Aktualności Lean
Od potentata do bankruta – relacja z XV Międzynarodowej Konferencji Lean Management
Dodano: 2015-06-19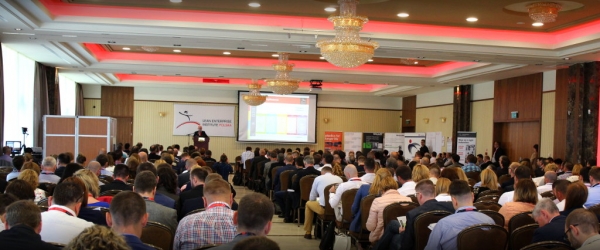
Międzynarodowa Konferencja Lean obchodzi swoje piętnastolecie. Pojawiło się na niej ponad 400 osób, wśród których spotykaliśmy doświadczonych praktyków ciągłego doskonalenia swoich firm, ale i osoby, które przyjechały by dopiero poznać metody Lean i posłuchać osób pracujących z nimi w wielu krajach na całym świecie.
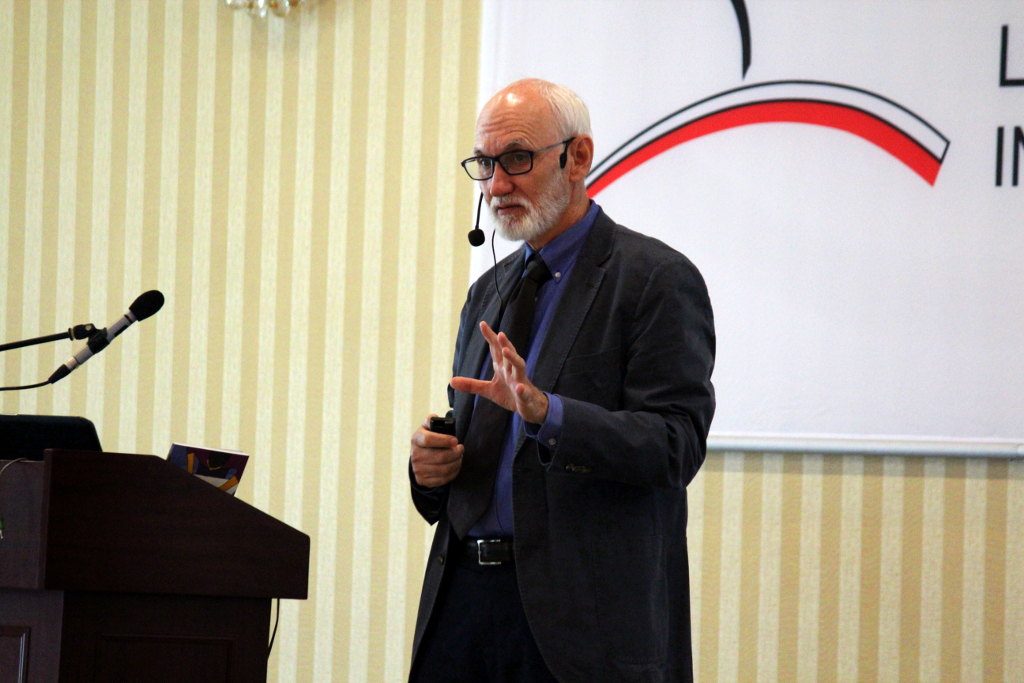
W pierwszym dniu konferencji organizatorzy pokazali umiejętność szybkiego reagowania na problemy. Jeden spóźniony samolot w Los Angeles mógł sprawić, że nie mielibyśmy okazji posłuchać Samuela Obary, który ostatecznie dzięki staraniom organizatorów przybył do Polski i wygłosił w ciągu dwóch dni kilka dynamicznych i zabawnych prelekcji, poruszając jednocześnie poważne tematy związane z budowaniem kultury rozwiązywania problemów w firmie.
