Projekty Lean
Druk 3D oraz Kaizen i Six Sigma w wydziale projektowym

Na każdym etapie powstawania naszego produktu istotną rolę ma dział jakości. Jego pracownicy sprawdzają zgodność komponentów z rysunkiem, czy też złożeń na kolejnych etapach produkcji. Istotnym sposobem pomiaru jest maszyna współrzędnościowa – zwana potocznie maszyną 3D. Jest to doskonałe narzędzie pozwalające zmierzyć wiele charakterystyk.
Istotną wadą tej metody pomiarowej jest konieczność napisania programu pomiarowego dla danego komponentu – jest on niezbędnym elementem do wykonania pomiaru. Sam proces pisania programu jest także czasochłonny. W zależności od skomplikowania elementu i ilości charakterystyk konieczne do tego celu jest poświęcenie czasu od godziny aż do ośmiu godzin.
Istotne utrudnienie – brak fizycznej sztuki
W procesie powstawania prototypu nie ma jeszcze gotowej i istniejącej sztuki, na której można napisać program i kontrolować ustawienia narzędzi do spawania. Podczas wprowadzania nowego produktu, kontroli wymaga nie tylko on, ale zwłaszcza narzędzie, które ma pozwolić na jego zespawanie, tak by był on nie tylko funkcjonalny, ale spełniał wymagania zawarte na rysunku.
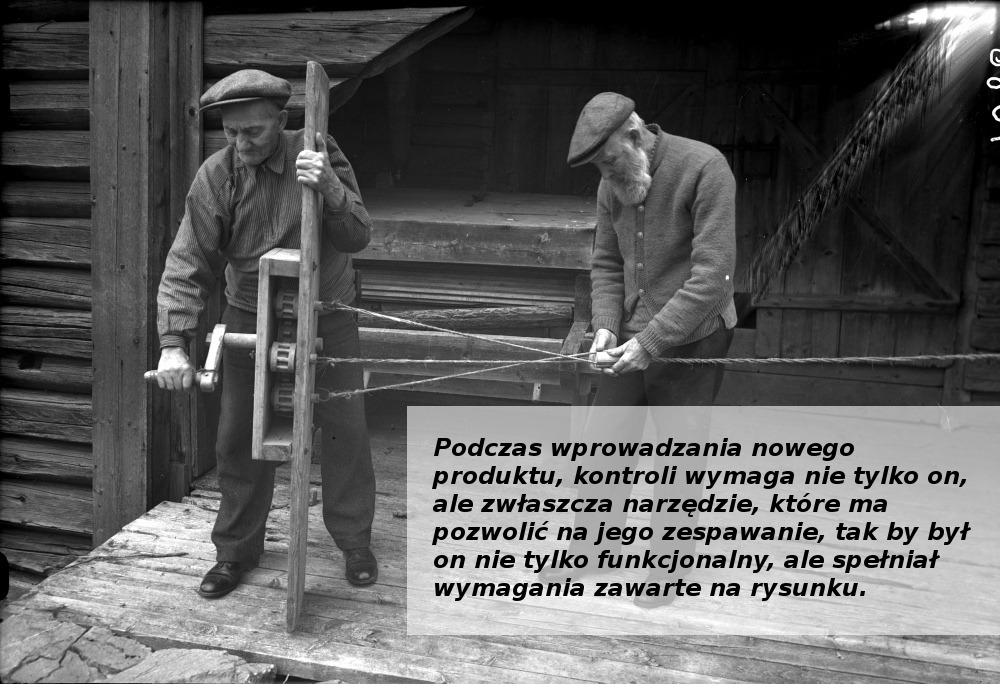
Proces powstawania programu do pomiarów jak i narzędzia spawalniczego możemy zatem podzielić na etapy:
1. Rura plus pierwszy komponent zespawane na wstępnym narzędziu.
2. Pisanie programu dla istniejącej sztuki – wynik pomiarowy.
3. Jeśli wynik jest dobry, przejście do komponentu B, jeśli nie - modyfikacja narzędzia i ponowne zespawanie kolejnego zestawu z komponentem A.
