Aktualności Lean
Nie nazywaj TPM-u projektem – relacja z konferencji TPM Excellence
Dodano: 2013-03-27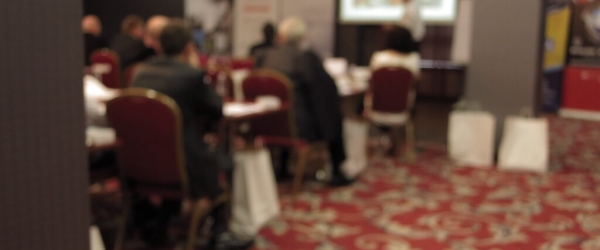
Pierwszym prelegentem był audytor instytutu JIPM – Paul Hardiman, który przedstawiał w żywiołowy sposób cele i idee, które powinny przyświecać wdrożeniu TPM. Rozwiał między innymi wątpliwości na temat tego, czy wszystkie filary są istotne. Określił, że cztery z nich (skupienie się doskonaleniu, autonomiczna obsługa, planowe kontrole i konserwacje oraz szkolenia i nauka) to konieczne postawy, których budowa ma ostatecznie doprowadzić do zera awarii, zera wad i zera wypadków. Jednak, jak mówi, bez pracy w pozostałych czterech filarach, efekty mogą być tylko częściowe. TPM w najlepszych zakładach, to niekończąca się droga. Paul Hardiman podkreśla, że nazywając wdrożenie TPM projektem, zakończymy go jak każdy projekt – spojrzymy na efekty, rozdamy certyfikaty, a później najprawdopodobniej będziemy oglądać powolny upadek TPM-u w naszym zakładzie. Mówi, że skrót TPM w jego opinii powinien mieć rozwinięcie Total Productive Management, co ma wskazywać na ciągłe zaangażowanie kierownictwa w budowę niezawodnego parku maszynowego.
Kolejna prezentacja była znacznie spokojniejsza, a prelegent skupił się na przedstawieniu przykładów działań funkcjonujących w zakładzie Ronal. Tomasz Kalandyk – zastępca kierownika Działu Utrzymania Ruchu – zwrócił uwagę między innymi na ważną rolę zastosowania pilotażowego wdrożenia TPM na jednej linii produkcyjnej, bądź w przypadku bardzo rozbudowanych linii, nawet tylko na pojedynczej maszynie. Przedstawił także strukturę Działu Utrzymania Ruchu, która jest uzupełniona o strukturę TPM wraz z komitetem sterującym i koordynatorami w poszczególnych obszarach zakładu. Przyznał, że w efekcie zmian i podziałowi pracy pomiędzy technikami, a operatorami, udało się wyeliminować wiele mikroprzestojów oraz zwiększyć ilość działań zaplanowanych i zmniejszyć ilość interwencyjnych napraw.
Następny prelegent również rozwinął temat struktury Działu Utrzymania Ruchu i przestawił jej modyfikacje postępujące stopniowo od momentu rozpoczęcia wdrażania TPM. Łukasz Napierała – zastępca dyrektora produkcji ds. Utrzymania Ruchu w firmie Barlinek – przestawił zalety wprowadzenia funkcji planisty utrzymania ruchu. Wskazuje, że ten zabieg jest jednym z bardziej istotnych w dążeniu do zera awarii maszyn w zakładzie. Jak mówi, sam nie widział wcześniej potrzeby zatrudnienia planisty w swoim zespole, jednak obecnie założone jest dodatkowo utworzenie zespołu planistycznego. Faktem zaskakującym dla uczestników było osadzenie dyrektora utrzymania ruchu w zespole kierowanym przez dyrektora produkcji, mimo iż wcześniej byli oni równorzędnymi dyrektorami. Sam Łukasz Napierała mówi jednak że obecna struktura jest bardziej korzystna dla funkcjonowania zakładu, a służby utrzymania ruchu dostały obecnie większe pole działania niż miało to miejsce wcześniej.