Wcześniej jednak uczestnicy uzbrojeni szybko w nowy plan konferencji, podzielili się na dziesięć mniejszych grup, by poczuć namiastkę swobody, którą daje formuła Open Space. Zacięte dyskusje toczyły się w wielu grupach, m.in. na temat organizacji struktury przedsiębiorstwa wspierającej ciągłe doskonalenie, gdzie m.in. przytoczono trzy główne zasady wsparcia prezesa (idź i zobacz, pytaj „dlaczego?” i pokazuj swój szacunek dla pracowników). Mówiono też o zmieniającej się roli zespołów projektowych na początku procesu wdrożenia i w kolejnych latach funkcjonowania Lean w zakładzie. W temacie Hoshin Kanri zwrócono uwagę na rozbicie celów w taki sposób, by każdy pracownik czuł, że ma wpływ na wypełnienie strategii i wizji/misji firmy. Przestrzeżono także przed budową systemu nieprzemyślanych spotkań, z których nie spisuje się nawet żadnych wiążących wniosków.
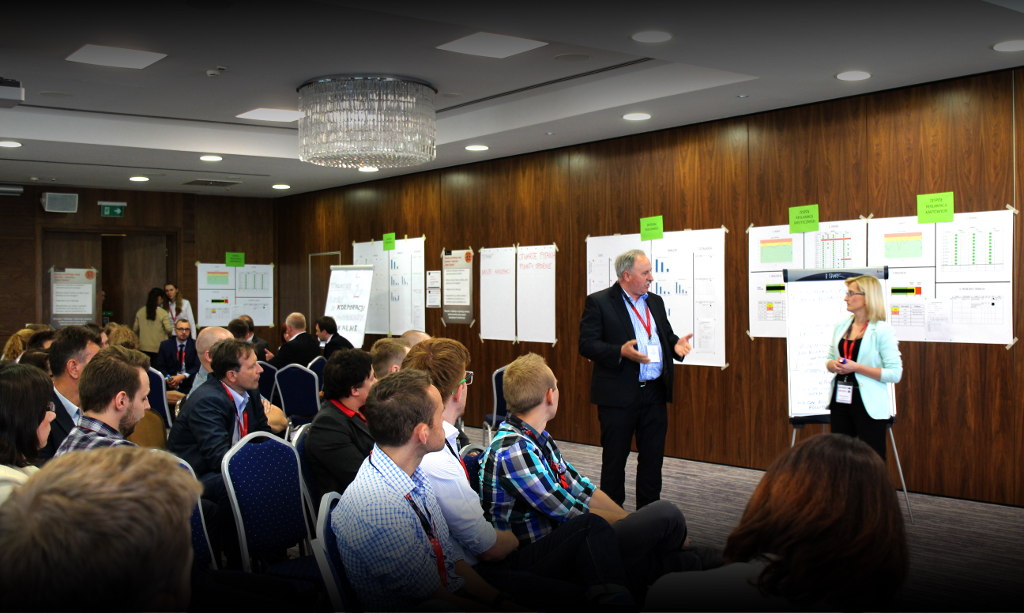
Pigułki wiedzy z pięciu obszarów
W dalszej części uczestnicy ponownie przegrupowali się przechodząc tym razem na pięć seminariów, które prowadzili John Shook, Samuel Obara, Mike Orzen, Chris Vogel oraz przedstawiciele polskiego oddziału Lean Enterprise Institute, a także zakładów zlokalizowanych w Polsce prezentujących swoją drogę Lean w poszczególnych obszarach tematycznych. Z pośród poruszanych przez prelegentów obszarów mocnym akcentem był stosunek do narzędziowego nastawienia Lean niektórych firm. W świecie pojawiają się dodatkowe „S” w ramach punktów 5S, jednak w Toyocie w Japonii, jak mówił Samuel Obara, używane jest 4S. John Shook natomiast wspomniał o istocie Kanbanu, którego nie powinniśmy traktować jedynie jako sposobu na przekazywanie sobie pojemników. Wszystkie te narzędzia, czy idee znaczą dużo więcej i mają wspomagać kulturę rozwiązywania problemów w firmie.
