Projekty Lean
Transformacja Lean z trwałymi rezultatami w branży FMCG – Case Study

W niniejszym tekście przedstawiamy studium przypadku transformacji strategicznej Lean w dużej grupie kapitałowej zajmującej się produkcją FMCG, która zatrudnia 3000 pracowników w czterech zakładach produkcyjnych w Polsce. Całość transformacji została przeprowadzona przez firmę Leanpassion.
Dane firmy objętej zmianami zostały zanonimizowane ze względu na poufność, jednak mimo to mamy nadzieję, że lektura tego studium przypadku będzie wartościową lekcją na temat strategicznego podejścia do Lean.
Sytuacja Biznesowa
Tuż przed transformacją, w 2015 roku, Grupa opracowała nową misję i wizję. Z jednej strony wieńczyło to długą drogę konsolidacji. Z drugiej strony otwierało Grupę na nowe perspektywy. W strategii firmy jako główne filary zaplanowano koncentrację na klientach i dostawcach, ale także operacyjną doskonałość i efektywność kosztową. Po upewnieniu się z zarządem co do wspólnego zrozumienia i konsensusu zarządu odnośnie kontekstu biznesowego (Misja, Wizja, Cele strategiczne i Wartości) można było przejść do kolejnego kroku. Wyzwaniem okazała się konieczność wypracowania z pracownikami kierunku oraz przyjrzenia się wewnętrznym procesom finalnie budując warunki do doskonalenia.
Czy na pewno Strategia Lean?
Organizacje z wpływowym akcjonariatem w postaci funduszu inwestycyjnego, rzadko decydują się na mozolne, długotrwałe zmiany, uwzględniające także rozwój zasobów ludzkich. Raczej idą w kierunku szybkiego wzrostu wartości kapitału. Częściej poprzez restrukturyzacje niż strategiczne podejście z wykorzystaniem metodologii Lean. Ale ta firma zdążyła już przejść restrukturyzację. Co więc dalej?
Założenia Transformacji
Przygotowując transformację, starano się nie zapominać o celach powiązanych z rachunkiem zysków i strat. Założono wzrost produktywności o 25%, jednak nie poprzez proste zwolnienia czy cięcia płac. W 2015 roku rynek pracy powoli przechylał się ku niedoborom pracowników. Przedsiębiorstwo zaczęło sięgać po pracowników tymczasowych z Ukrainy. Wzrost wydajności mógł wiec dokonać się tylko poprzez wyeliminowanie marnotrawstwa z procesów.
Drugim założeniem była trwałość transformacji. Zakładaliśmy osiągnięcie jej poprzez realizowanie celów rękami grupy pracowników oraz włączenie w proces doskonalenia wszystkich zatrudnionych w jednym z Zakładów Produkcyjnych. Wybrano jeden z czterech funkcjonujących zakładów jako miejsce pierwszego etapu transformacji, zakładając, że wyszkoleni wewnętrzni liderzy zmian, będą w stanie nie tylko utrzymać je, ale także poprowadzić dalej zarówno w czasie, jak i w kolejnych zakładach.
Mając uzgodniony kierunek, wybraliśmy ok. 20 członków grupy przygotowywanej do roli liderów transformacji. Zostali dobrani tak, aby reprezentowali różne szczeble, różne działy i różnorodne predyspozycje. Szybko okazało się, że Miłosz i Artur to talenty analityczne, Ania to solidna, pracowita „mrówa”, która zadba o szczegóły; Magda jest świetnie zorganizowana, a Kamil ma „gadane” i łatwość nawiązywania relacji. Mieliśmy też McGyver’a z Utrzymania Ruchu. W swojej historii Paweł w 2 dni zaprojektował i skonstruował „wiatraczek”, który tak sprytnie przerzucał produkty pomiędzy transportami, że można było oszczędzić bezsensownej roboty 2 operatorom. Kilka osób z grupy, niestety szybko się wykruszyło, ale pozostała wytrwała 12, w tym niektórzy brygadziści z samego Gemba, zaskoczyła nas wielką determinacją.
