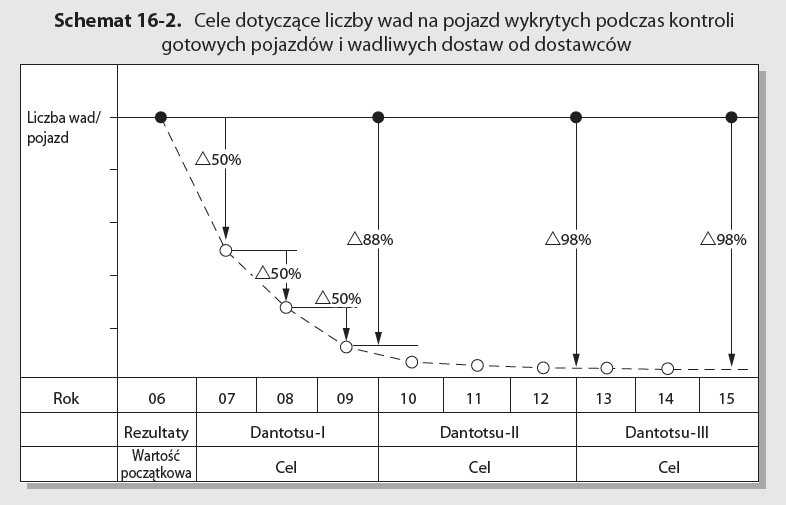
Schemat 16-2. Cele dotyczące liczby wad na pojazd wykrytych podczas kontroli gotowych pojazdów i wadliwych dostaw od dostawców
(2) Liczba wadliwych dostaw od dostawców
Wskaźnik redukcji wad w dostawach do zakładu w Takahamie osiągnął 86%, czyli nieco poniżej docelowego poziomu 98% (schemat 16-3). Mimo że cel nie został jeszcze osiągnięty, zdecydowany spadek liczby wadliwych dostaw doprowadził do znacznej redukcji problemów podczas montażu pojazdów, co umożliwiło płynną pracę linii.
Jednocześnie po stronie dostawców możliwe stało się istotne ograniczenie takich dodatkowych prac, jak ponowna dostawa, naprawa, przegląd pozycji magazynowych, przygotowanie planu/raportu środków zaradczych itp., a zaoszczędzone w ten sposób dodatkowe koszty materiałów, pracy i energii pozwoliły zwiększyć im rentowność.
W Japonii istnieje ścisły związek między zakładami produkującymi pojazdy a dostawcami części, trochę jak w relacji rodzic – dziecko. Dostawcy dobrze wiedzą, że są w stanie stale zmniejszać liczbę wad, stosując się rzetelnie do tego, czego nauczył ich – niczym rodzić – zakład produkujący pojazdy. Natomiast sytuacja jest zgoła inna, jeśli chodzi o zagranicznych dostawców części i zakłady produkujące pojazdy. Tu relacje oparte są na równości i nieczęsto zdarza się, aby zakłady udzielały dostawcom części wskazówek na temat poprawy jakości produktów. Z tego powodu istnieje różnica w przebiegu redukcji wadliwych dostaw między zakładem w Takahamie a zakładami zagranicznymi, co przedstawiono na schemacie 16-4.