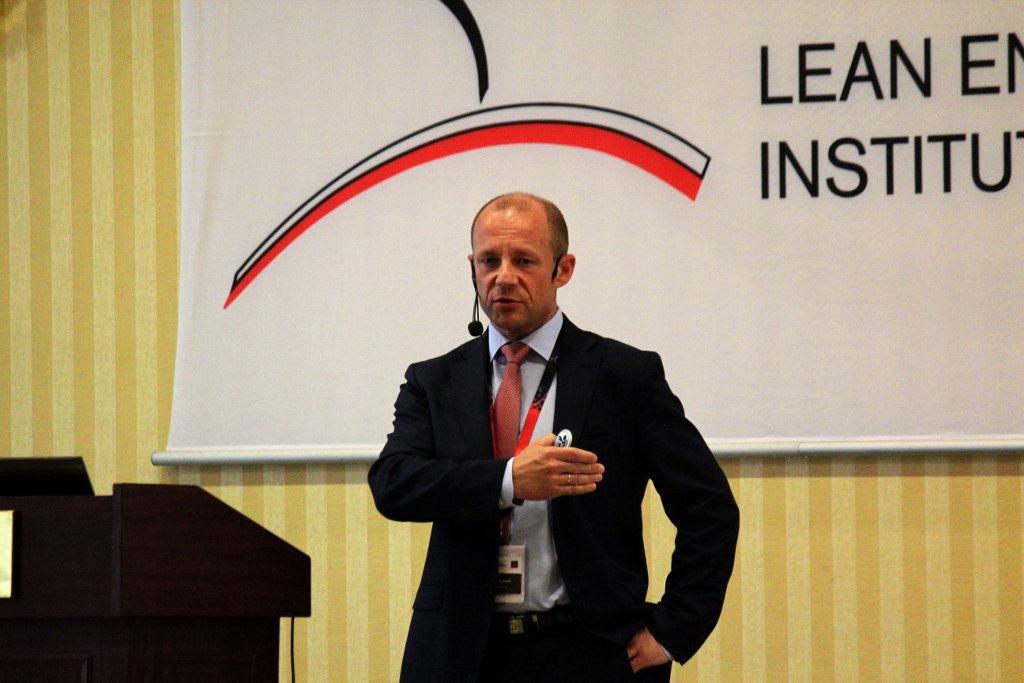
W bloku produkcyjnym mieliśmy okazję posłuchać także przedstawicieli Grupy Nowy Styl – zakładów, które odeszły od systemu akordowego wspierającego konkurencję między pracownikami na rzecz zdefiniowanej płacy z premiami uwzględniającymi naturalny ich rozwój, przez co wzmacniany jest potencjał zakładu. Dariusz Frydrych – Dyrektor Operacyjny w Grupie Nowy Styl pokazał też, że ciężko mówić obecnie w zakładach o czymś takim jak produkcja seryjna. Zakład produkuje 17 tys. krzeseł dziennie, jednak 65% produkcji, to zamówienia indywidualne w seriach od 1-5 sztuk. Jednym z ostatnich projektów jest centrum szkoleniowe, które regularnie będzie odwiedzane przez każdego z pracowników, po to by mogli poznawać znaczenie używanych technik oraz nabywać i odświeżać umiejętności rozwiązywania problemów bezpośrednio w miejscu ich powstawania.
Menadżerowie na usługach pracowników
Drugiego dnia kontynuowano pięć strumieni tematycznych – jeden dla prezesów i dyrektorów o budowaniu strategii i przewodzeniu organizacji oraz po dwa dla produkcji i usług – transformacja procesów i zarządzanie w kulturze Lean.