Zanim jednak doszło do usprawnień – przygotowaliśmy do nadchodzących wydarzeń załogę. Ponad 100 pracowników objęto treningami i warsztatami Lean. Oprócz dostarczenia praktycznej wiedzy i umiejętności były one okazją do uspokajającej komunikacji. W firmach, które przeszły restrukturyzację związaną ze zwolnieniami grupowymi, każda zmiana kojarzy się z najgorszym. Wskutek sytuacji na rynku pracy, wzrosło też obciążenie pracowników, a więc nastroje nie były najlepsze. Na szczęście, zgodnie z idealnymi założeniami Lean mogliśmy pozwolić sobie na „0” zwolnień; powiedzieć o tym pracownikom i zaprosić ich do udziału w zmianach. Zapowiedzieliśmy też stopniowe zmniejszanie obciążenia. Uzyskane roboczogodziny w lwiej części miały wpłynąć na rachunek wyników, ale w miarę możliwości także odciążyć ludzi.
W fazie przygotowawczej ogłosiliśmy konkurs z nagrodami — Sherlock Waste – kto z pracowników odnajdzie najwięcej marnotrawstw. Udział w konkursie był dla wielu z nich pierwszym pozytywnym doświadczeniem związanym ze zmianami w firmie, usprawniło komunikację, dając poczucie wpływu na swoje otoczenie i miejsce pracy.
Konsensus
Analiza Stanu Obecnego w pigułce: około 30 dni analitycznych. Rezultatem było 8 map procesów; 69 badań migawkowych lub pomiarów cyklów na stanowiskach pracy i ponad 150 pomysłów na usprawnienia i wzrost produktywności. Każdy badany proces został oceniony pod kątem potencjału oszczędności i korzyści wyrażonych w czasie i w pieniądzach. Unikaliśmy inwestycji, skupiając się na rozwiązaniach nisko kosztowych. Każdy ze zbadanych procesów miał lidera, mapę stanu przyszłego, harmonogram usprawnień i osoby odpowiedzialne za wdrażanie usprawnień.
My Lean Journey i „czarna dziura”
Równolegle do realizacji harmonogramu rozpoczęto budowę podstaw kulturowych Strategii Lean. Podobnie jak w wielu transformacjach, przyszła pora na prace z liderami, a konkretnie budowę ich pracy - standardów przywództwa. Zarządzanie Wizualne. Cel – świadomość i zaangażowanie. Skaskadowano cele. Przy każdym stanowisku wywieszono tablice „godzina po godzinie”. Pierwsze dni to wpisy liderów, ale zadziwiająco łatwo udało się namówić pracowników na cogodzinne wpisywanie wyników i na czerwono — przyczyn braku wyniku. Wraz z tym powiesiliśmy pierwsze tablice codziennych odpraw. Na początek dla dwóch głównych procesów: Pojawiły się pierwsze wpisy problemów i próby dociekania przyczyn…
No i nadszedł moment spotykany w większości transformacji: „czarna dziura”. Był styczeń 2016. Spora absencja chorobowa; odejścia stałych pracowników; liderzy zajęci zadaniami transformacji; ukraińscy pracownicy tymczasowi zmieniali się jak w kalejdoskopie, wprowadzając chaos. Wzrost produktywności stanął w miejscu. Kiedy szliśmy na produkcję, ścigały nas zmęczone, niechętne spojrzenia. Spotkania przy tablicach wyglądały jak wiece niezadowolonych. Wszak, zamiast zmniejszyć obciążenie pracą, w tej sytuacji zwiększono je. Łatwo sobie tłumaczyć, że to faza oporu w zarządzaniu zmianą; trudniej taką fazą „zarządzić”. Nawet liderzy transformacji tracili wenę.
Pomógł pomysł na systematyczną, cierpliwą pracę w Gemba. Codziennie inny, wyznaczony Lider z grupy Lean praktykował Gemba Walk monitorując wskaźnik produktywności. Czasem sam, czasem z dyrektorem zakładu, coraz częściej z lokalnym liderem. Sprawdzaliśmy prawidłowość wpisów na tablicach, liczyliśmy obsadę, sprawdzaliśmy realizacje zadań transformacji; prowadziliśmy nieskończone dialogi mentor – uczeń z brygadzistami i pracownikami; konsultanci zewnętrzni dzień po dniu uczestniczyli w odprawach. Wreszcie po kilku tygodniach pojawiło się światełko w tunelu, wyniki ruszyły, ludzie stopniowo uspokajali się.
Stało się jednak jasne, że to tylko zgasiło pożar, a naszym celem było zbudowanie trwałych mechanizmów doskonalenia, w tym właściwych postaw liderów – brygadzistów. Doszliśmy do piątego kroku Strategii Lean – tworzenia Modelu Zarządzania.