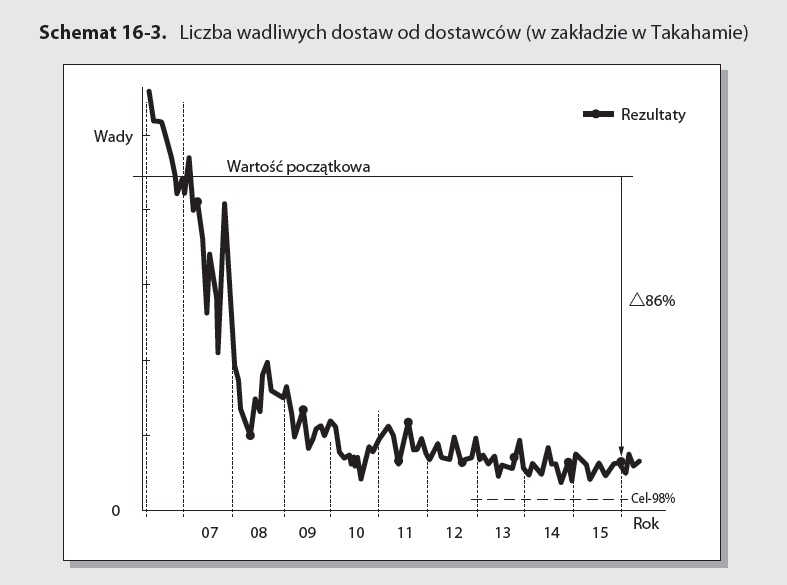
Schemat 16-3. Liczba wadliwych dostaw od dostawców (w zakładzie w Takahamie)

Schemat 16-4. Liczba wadliwych dostaw od dostawców w dwóch zakładach zagranicznych
Poza Japonią powszechną praktyką jest zakup części, jeśli ich jakość jest dobra, a jeśli się pogorszy, kontrakt jest rozwiązywany i części zamawia się u innego dostawcy. W takich miejscach, gdzie zwyczaje różnią się od japońskich, odwiedziłem kilka firm produkcyjnych dostarczających części najgorszej jakości. Towarzyszyli mi członkowie „zespołu wsparcia poprawy jakości dostawców” z naszego działu zapewnienia jakości. Razem zaczęliśmy udzielać im wskazówek na temat wizualizacji, metody 8 kroków itp.
Chociaż przez pierwsze dwa lata efekty były słabo widoczne, ich zainteresowanie działaniami rosło stopniowo, w miarę jak na własne oczy (genchi genbutsu) obserwowali rezultaty (szybki spadek liczby wadliwych pojazdów) w miejscach wykonywania rzeczywistej pracy (zakład produkujący pojazdy). Sprawiło to, że liczba firm prowadzących proaktywne działania na rzecz jakości Dantotsu się zwiększała. Aby jeszcze bardziej wzmocnić ich motywację, najlepszym dostawcom daliśmy możliwość przedstawienia prezentacji na temat ich radykalnego zmniejszenia liczb wad jakościowych podczas corocznych konferencji dostawców. Innymi sposobami wpłynięcia na nich były np. prezentowanie dostawcom rzeczywistych efektów poprawy jakości w naszym zakładzie produkującym pojazdy oraz tworzenie instrukcji tekstowych dotyczących zapewnienia jakości (na podstawie moich notatek), aby nauczyć ich, co i jak powinni robić. W wyniku tych ciągłych wysiłków podejmowanych w Stanach Zjednoczonych i Europie liczba wadliwych dostaw zmniejszyła się w podobny sposób, co widać na obu schematach. Raymond Corporation zdobyła w 2014 roku m.in. Best Plant Award przyznawaną przez amerykański magazyn „Industry Week” i ogłosiła szczegóły swoich działań na rzecz jakości Dantotsu podczas ceremonii wręczenia nagrody, wzbudzając zainteresowanie innych firm i wywołując w nich chęć skorzystania z naszych wskazówek. Dzięki temu udało się zmniejszyć liczbę wadliwych dostaw o 88%. Był to owoc moich szczerych i wytrwałych wysiłków poświęconych działaniom na rzecz jakości Dantotsu przez minione dziewięć lat.
(3) Cel redukcji roszczeń reklamacyjnych z rynku i jego osiągnięcie
Jako punkt odniesienia (100%) wykorzystaliśmy dane dotyczące kosztów roszczeń reklamacyjnych z rynku oraz ich całkowitą sumę z 2006 roku i wyznaczyliśmy cel zmniejszenia jej o połowę co trzy lata. Następnie zachęciliśmy każdy zakład do przeprowadzenia działań od Dantotsu-I do Dantotsu-III, tak aby uzyskać redukcję na poziomie 88%.
W rezultacie, jak widać na schemacie 16-5, firma „F” osiągnęła cel redukcji na poziomie 93%, co uważano za nieosiągalne. Następnie firmy „D” i „E” zbliżyły się do poziomów odpowiednio 78% i 80% redukcji.