Jednym z prelegentów strumienia usługowego był Mike Orzen, który pokazywał w jaki sposób możemy stać się coachem dla swoich pracowników. Jak mówił, abyśmy mogli określać się tym mianem, musimy odwrócić się od roli mówiącego „nauczyciela” i skierować w stronę zadającego odpowiednie pytania trenera. Okazuje się, że jest to jedna z najtrudniejszych umiejętności. Pytania nie powinny być bowiem sposobem na pokazywanie źle zrobionej pracy, wyrazem krytyki, albo wymuszeniem dojścia do punktu, który sami sobie wymyśliliśmy. Otrzymujący pytania szkolony pracownik sam dochodzi do rozwiązania problemu z naszym ciągłym wsparciem wykazywanym ponownie poprzez zadawanie odpowiednich pytań. Każda próba odzwierciedla cykl PDCA i jest równocześnie kolejnym krokiem w rozwoju pracownika. Menadżer trenując swojego pracownika musi wykazywać pełne zaangażowanie. Jak mówił Mike Orzen: „Kiedy idę na gembę, wyłączam telefon”, potwierdzając to dobitnie w reakcji na zdziwienie uczestników. Podkreślił również, że dobrzy coachowie widzą najlepszą wersję osoby, do rozwoju której mają się przyczynić.
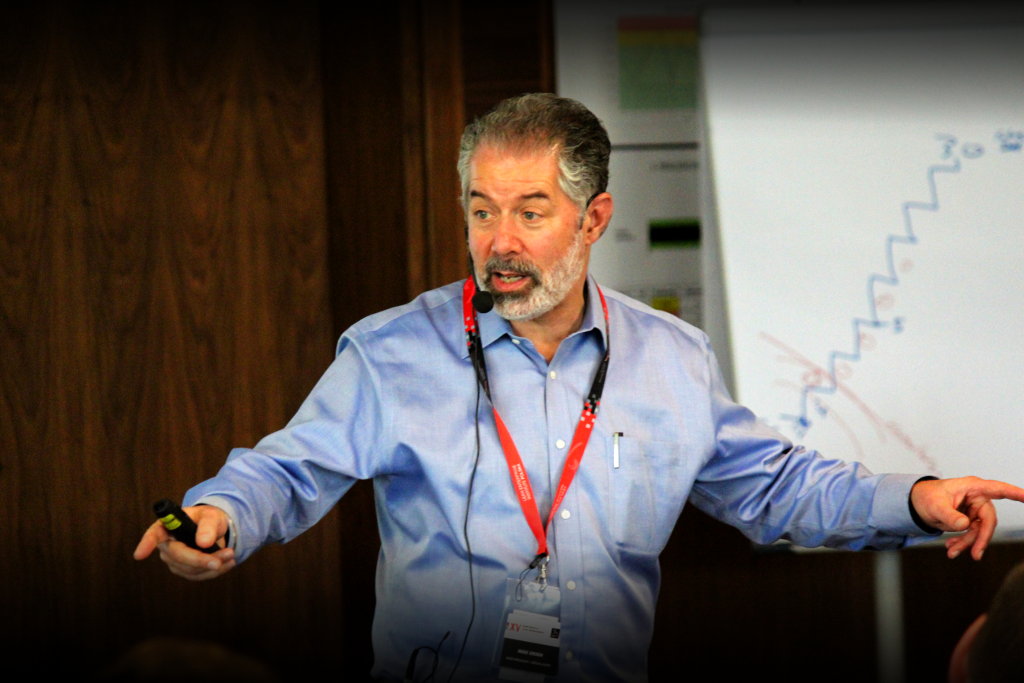
TPM to praca z ludźmi, nie z maszynami
W bloku produkcyjnym drugiego dnia jednym z bloków strumienia produkcyjnego był Total Productive Maintenance, w którym wystąpili przedstawiciele zakładów VW w Poznaniu przedstawiając studium przypadku realizacji nowego podejścia do TPM. Po zaniechaniu części działań w obszarze postanowiono wykorzystać mocne strony wdrożenia z 2006 roku i skorzystać z wiedzy o błędach, które popełniono w pierwszej fazie. Na celowniku pośród kilku czynników znalazła się m.in. czytelność instrukcji, ale także takie dziedziny jak transparentność statusów naprawy, czy przepływ informacji pomiędzy produkcją, a działami usługowymi.