Model Zarządzania
Zaplanowano tygodniowe warsztaty Lean Action Workout. 4 zespoły, 40 osób; 5 dni, 19 celów. Zadanie generalne: wypracowania nowych standardów dotyczących pracy Liderów i 3 według wcześniejszych analiz najpotrzebniejszych narzędzi Lean (Problem Solving, SMED w obszarze pakowania; Zarządzanie Wizualne dla procesów wsparcia).
Kluczowa grupa opracowuje nowy Standard Zarządzania dla Kierowników i Liderów. W nowej strukturze lider kieruje dziesięcioma osobami, dawniej nawet pięćdziesięcioma. Szybciej podejmowane są decyzje, nie ma silosów. Opracowano nowe rutyny dla liderów, gdzie jednym z priorytetów stało się stymulowanie procesu identyfikacji i rozwiązywania codziennych problemów przez pracowników. Przeglądnięto przygotowane wcześniej matryce kompetencji i zaplanowano rozwój każdego z pracowników. Daje to większą zastępowalność, pomaga złagodzić skutki sytuacji na rynku pracy.
Zastanawiamy się nad uruchomieniem odpraw także na II i III zmianie. Początkowo wydawało się to niemożliwe, ale już po miesiącu spotkań I zmiany, widzimy na tablicach dopiski i uwagi ze zmiany II, a nawet z „nocki”. Dla Leanowca, nie ma nic przyjemniejszego niż sygnały od ludzi z Gemba, że chcą pracować z problemami. Wystartowanie z oficjalnymi odprawami było już tylko formalnością.
Szybko jednak pojawiają się problemy, których nie sposób rozwiązać podczas 15-minutowych odpraw przy tablicach. Wracają po kilka razy i nie wiadomo co z nimi robić, bo pracujemy wyłącznie z objawami. Jednym z takich problemów są zrywane folie, innym duża ilość odpadów materiałów - w tym cennych składników spadających z linii podczas produkcji. Czas na System Problem Solving, zwany tu ZSA (Zespoły Szybkiej Akcji). Liderzy mogą organizować jedno 20-40 minutowe spotkanie poza odprawą. Jeśli nie daje efektu, trudniejszy problem trafia na spotkanie kierownicze. Tu raz w tygodniu problem może być przydzielony specjalnie przygotowanemu moderatorowi. Ten organizuje grupę roboczą i inicjatywę, prowadzącą do wygenerowania rozwiązań i pomaga liderowi w eksperymentach i standaryzacji.
Chwila celebracji
Dodatkowo można pochwalić się wynikami: produktywność wzrosła o ponad 25%; OEE na procesie produkcji jednego z ważniejszych produktów wzrósł do 62%; przezbrojenia skrócone o 50-80%; pokrycie matrycy kompetencji z 24 do ponad 72%; wspólne cele i raportowanie 100% - 276 osób załogi. Liderzy przeprowadzili 76 eksperymentów w cyklu PDCA; także tych, które wynikały z trudniejszych problemów.
To była dobra transformacja. Była? Jest. Wiemy przecież, że stawanie się Lean nigdy nie ma końca.
Sytuacja Biznesowa
Tuż przed transformacją, w 2015 roku, Grupa opracowała nową misję i wizję. Z jednej strony wieńczyło to długą drogę konsolidacji. Z drugiej strony otwierało Grupę na nowe perspektywy. W strategii firmy jako główne filary zaplanowano koncentrację na klientach i dostawcach, ale także operacyjną doskonałość i efektywność kosztową. Po upewnieniu się z zarządem co do wspólnego zrozumienia i konsensusu zarządu odnośnie kontekstu biznesowego (Misja, Wizja, Cele strategiczne i Wartości) można było przejść do kolejnego kroku. Wyzwaniem okazała się konieczność wypracowania z pracownikami kierunku oraz przyjrzenia się wewnętrznym procesom finalnie budując warunki do doskonalenia.
Czy na pewno Strategia Lean?
Organizacje z wpływowym akcjonariatem w postaci funduszu inwestycyjnego, rzadko decydują się na mozolne, długotrwałe zmiany, uwzględniające także rozwój zasobów ludzkich. Raczej idą w kierunku szybkiego wzrostu wartości kapitału. Częściej poprzez restrukturyzacje niż strategiczne podejście z wykorzystaniem metodologii Lean. Ale ta firma zdążyła już przejść restrukturyzację. Co więc dalej?