Kwestię planowania poruszył również kierownik Utrzymania Ruchu z Akzo Nobel - Mariusz Ostaszewski. Także on przyznał, że zbyt optymistycznie oceniał poprawność prowadzonego przez siebie planowania, o czym przekonał się dopiero po wprowadzeniu zmian w swoim dziale. Ważnym i ciekawym zagadnieniem w tej prelekcji było jednak podejście do szkoleń załogi i modyfikacji sposobu komunikacji w dziale. Mariusz Ostaszewski podkreśla, że w tej materii, tak jak i w innych, warto stosować schemat PDCA. Jeśli wykonamy tablicę, która obwieszcza rozpoczęcie wdrożenia TPM, rozrysowaliśmy schematy, zrobiliśmy nawet piękne obrazki, to może się okazać, że tak naprawdę rozumiemy i czytamy ją tylko my. Co sugeruje prelegent? Nie nakłaniać pracowników do czytania tablicy, tylko sprawdzić, dlaczego nie wzbudza ona zainteresowania. Podobne postępowanie przedstawia w przypadku innych narzędzi, np. stosowanych do zgłaszania awarii, przekazywania informacji o wykonanych zadaniach, czy opracowania systemu diagnozy maszyn w punktach inspekcyjnych.
Kolejną prezentację wygłosił Marcin Walczak – Maintenance Manager z Koelner. W tej prezentacji pojawiło się po raz kolejny wyrażenie „gaszenie pożarów”, które podczas tegorocznej konferencji TPM Excellence zostało przytoczone już kilkukrotnie. Jak mówi, w jego zakładzie pracownicy Działu Utrzymania Ruchu byli strażakami – bohaterami, na których wszyscy oczekiwali podczas kolejnych awarii maszyn. Jednak „gaszenie pożarów” w dużej części skończyło się, a zespół dokonuje teraz więcej planowych konserwacji. Jednym z narzędzi pomagającym w przejściu do poprawionego stanu obecnego była tak zwana dekompozycja maszyn, która jest uproszczoną analizą RCM. Taka analiza pozwala na podjęcie zapobiegawczych działań, które nie są możliwe, gdy opieramy się jedynie na danych z analizy usterek. Marcin Walczak nadmienił również o niezbędnym szacunku przełożonego dla swojej załogi oraz na wykazywaniu zaangażowania, które jest podstawą motywacji całego zespołu.
O roli menadżerów we wdrażaniu TPM mówił szeroko Wojciech Mączyński z WoMa Solution - firmy organizującej konferencję. Przytacza przeprowadzone przez siebie ankiety, w których za najbardziej demotywujący czynnik w pracy operatorzy wskazali nie niskie zarobki, ale kiepskiego przełożonego. Uczestnicy dowiedzieli się także, jakie pracownicy mają wymagania odnośnie swoich przełożonych. I tu znowu, nie zależy im najbardziej na tym, żeby pozwalał im na dużo swobody, lecz na możliwości podjęcia z nim rozmowy na temat problemów w pracy. Wśród cech, które pomagają wdrażać TPM wymienia między innymi umiejętność słuchania, wsparcia zespołu, a także wdzięczność. Najgorszą z cech, która jest jednym z dwunastu gwoździ menadżera przybliżającym TPM do upadku, jest bierność.
Biernością nie wykazywał się nikt podczas wieczornego spotkania przygotowanego przez organizatorów, podczas którego uczestnicy mogli oddać się pełnej losowości ruletce, black jackowi i pokerowi. Na szczęście pieniądze były wirtualne i ze spokojem można było rozbijać bank bez obawy o stratę setek tysięcy dolarów. Być może ruletka była swego rodzaju przygotowaniem do drugiego dnia konferencji, kiedy to już w mniejszych grupach uczestnicy dowiedzieli się między innymi, na co uważać podczas sprowadzania maszyn m.in. z zachodniej Europy, czy z Chin. Rozbieżności w unijnych dyrektywach mogą prowadzić do odmienności w interpretacji. Początkowo oszczędzając na cenie maszyny, może okazać się, że stracimy pieniądze na jej dostosowaniu do wymogów stawianych przez Unię Europejską. Jak zaznaczył Arkadiusz Maciaś z Akademii Bezpiecznych Maszyn, nawet maszyny, które były użytkowane dotychczas w krajach Unii, mogą być niezgodne z obowiązującymi dyrektywami, mimo że pracowały kiedyś z powodzeniem w Niemczech, czy Włoszech. Prelegent analizował również przypadki, w których odpowiedzialność za wprowadzenie do użytkowania w zakładzie niedostosowanej maszyny może spaść m.in. na osobę, która sprowadziła urządzenie do przedsiębiorstwa.