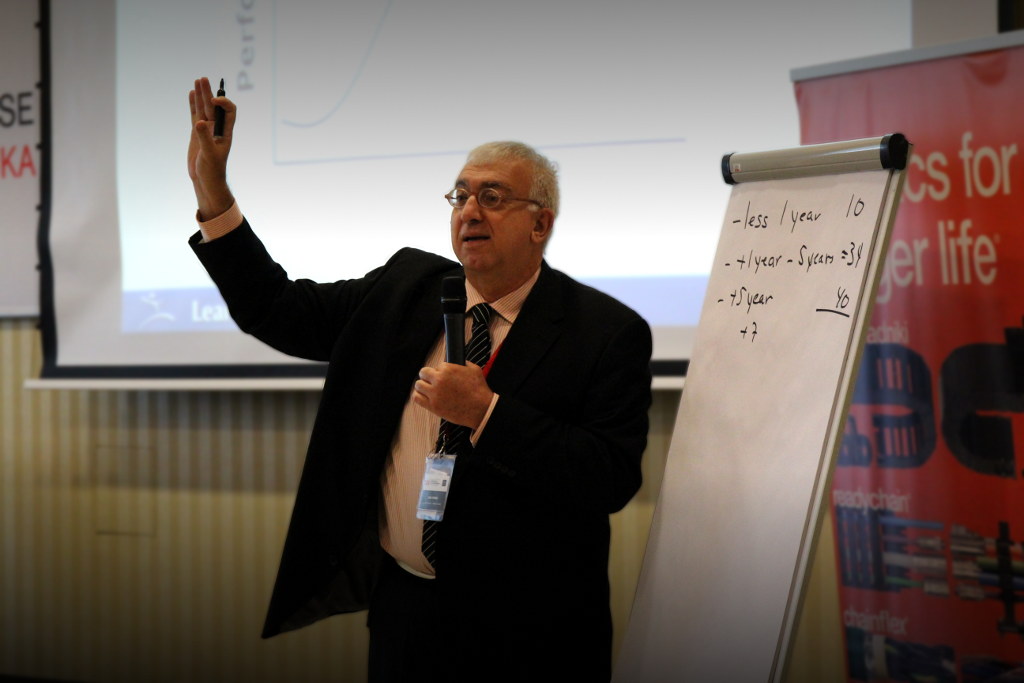
W tym bloku wystąpił także Jose Ferro, który skupił się na miękkich aspektach pracy z autonomicznym utrzymaniem ruchu. Podkreślał, że pracownicy nie mając wszystkich umiejętności do obsługi maszyny, muszą przynajmniej wiedzieć, że w razie problemów otrzymają niezbędną pomoc w jego rozwiązaniu. Wprowadzając TPM w zakładzie powinniśmy się zastanowić, jak te działania wpłyną na zaspokojenie potrzeb klienta oraz skupić się na pracy z problemami oraz dostarczeniu pracownikom narzędzi i możliwości (środowiska), tak by mogli sobie z nimi poradzić.
Dwa koła w osi napędowej zakładu
Ostatnim prelegentem drugiego dnia był wiceprezes zarządu Toyota Motor Manufacturing Poland – Dariusz Mikołajczak. Standaryzacja, genchi genbutsu (czyli wizyty w miejscu produkcji) i rozwój pracowników, to główny przekaz na koniec tej części konferencji. Jeśli idziesz do gemby, zacznij badać problem z pustym umysłem, zmierz się z różnymi punktami widzenia i obserwuj proces w czasie rzeczywistym. Poprzez wspólne zrozumienie tego co jest jasne, a co nie, zespół dochodzi do rozwiązania problemu. Dariusz Mikołajczak przedstawił również koncepcję osi napędowej samochodu, na której jedno koło odwzorowuje rozwój firmy, a drugie rozwój pracownika. Jeśli jest to rozwój niejednolity i skupiony tylko w jednym obszarze (np. korzyści firmy), to wysiłki włożone w Lean nie mają sensu.
W tym kontekście warto powrócić jeszcze do wystąpienia Samuela Obary, który przestrzegł przed zbytnim samozadowoleniem w kontekście pozycji swojej firmy na rynku. Za przykład podał trzy wielkie firmy, które były niekwestionowanymi liderami, a obecnie już nie istnieją – amerykańskie linie lotnicze Pan Am, firmę Atari i producenta butów Converse. Jak mówił: „Jeśli myślisz, że twoja firma jest liderem, a marka jest tak rozpoznawalna, że nie może zginąć, pomyśl już teraz o ciągłym doskonaleniu i kulturze rozwiązywania problemów”. Historia trzech przytoczonych firm może być nauką i przestrogą dla pozostałych, którzy po serii usprawnień spoczęli na laurach.