Założenia Transformacji
Przygotowując transformację, starano się nie zapominać o celach powiązanych z rachunkiem zysków i strat. Założono wzrost produktywności o 25%, jednak nie poprzez proste zwolnienia czy cięcia płac. W 2015 roku rynek pracy powoli przechylał się ku niedoborom pracowników. Przedsiębiorstwo zaczęło sięgać po pracowników tymczasowych z Ukrainy. Wzrost wydajności mógł wiec dokonać się tylko poprzez wyeliminowanie marnotrawstwa z procesów.
Drugim założeniem była trwałość transformacji. Zakładaliśmy osiągnięcie jej poprzez realizowanie celów rękami grupy pracowników oraz włączenie w proces doskonalenia wszystkich zatrudnionych w jednym z Zakładów Produkcyjnych. Wybrano jeden z czterech funkcjonujących zakładów jako miejsce pierwszego etapu transformacji, zakładając, że wyszkoleni wewnętrzni liderzy zmian, będą w stanie nie tylko utrzymać je, ale także poprowadzić dalej zarówno w czasie, jak i w kolejnych zakładach.
Mając uzgodniony kierunek, wybraliśmy ok. 20 członków grupy przygotowywanej do roli liderów transformacji. Zostali dobrani tak, aby reprezentowali różne szczeble, różne działy i różnorodne predyspozycje. Szybko okazało się, że Miłosz i Artur to talenty analityczne, Ania to solidna, pracowita „mrówa”, która zadba o szczegóły; Magda jest świetnie zorganizowana, a Kamil ma „gadane” i łatwość nawiązywania relacji. Mieliśmy też McGyver’a z Utrzymania Ruchu. W swojej historii Paweł w 2 dni zaprojektował i skonstruował „wiatraczek”, który tak sprytnie przerzucał produkty pomiędzy transportami, że można było oszczędzić bezsensownej roboty 2 operatorom. Kilka osób z grupy, niestety szybko się wykruszyło, ale pozostała wytrwała 12, w tym niektórzy brygadziści z samego Gemba, zaskoczyła nas wielką determinacją.
Zanim jednak doszło do usprawnień – przygotowaliśmy do nadchodzących wydarzeń załogę. Ponad 100 pracowników objęto treningami i warsztatami Lean. Oprócz dostarczenia praktycznej wiedzy i umiejętności były one okazją do uspokajającej komunikacji. W firmach, które przeszły restrukturyzację związaną ze zwolnieniami grupowymi, każda zmiana kojarzy się z najgorszym. Wskutek sytuacji na rynku pracy, wzrosło też obciążenie pracowników, a więc nastroje nie były najlepsze. Na szczęście, zgodnie z idealnymi założeniami Lean mogliśmy pozwolić sobie na „0” zwolnień; powiedzieć o tym pracownikom i zaprosić ich do udziału w zmianach. Zapowiedzieliśmy też stopniowe zmniejszanie obciążenia. Uzyskane roboczogodziny w lwiej części miały wpłynąć na rachunek wyników, ale w miarę możliwości także odciążyć ludzi.
W fazie przygotowawczej ogłosiliśmy konkurs z nagrodami — Sherlock Waste – kto z pracowników odnajdzie najwięcej marnotrawstw. Udział w konkursie był dla wielu z nich pierwszym pozytywnym doświadczeniem związanym ze zmianami w firmie, usprawniło komunikację, dając poczucie wpływu na swoje otoczenie i miejsce pracy.
Konsensus
Analiza Stanu Obecnego w pigułce: około 30 dni analitycznych. Rezultatem było 8 map procesów; 69 badań migawkowych lub pomiarów cyklów na stanowiskach pracy i ponad 150 pomysłów na usprawnienia i wzrost produktywności. Każdy badany proces został oceniony pod kątem potencjału oszczędności i korzyści wyrażonych w czasie i w pieniądzach. Unikaliśmy inwestycji, skupiając się na rozwiązaniach nisko kosztowych. Każdy ze zbadanych procesów miał lidera, mapę stanu przyszłego, harmonogram usprawnień i osoby odpowiedzialne za wdrażanie usprawnień.