Jeśli chodzi o całą grupę, udało nam się zmniejszyć łączną kwotę wypłat z tytułu roszczeń reklamacyjnych z rynku o 65%. Szczególnie duży wkład w ten wynik miały spotkania asaichi poświęcone roszczeniom, zainicjowane w 2011 roku. Podczas tych spotkań skutecznie prowadzono m.in. następujące działania: sprawdzanie przez wszystkie właściwe osoby – codziennie rano – reklamowanych części zwracanych przez dealerów, ustalanie osoby odpowiedzialnej za środki zaradcze oraz ich szybkie wdrażanie. Ponadto korzystne zmiany przyniosły także nowe inicjatywy, takie jak działania w celu redukcji zanieczyszczeń (z udziałem dostawców) oraz cotygodniowe spotkania przeglądowe dotyczące kwestii związanych z projektowaniem (części/podzespołów/wyrobów).
Działania opisane w rozdziale 14, mające zapobiegać wydostawaniu się wad na rynek dzięki poprawie jakości projektowania i metod przygotowania produkcji, dopiero się rozpoczęły, ale jestem przekonany, że entuzjastyczne wysiłki w każdej z firm prędzej czy później przyniosą efekty. We wszystkich tych organizacjach powstają indywidualne instrukcje SE dla poszczególnych obszarów, na każdym etapie projektowania, prototypu i produkcji prowadzi się kontrolę jakości przy użyciu list kontrolnych SE, a różnego rodzaju problemy są rozwiązywane w „najlepszym” (etap projektowania) lub „lepszym” (etap prototypu lub przygotowania produkcji) czasie. Jeśli pracownicy będą zdolni do skutecznego rozwiązywania problemów, redukcja kosztów roszczeń reklamacyjnych z rynku na poziomie 90% nie będzie już tylko marzeniem.
Działania na rzecz jakości Dantotsu pozwoliły uzyskać 65-procentowe oszczędności kosztów, jeśli chodzi o roszczenia reklamacyjne z rynku, dzięki czemu usunięto dużą część strat finansowych, a to z kolei przyczyniło się w istotny sposób do poprawy rentowności całej grupy. Ponadto zmniejszenie liczby wad przedostających się na rynek zwiększyło poziom zadowolenia klientów, co doprowadziło do zwiększenia naszego w nim udziału.
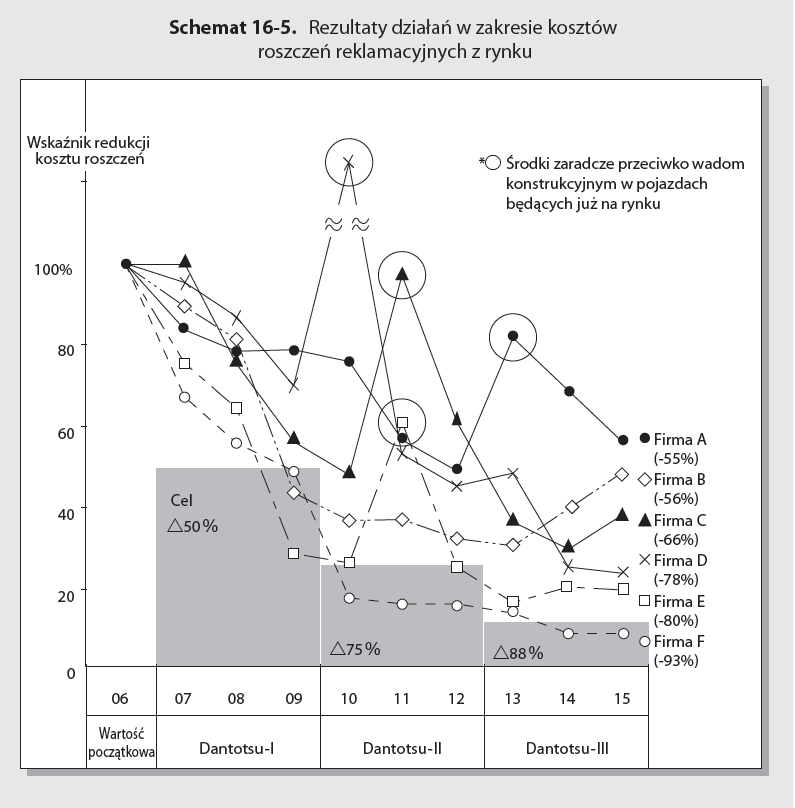
Schemat 16-5. Rezultaty działań w zakresie kosztów roszczeń reklamacyjnych z rynku
2. Ważne wskazówki w działaniach na rzecz jakości Dantotsu
Poniżej przedstawiam wskazówki niezbędne w poprawie jakości, których wielokrotnie udzielałem firmom w ramach działań na rzecz jakości Dantotsu. Jestem przekonany, że te pomysły i zabiegi miały wielką wagę dla działań we wszystkich krajach i dla uzyskania korzystnych rezultatów (schemat 16-6).