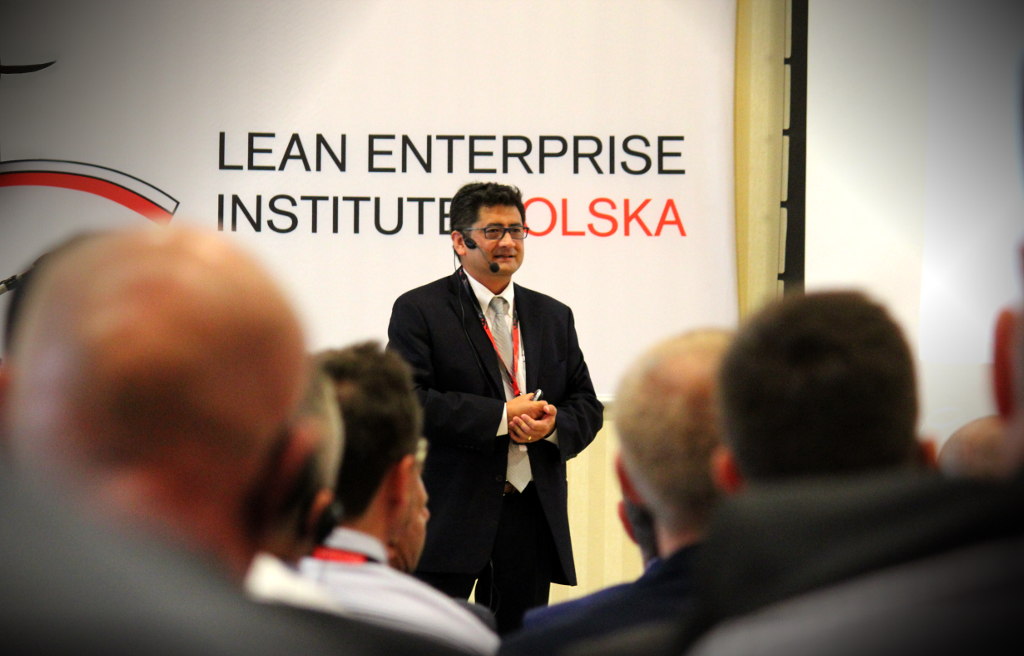
W trzecim dniu konferencji odbyły się tradycyjnie wizyty w firmach produkcyjnych. Tym razem swoje drzwi dla uczestników XV Międzynarodowej Konferencji Lean Management otworzyły zakłady Toyoty oraz Electrolux. Podczas tych trzech dni polscy przedsiębiorcy mieli szansę uczyć się bezpośrednio od osób, które nabywały wiedzę Lean poprzez japońskich mentorów i propagują ją teraz na całym świecie. Pokazują, że Lean to nie tylko zestaw narzędzi, ale przede wszystkim kultura przedsiębiorstwa, w której te narzędzia powstają w celu dostarczenia klientom oczekiwanych wartości.
Pozostałe aktualności Lean
-
Ogólnopolski Kongres Jakościowy 2025: Wiedza. Relacje. Biznes.
W dniach 14-16 maja 2025 roku w Centrum Edukacyjno-Kongresowym Politechniki Śląskiej odbędzie się Ogólnopolski Kongres Jakościowy 2025. To największe wydarzenie w Polsce poświęcone jakości, łączące wiedzę, relacje i biznes. Kongres stanowi unikalną okazję do zdobycia praktycznej wiedzy, wymiany doświadczeń oraz nawiązania strategicznych kontaktów biznesowych.