My Lean Journey i „czarna dziura”
Równolegle do realizacji harmonogramu rozpoczęto budowę podstaw kulturowych Strategii Lean. Podobnie jak w wielu transformacjach, przyszła pora na prace z liderami, a konkretnie budowę ich pracy - standardów przywództwa. Zarządzanie Wizualne. Cel – świadomość i zaangażowanie. Skaskadowano cele. Przy każdym stanowisku wywieszono tablice „godzina po godzinie”. Pierwsze dni to wpisy liderów, ale zadziwiająco łatwo udało się namówić pracowników na cogodzinne wpisywanie wyników i na czerwono — przyczyn braku wyniku. Wraz z tym powiesiliśmy pierwsze tablice codziennych odpraw. Na początek dla dwóch głównych procesów: Pojawiły się pierwsze wpisy problemów i próby dociekania przyczyn…
No i nadszedł moment spotykany w większości transformacji: „czarna dziura”. Był styczeń 2016. Spora absencja chorobowa; odejścia stałych pracowników; liderzy zajęci zadaniami transformacji; ukraińscy pracownicy tymczasowi zmieniali się jak w kalejdoskopie, wprowadzając chaos. Wzrost produktywności stanął w miejscu. Kiedy szliśmy na produkcję, ścigały nas zmęczone, niechętne spojrzenia. Spotkania przy tablicach wyglądały jak wiece niezadowolonych. Wszak, zamiast zmniejszyć obciążenie pracą, w tej sytuacji zwiększono je. Łatwo sobie tłumaczyć, że to faza oporu w zarządzaniu zmianą; trudniej taką fazą „zarządzić”. Nawet liderzy transformacji tracili wenę.
Pomógł pomysł na systematyczną, cierpliwą pracę w Gemba. Codziennie inny, wyznaczony Lider z grupy Lean praktykował Gemba Walk monitorując wskaźnik produktywności. Czasem sam, czasem z dyrektorem zakładu, coraz częściej z lokalnym liderem. Sprawdzaliśmy prawidłowość wpisów na tablicach, liczyliśmy obsadę, sprawdzaliśmy realizacje zadań transformacji; prowadziliśmy nieskończone dialogi mentor – uczeń z brygadzistami i pracownikami; konsultanci zewnętrzni dzień po dniu uczestniczyli w odprawach. Wreszcie po kilku tygodniach pojawiło się światełko w tunelu, wyniki ruszyły, ludzie stopniowo uspokajali się.
Stało się jednak jasne, że to tylko zgasiło pożar, a naszym celem było zbudowanie trwałych mechanizmów doskonalenia, w tym właściwych postaw liderów – brygadzistów. Doszliśmy do piątego kroku Strategii Lean – tworzenia Modelu Zarządzania.
Model Zarządzania
Zaplanowano tygodniowe warsztaty Lean Action Workout. 4 zespoły, 40 osób; 5 dni, 19 celów. Zadanie generalne: wypracowania nowych standardów dotyczących pracy Liderów i 3 według wcześniejszych analiz najpotrzebniejszych narzędzi Lean (Problem Solving, SMED w obszarze pakowania; Zarządzanie Wizualne dla procesów wsparcia).
Kluczowa grupa opracowuje nowy Standard Zarządzania dla Kierowników i Liderów. W nowej strukturze lider kieruje dziesięcioma osobami, dawniej nawet pięćdziesięcioma. Szybciej podejmowane są decyzje, nie ma silosów. Opracowano nowe rutyny dla liderów, gdzie jednym z priorytetów stało się stymulowanie procesu identyfikacji i rozwiązywania codziennych problemów przez pracowników. Przeglądnięto przygotowane wcześniej matryce kompetencji i zaplanowano rozwój każdego z pracowników. Daje to większą zastępowalność, pomaga złagodzić skutki sytuacji na rynku pracy.
Zastanawiamy się nad uruchomieniem odpraw także na II i III zmianie. Początkowo wydawało się to niemożliwe, ale już po miesiącu spotkań I zmiany, widzimy na tablicach dopiski i uwagi ze zmiany II, a nawet z „nocki”. Dla Leanowca, nie ma nic przyjemniejszego niż sygnały od ludzi z Gemba, że chcą pracować z problemami. Wystartowanie z oficjalnymi odprawami było już tylko formalnością.
Szybko jednak pojawiają się problemy, których nie sposób rozwiązać podczas 15-minutowych odpraw przy tablicach. Wracają po kilka razy i nie wiadomo co z nimi robić, bo pracujemy wyłącznie z objawami. Jednym z takich problemów są zrywane folie, innym duża ilość odpadów materiałów - w tym cennych składników spadających z linii podczas produkcji. Czas na System Problem Solving, zwany tu ZSA (Zespoły Szybkiej Akcji). Liderzy mogą organizować jedno 20-40 minutowe spotkanie poza odprawą. Jeśli nie daje efektu, trudniejszy problem trafia na spotkanie kierownicze. Tu raz w tygodniu problem może być przydzielony specjalnie przygotowanemu moderatorowi. Ten organizuje grupę roboczą i inicjatywę, prowadzącą do wygenerowania rozwiązań i pomaga liderowi w eksperymentach i standaryzacji.