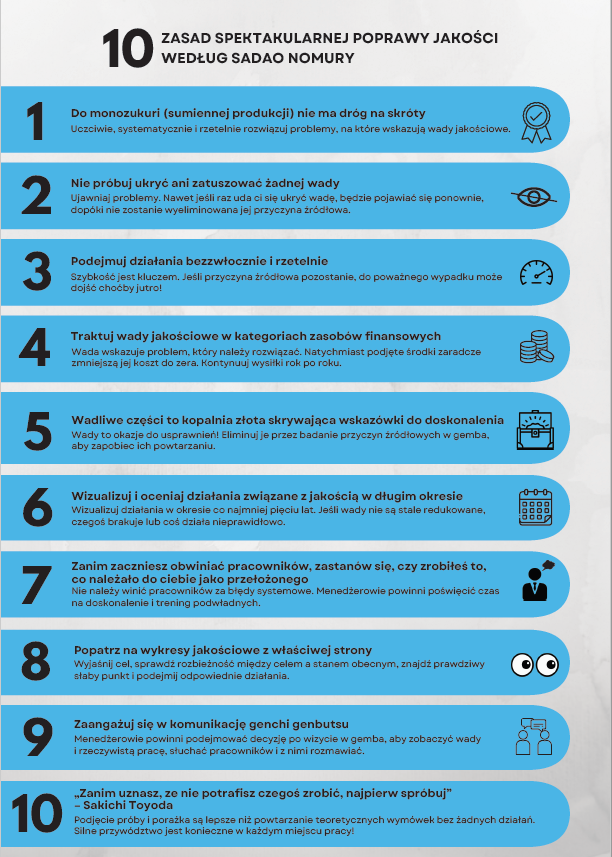
Schemat 16-6. 10 wskazówek w działaniach na rzecz jakości Dantotsu
3. Pomysły i działania zmierzające do uzyskania korzystnych rezultatów
Wysiłki całej firmy muszą prowadzić do satysfakcjonujących rezultatów. Jako doradca ds. jakości opisuję niektóre z pomysłów, które stały się swoistą siłą napędową działań na rzecz jakości Dantotsu i właśnie takie rezultaty przyniosły.
(1) Pobudzanie motywacji poprzez rywalizację w zakresie poprawy jakości między zakładami w różnych krajach
Ustandaryzowaliśmy cele jakościowe i wskaźniki jakościowe dla sześciu zakładów należących do Oddziału Pojazdów Przemysłowych, aby umożliwić uczciwe porównanie, i skłoniliśmy je do wzajemnej rywalizacji w zakresie poprawy jakości (schemat 16-7). Dzięki temu wszyscy pracownicy wiedzieli, czy jakość w zakładzie jest lepsza czy gorsza od innych, co wywołało ich entuzjazm do własnych działań w celu poprawy jakości. Wszyscy bowiem chcieli zdobyć pierwsze miejsce. Kolejną zmianą było usprawnienie komunikacji i zacieśnienie relacji między zakładami. Wcześniej ich pracownicy rzadko się odwiedzali. Po rozpoczęciu działań na rzecz jakości Dantotsu, gdy usłyszano, że jakiś zakład wdraża skuteczne rozwiązania, szybko wybierano się tam z wizytą, aby dowiedzieć się czegoś pożytecznego.
Początkowo działania związane z jakością Dantotsu w zakładzie w Takahamie nie były zbyt intensywne. Wynikało to z przekonania tamtejszych pracowników, że pod względem jakości ich zakład jest znacznie lepszy od fabryk za granicą. Niemniej niecały rok później, odwiedziwszy kilka zagranicznych zakładów, dyrektor Takahamy stwierdził krótko: „Przegrywamy z nimi”. Odtąd zaczęli poważniej pracować nad poprawą jakości. Najlepszym sposobem, by zmotywować nastawioną mało entuzjastycznie załogę danego zakładu jest pokazanie jej wyników osiąganych przez lepsze zakłady.