4. Ewentualna modyfikacja programu pomiarowego – wynik pomiarowy.
Jak widać proces ten może być bardzo czasochłonny przez co ustawienie narzędzia spawalniczego, które osobno musi być ustawione dla sztuk lewych i prawych, a także pisanie programu zajmuje nawet do 15 dni roboczych. Poprzez wady jakościowe na etapie projektowania oraz oczekiwanie na wykonanie stalowych elementów i konieczne kolejne kontrole, czas ten mocno się wydłuża.
Analiza procesu
Podczas analizy procesu powstawania narzędzia spawalniczego okazało się, że czas potrzebny do jego powstania wynosi aż 1097 godzin, z czego większość tego czasu to czekanie. Czas czynności dodających wartość, czyli tych które prowadzą nas do rozwiązania to 82.4h co stanowi 7.51% całego czasu.
Ilość tego czasu wynika z faktu, że narzędzie to powstaje w sposób manualny, wykorzystując doświadczenie operatora oraz takie narzędzia pomiarowe jak suwmiarki i wysokościomierze.
Idealnym rozwiązaniem byłoby przeniesienie procesu powstawania narzędzia spawalniczego i programu pomiarowego na maszynie współrzędnościowej podczas produkcji komponentów potrzebnych do wyprodukowania kolejnych sztuk. Jednakże, aby napisać program potrzebna jest fizyczna gotowa sztuka, która to zostałaby zespawana na nowym narzędziu spawalniczym. Naprzeciw problemowi braku fizycznej sztuki przychodzi nam druk 3D.
Mapa pozostałych procesów
Mapa procesu zamawiania i sprawdzania nowego, nigdy wcześniej nie używanego komponentu pokazała, że proces ten jest długotrwały i zajmuje 1518 godzin. Z czego wartości dodanej jest zaledwie 5.8 godziny.
Największym problemem jest brak informacji między działami o konieczności zaprojektowania i zamówienia przyrządu potrzebnego do zamontowania komponentu na maszynie współrzędnościowej. Podobnie jak w przypadku procesu powstawania narzędzia do spawania, przyspieszyć ten proces może zastosowanie druku 3D, oraz zmiana dotychczasowego procesu zamawiania narzędzi do maszyny współrzędnościowej. Po przeprowadzonej analizie kosztów zdecydowano się na zakup drukarki 3D.
Skomplikowany proces druku 3D
Proces druku okazał się dosyć skomplikowany, ze względu na mnogość parametrów możliwych do ustawienia, które to wpływały na czas druku oraz jego wytrzymałość. W związku z tym podjęto decyzję aby zaprojektować eksperyment, który ma nam dać odpowiedź jaki czas druku jest potrzebny, aby uzyskać wydruk o zadanej wytrzymałości w możliwie jak najkrótszym czasie. W obliczeniach zastosowano Design of Experiment, dzięki temu dowiedzieliśmy się, w jakiej kolejności zmieniać poszczególne parametry.
Czas i wytrzymałość druku
Przystąpiliśmy więc do analizy Pareto czynników wpływających na czas druku, która pokazała, że największy wpływ ma wysokość warstwy oraz procent wypełnienia modelu. Następnie połączenie tych dwóch parametrów oraz prędkość druku. Wyniki te nie dziwią i wnioski takie można było wyciągnąć analizując zgromadzone dane.
Podobną analizę wykonano dla czynników wpływających na wytrzymałość wydruku. Tu największy wpływ na wytrzymałość wydruku ma wypełnienie, następnie wysokość warstwy. Prędkość wydruku oraz rozmiar dyszy mają marginalny wpływ na jego wytrzymałość.