-
Nowoczesne podejście do doskonalenia procesów - relacja z IX Europejskiego Kongresu Lean
Dziewiąta edycja Europejskiego Kongresu Lean przyniosła uczestnikom ogromną dawkę wiedzy na temat wdrażania efektywnych procesów i innowacji w różnych branżach. Organizatorzy podkreślali, że kluczowym przesłaniem wydarzenia jest przekonanie, że to, co jest dobre dzisiaj, jutro może już być jedynie wystarczające.
-
Bezpłatna Konferencja – Cyfrowa Transformacja w Biznesie
Jak rozpocząć proces zmiany i zadbać o rozwój technologiczny firmy? Już 24 października odbędzie się Konferencja, podczas której zostaną przedstawione najnowsze trendy w zakresie wdrażania i udoskonalania procesu cyfrowej transformacji.
Technologie wspierające Lean
PARTNERZY SEKCJI:
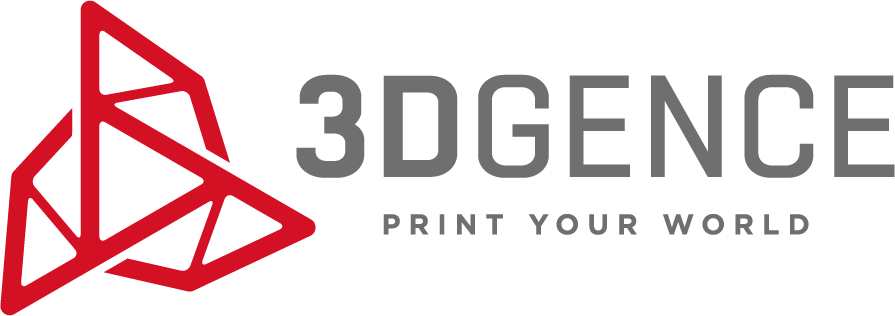
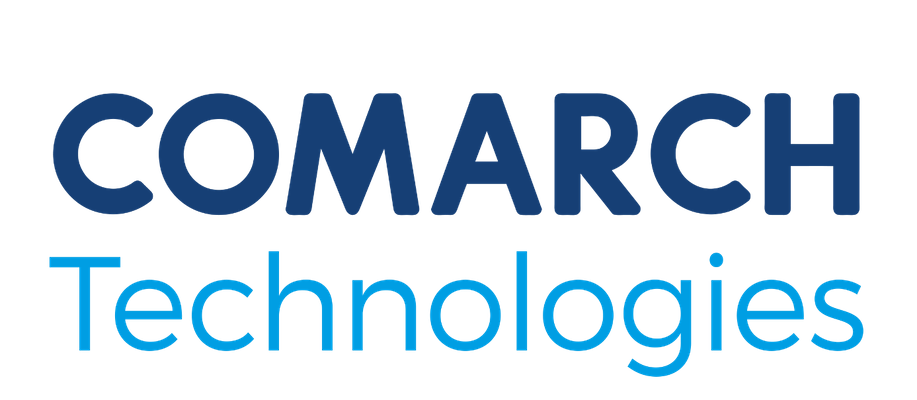
Komentarze
W dniach 14-16 maja 2025 roku w Centrum Edukacyjno-Kongresowym Politechniki Śląskiej odbędzie się Ogólnopolski Kongres Jakościowy 2025. To największe wydarzenie w Polsce poświęcone jakości, łączące wiedzę, relacje i biznes. Kongres stanowi unikalną o ...
Dziewiąta edycja Europejskiego Kongresu Lean przyniosła uczestnikom ogromną dawkę wiedzy na temat wdrażania efektywnych procesów i innowacji w różnych branżach. Organizatorzy podkreślali, że kluczowym przesłaniem wydarzenia jest przekonanie, że to, c ...
PON | WT | ŚR | CZW | PT | SOB | NDZ |
---|---|---|---|---|---|---|
26 | 27 | 28 | 29 | 30 | 31 | 1 |
2 | 3 | 4 | 5 | 6 | 7 | 8 |
9 | 10 | 11 | 12 | 13 | 14 | 15 |
16 | 17 | 18 | 19 | 20 | 21 | 22 |
23 | 24 | 25 | 26 | 27 | 28 | 29 |
30 | 1 | 2 | 3 | 4 | 5 | 6 |