Chwila celebracji
Dodatkowo można pochwalić się wynikami: produktywność wzrosła o ponad 25%; OEE na procesie produkcji jednego z ważniejszych produktów wzrósł do 62%; przezbrojenia skrócone o 50-80%; pokrycie matrycy kompetencji z 24 do ponad 72%; wspólne cele i raportowanie 100% - 276 osób załogi. Liderzy przeprowadzili 76 eksperymentów w cyklu PDCA; także tych, które wynikały z trudniejszych problemów.
To była dobra transformacja. Była? Jest. Wiemy przecież, że stawanie się Lean nigdy nie ma końca.
Grażyna Potwora Transformation Expert, Leanpassion Maciej Molczyk Partner, Leanpassion | ![]() |
Technologie wspierające Lean
PARTNERZY SEKCJI:
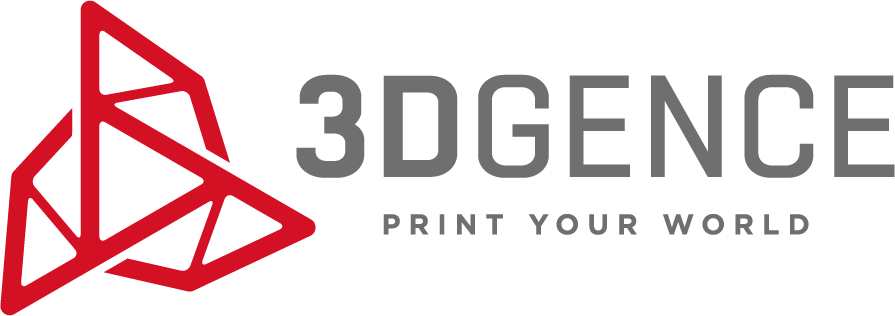
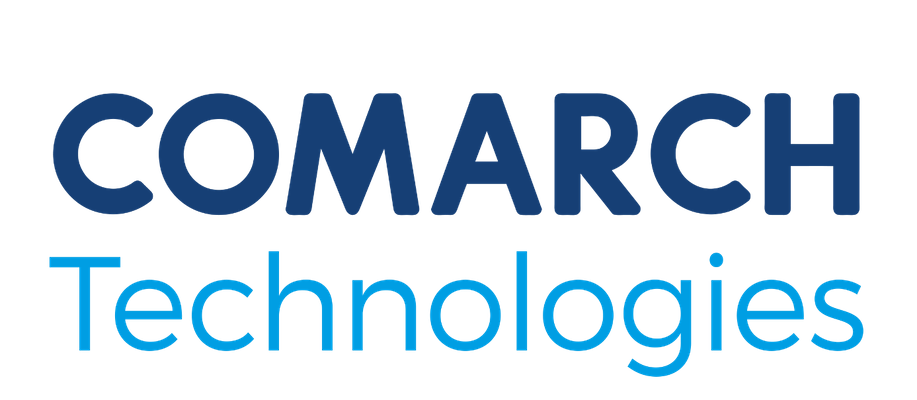
Śledź nas w social media
Aktualności
Ogólnopolski Kongres Jakościowy 2025: Wiedza. Relacje. Biznes.
Nowoczesne podejście do doskonalenia procesów - relacja z IX Europejskiego Kongresu Lean
PolecamyW dniach 14-16 maja 2025 roku w Centrum Edukacyjno-Kongresowym Politechniki Śląskiej odbędzie się Ogólnopolski Kongres Jakościowy 2025. To największe wydarzenie w Polsce poświęcone jakości, łączące wiedzę, relacje i biznes. Kongres stanowi unikalną o ...
Dziewiąta edycja Europejskiego Kongresu Lean przyniosła uczestnikom ogromną dawkę wiedzy na temat wdrażania efektywnych procesów i innowacji w różnych branżach. Organizatorzy podkreślali, że kluczowym przesłaniem wydarzenia jest przekonanie, że to, c ...
Kalendarz konferencji Lean
Najbliższe szkolenia Lean
Patronujemy Wyszukiwarka
Śledź nas na Facebooku