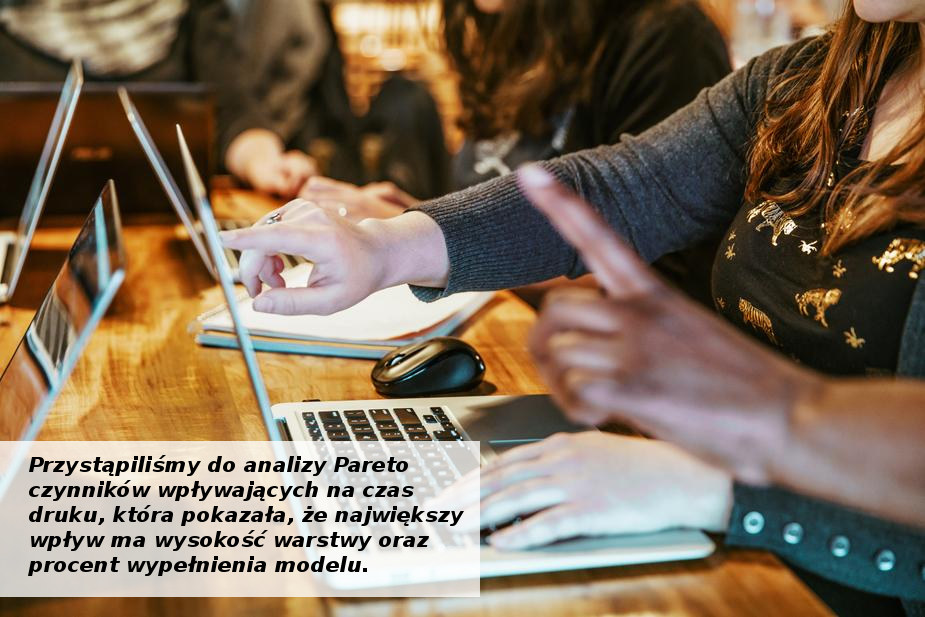
Wykres zależności pokazały korelację pomiędzy wysokością warstwy, a wypełnieniem wpływający na wytrzymałość wydruku oraz pomiędzy wysokością warstwy, a wypełnieniem - wpływający na czas druku. Otrzymaliśmy informację, o parametrach, które dadzą nam prototyp wymaganej wytrzymałości w najkrótszym czasie.
Wszystkie dotychczasowe testy i obliczenia pozwolą nam na zoptymalizowanie procesu druku 3D jeszcze przed jego użyciem do zmiany obecnego stanu i sposobu produkowania prototypów.
Start – pierwszy wydruk 3D
Jednym z pierwszych druków był przyrząd kontrolujący wymiary prototypu. Czas wydruku przyrządu kontrolnego to 154 minuty. Wydrukowanie modelu produktu wraz ze wszystkimi komponentami zajęło około 72 godzin.
Wydrukowano także komponenty, które nie tylko posłużyły do napisania programu pomiarowego, ale zostały także przekazane do dostawcy celem ich produkcji. Przekazanie fizycznych modeli dostawcy przyspieszyło oraz poprawiło proces powstania tego komponentu. Czas oczekiwania na zamówione komponenty zmalał z pierwotnych czterech tygodni do dwóch, czyli o połowę.
Nie tylko w dziale projektowania
Wraz z kolejnymi wydrukami pojawiło się zainteresowanie działu testów procesem druku 3D. Na ich życzenie został wydrukowany komponent, na którego dostawę mieli czekać około ośmiu tygodni, a bez niego nie mogli rozpocząć przygotowań do zbudowania narzędzia do testów. Dzięki drukarce 3D po około 22 godzinach dostali gotowy komponent, który pozwolił na wcześniejsze przygotowanie narzędzia.
Czas oczekiwania niewykorzystany
Analiza dotychczasowych procesów powstawania narzędzia spawalniczego oraz zamawiania komponentów prototypowych pokazała, że w czasie kiedy komponenty są produkowane, czas oczekiwania na komponenty nie był wykorzystywany w żadnym stopniu mającym na celu skrócenie dotychczasowego czasu powstawania czy to narzędzi spawalniczych czy też uzyskania sposobu na sprawdzenie komponentów. Wykorzystując druk 3D udało się zmienić dotychczasowe podejście.
Proces powstawania narzędzi spawalniczych był dotychczas procesem bardzo długotrwałym, wymagającym wielu korekt i powtórzeń. Proces ten wydłużony był dodatkowo przez czas konieczny do napisania programu, który to był pisany jako kolejny krok a nie zrównoleglony. Wprowadzenie druku 3D pozwoliło na wstępne przygotowanie narzędzia spawalniczego oraz napisanie programu pomiarowego jeszcze przed dostawą komponentów.