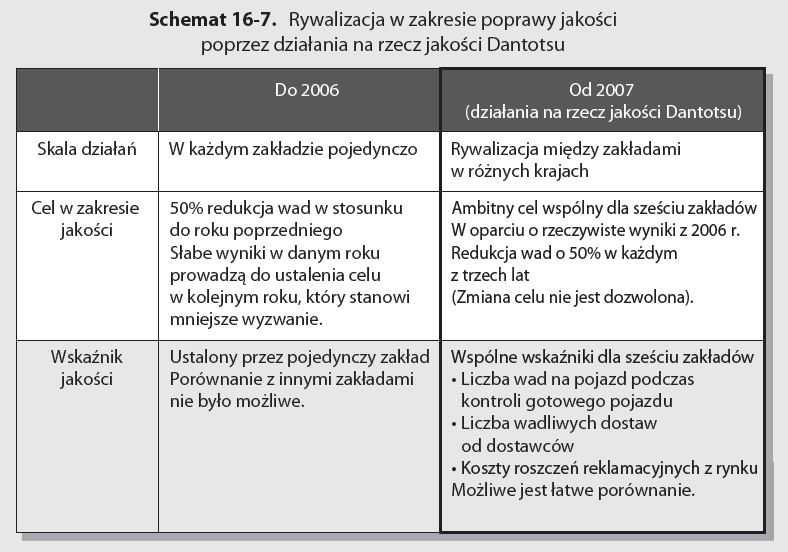
Schemat 16-7. Rywalizacja w zakresie poprawy jakości poprzez działania na rzecz jakości Dantotsu
(2) Ustalenie kolejności kroków doskonalenia jakości i tworzenie instrukcji tekstowych
Na podstawie wiedzy zgromadzonej podczas działań związanych z poprawą jakości w zakładach Toyota Motor Corporation: w zakładzie Motomachi, w Toyota Australia i Toyota South Africa ustaliłem priorytety wśród działań na rzecz jakości Dantotsu i ręcznie zapisałem każdą pozycję na kartce formatu A3. Każdorazowo, kiedy odwiedzałem zagraniczne zakłady (raz na cztery miesiące), wyjaśniałem wszystkie te teksty i instruowałem pracowników, co mają robić na ich podstawie. Działania były prowadzone w następującej kolejności: wizualizacja (rozdział 2), metoda 8 kroków (rozdział 3), standaryzacja (rozdziały 4, 5 i 6), edukacja i trening (rozdział 7) oraz zarządzanie słabymi punktami (rozdział 8). Jeśli chodzi o te kwestie, których trudno nauczyć tylko za pomocą tekstu i wskazówek w miejscu pracy, wyjaśnialiśmy je na rzeczywistych przykładach podczas szkolenia z TPS w Japonii. Pozwalało to pracownikom dogłębnie je zrozumieć.
Bardzo ważne jest, aby krok po kroku podnosić poziom szkolenia. Dołączam do niniejszej książki, na końcu tego rozdziału, swoje odręczne notatki nr 124 i 220, dotyczące metody 8 kroków. Chciałbym, aby czytelnicy poczuli energię i zapał, które towarzyszyły mi podczas ich tworzenia.
(3) Staranne wdrożenie działań następczych
Odwiedzałem każdy zakład co cztery miesiące i sprawdzałem postępy w realizacji tego, czego nauczyłem ich załogi poprzez genchi genbutsu. Przez kilka dni po osiem godzin dziennie w każdym zakładzie sprawdzałem stan aktualny i w danym miejscu wskazywałem, czego brakuje lub gdzie popełnia się błędy. Następnie, z wykorzystaniem notatek w formacie A3, uczyłem ludzi kolejnych kroków. Po powrocie do hotelu musiałem podsumować problemy znalezione tego dnia, zastanowić się nad środkami zaradczymi, a następnie na kartce A3 zapisać po angielsku kolejne wyzwania. Kartka ta stanowiła dla nich kolejne zadanie. Aby stworzyć tekst o takiej objętości, długo zastanawiałem się, jak sformułować myśli, jakie wykorzystać fotografie i jakich użyć tabel, by łatwo było wszystko zrozumieć. W rezultacie brakowało mi czasu na porządny sen. Ale taka była moja praca. W ostatnim dniu wizyty przekazywałem im kopię swojej notatki (arkusza tekstu), wyjaśniałem szczegóły i potwierdzałem, co muszą zrobić. Następnie wracałem do Japonii.