O ile skrócono proces
Dzięki takiemu działaniu skrócono czas potrzebny do wykonania narzędzia o prawie 61 godzin, a czas czynności dodających wartość spadł o 57.1 godziny. Spadek ten wynika z faktu mniejszej liczby korekt i poprawek narzędzia spawalniczego. Zdecydowano także, aby wydrukować tylko jedną sztukę produktu, gdyż czas potrzebny na jego wydrukowanie wyniósł 72 godziny, a czas pisania programu 8 godzin, więc niemożliwym byłoby przekazanie kolejnej wydrukowanej sztuki wcześniej, niż osoba pisząca program skończy go pisać.
W przypadku kontroli komponentów, wraz z etapem zamówienia komponentów zrównoleglono etap projektowania i zamawiania narzędzia potrzebnego na maszynę współrzędnościową oraz następnie wydrukowanie gotowego komponentu i przekazanie go do jakości celem napisania programu pomiarowego.
O trzy tygodnie szybciej
Łączny czas ludzi potrzebny na wykonanie tego zadania zwiększył się nieznacznie poprzez dodanie druku 3D. Zmieniła się natomiast kolejność. Zrównoleglenie procesów pozwoliło na uzyskanie wyniku pomiarowego o 3 tygodnie wcześniej niż przed zmianą, a co za tym idzie zaraz po dotarciu do magazynu komponenty mogły zostać sprawdzone i przekazane dalej.
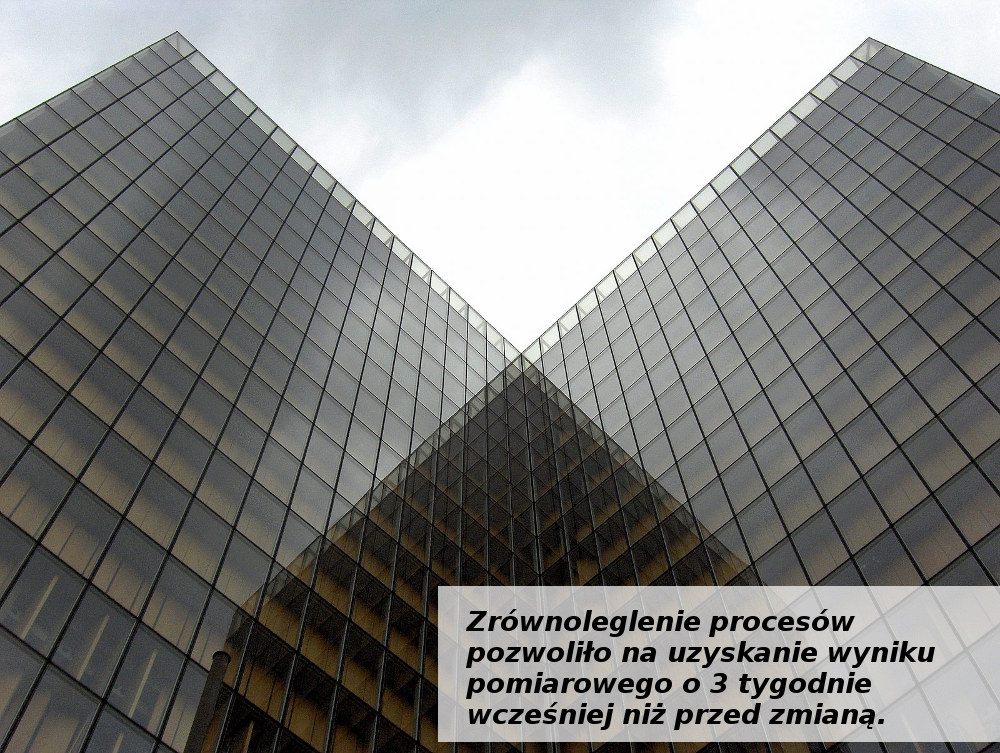
Druk 3D okazał się nieodłącznym elementem wprowadzenia zmian, a jednoczesne zoptymalizowanie pracy drukarki, pozwoliło na maksymalizację wydajności jej czasu poprzez uniknięcie wydrukowania elementu o za małej wytrzymałości, przez co konieczne byłoby ponowne wydrukowanie go na innych parametrach. Pozwoliło ono także na uniknięcie niepotrzebnego czekania na element drukowany, który przez niewiedzę mógłby być drukowany zbyt długo (2,5-krotne przyśpieszenie czasu druku). Badanie właściwości parametrów drukarki na wytrzymałość pokazało także, które ze sterowalnych parametrów ma największy wpływ na rezultat.
Zobacz także: Więcej projektów Lean z firm produkcyjnych i usługowych
Wszystkie zmiany, które wprowadzono spotkały się z aprobatą przełożonych i współpracowników. Wprowadzenie zmiany w procesie sprawdzania komponentów i powstawania narzędzi spawalniczych było konieczne jeśli zakład produkcyjny chciał zwiększyć swoje możliwości przerobowe. Dzięki tym zmianom zwiększyła się możliwość przyjmowania kolejnych zleceń na budowy prototypowe oraz zmniejszenie kosztów związanych z pracą ludzi.
Technologie wspierające Lean
PARTNERZY SEKCJI:
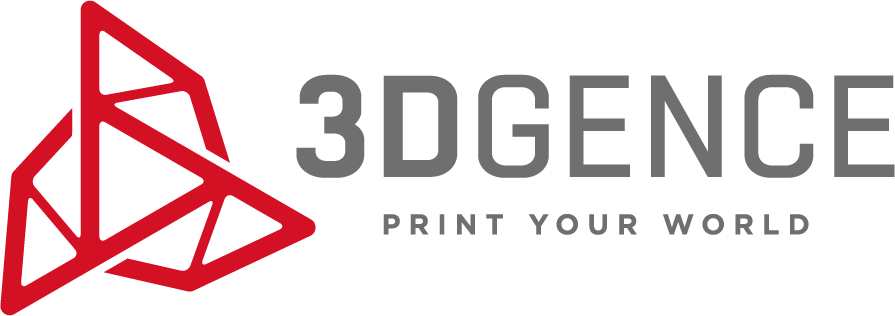
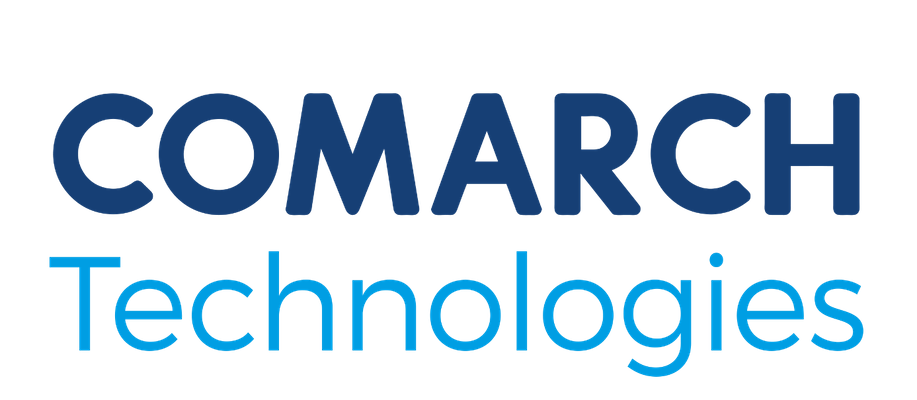
W dniach 14-16 maja 2025 roku w Centrum Edukacyjno-Kongresowym Politechniki Śląskiej odbędzie się Ogólnopolski Kongres Jakościowy 2025. To największe wydarzenie w Polsce poświęcone jakości, łączące wiedzę, relacje i biznes. Kongres stanowi unikalną o ...
Dziewiąta edycja Europejskiego Kongresu Lean przyniosła uczestnikom ogromną dawkę wiedzy na temat wdrażania efektywnych procesów i innowacji w różnych branżach. Organizatorzy podkreślali, że kluczowym przesłaniem wydarzenia jest przekonanie, że to, c ...
PON | WT | ŚR | CZW | PT | SOB | NDZ |
---|---|---|---|---|---|---|
26 | 27 | 28 | 29 | 30 | 31 | 1 |
2 | 3 | 4 | 5 | 6 | 7 | 8 |
9 | 10 | 11 | 12 | 13 | 14 | 15 |
16 | 17 | 18 | 19 | 20 | 21 | 22 |
23 | 24 | 25 | 26 | 27 | 28 | 29 |
30 | 1 | 2 | 3 | 4 | 5 | 6 |
- 08.07.2025 Otwarte szkolenie Lean Koromo
- 06.08.2025 Szkolenie Lean z grą Koromo w firmie Scanfil