Wizualizując zobowiązania złożone przez pracowników na piśmie (notatka z zadaniami domowymi) oraz wdrażając rzetelnie działania następcze, do pracy nad poprawą jakości można zmotywować pracowników nawet w tych zakładach, w których są oni nastawieni mniej entuzjastycznie.
![]() Zobacz folder książki | Książka Droga Toyoty do doskonałej jakości ukazała się nakładem Wydawnictwa Lean Enterprise Institute Polska i jest dostępna w księgarni leanbooks.pl. Książka jest objęta patronatem Toyota Material Handling Polska. |
Technologie wspierające Lean
PARTNERZY SEKCJI:
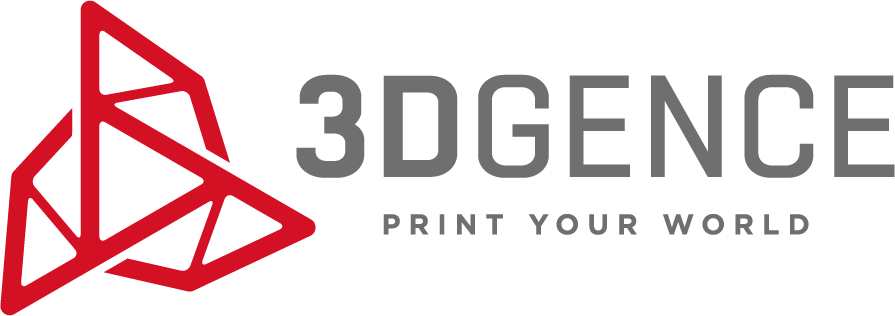
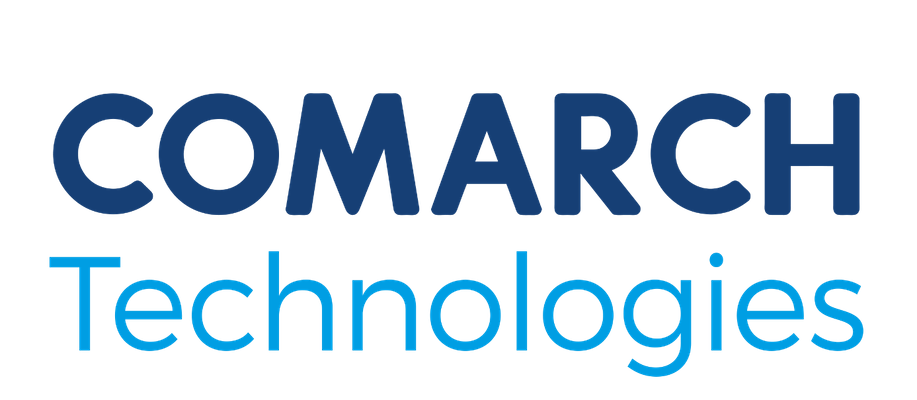
Śledź nas w social media
Aktualności
Ogólnopolski Kongres Jakościowy 2025: Wiedza. Relacje. Biznes.
Nowoczesne podejście do doskonalenia procesów - relacja z IX Europejskiego Kongresu Lean
PolecamyW dniach 14-16 maja 2025 roku w Centrum Edukacyjno-Kongresowym Politechniki Śląskiej odbędzie się Ogólnopolski Kongres Jakościowy 2025. To największe wydarzenie w Polsce poświęcone jakości, łączące wiedzę, relacje i biznes. Kongres stanowi unikalną o ...
Dziewiąta edycja Europejskiego Kongresu Lean przyniosła uczestnikom ogromną dawkę wiedzy na temat wdrażania efektywnych procesów i innowacji w różnych branżach. Organizatorzy podkreślali, że kluczowym przesłaniem wydarzenia jest przekonanie, że to, c ...
Kalendarz konferencji Lean
Patronujemy Wyszukiwarka
Śledź nas na Facebooku