Kolejny temat drugiego dnia, to Teoria Ograniczeń. Zgodnie z jej zasadami skupiamy się na identyfikacji wąskiego gardła, czyli np. najwolniejszej maszyny w całej linii produkcyjnej. Zgodnie z TOC całą pracę należy podporządkować temu ograniczeniu, wzmocnić je, a następnie po zwiększeniu mocy produkcyjnych znaleźć kolejne wąskie gardła i w ten sposób sukcesywnie podnosić możliwości produkcyjne. Marcin Felkiewicz z Akademii Bezpiecznych Maszyn zachęcał do kaskadowego dochodzenia do rozwiązań i przytacza trzy główne pytania Teorii Ograniczeń: „Co zmienić?”, „Na co zmienić?” oraz „Jak spowodować zmianę?”. Ostatni pion należał ponownie do Wojciecha Mączyńskiego, który pokazał, że zarządzanie ilością potrzebnych części do obsługi maszyn nie musi być oparte na zasadach podobnych do ruletki. Zwrócił uwagę m.in. na dokładną analizę ilości pobrań, rodzaju awarii oraz na zastosowanie zasady pareto także w stanu do stanu magazynowego części zamiennych. Przybliżył między innymi zasadę obliczenia wskaźnika rotacji oraz podziału zapotrzebowania w ramach analizy MRO. Jego żywa prezentacja wzbudzała wśród uczestników falę pytań o znalezienie optymalnej dostępność części i o sposoby radzenia sobie z ograniczonym budżetem.
Wojciech Mączyński zapytany o najważniejsze przesłanie konferencji, powiedział, że należy być systematycznym i konsekwentnym w swoich działaniach na drodze TPM. Wspomina również, że to, co motywuje do pracy najbardziej, to poprawa funkcjonowania Działów Utrzymania Ruchu w zakładach prezentujących swoje dokonania oraz realne oszczędności widoczne po zakończeniu poszczególnych etapów wdrożenia. Jak mówi, wartością spotkania w ramach konferencji była również wymiana doświadczeń pomiędzy uczestnikami oraz prelegentami konferencji. Następna konferencja TPM Excellence zapowiadana jest na marzec 2014.
Pozostałe aktualności Lean
-
Ogólnopolski Kongres Jakościowy 2025: Wiedza. Relacje. Biznes.
W dniach 14-16 maja 2025 roku w Centrum Edukacyjno-Kongresowym Politechniki Śląskiej odbędzie się Ogólnopolski Kongres Jakościowy 2025. To największe wydarzenie w Polsce poświęcone jakości, łączące wiedzę, relacje i biznes. Kongres stanowi unikalną okazję do zdobycia praktycznej wiedzy, wymiany doświadczeń oraz nawiązania strategicznych kontaktów biznesowych.
-
Nowoczesne podejście do doskonalenia procesów - relacja z IX Europejskiego Kongresu Lean
Dziewiąta edycja Europejskiego Kongresu Lean przyniosła uczestnikom ogromną dawkę wiedzy na temat wdrażania efektywnych procesów i innowacji w różnych branżach. Organizatorzy podkreślali, że kluczowym przesłaniem wydarzenia jest przekonanie, że to, co jest dobre dzisiaj, jutro może już być jedynie wystarczające.
-
Bezpłatna Konferencja – Cyfrowa Transformacja w Biznesie
Jak rozpocząć proces zmiany i zadbać o rozwój technologiczny firmy? Już 24 października odbędzie się Konferencja, podczas której zostaną przedstawione najnowsze trendy w zakresie wdrażania i udoskonalania procesu cyfrowej transformacji.
Technologie wspierające Lean
PARTNERZY SEKCJI:
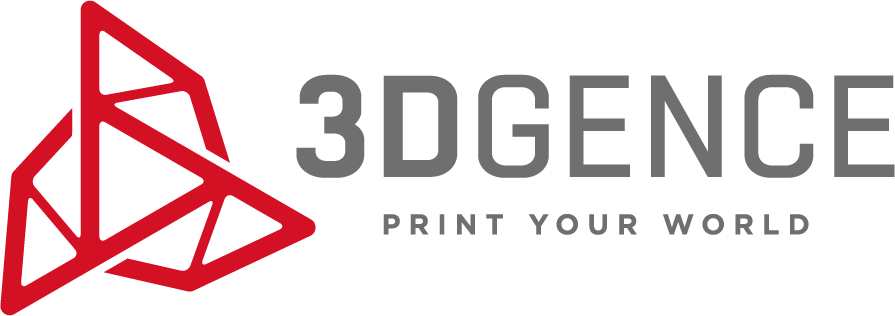
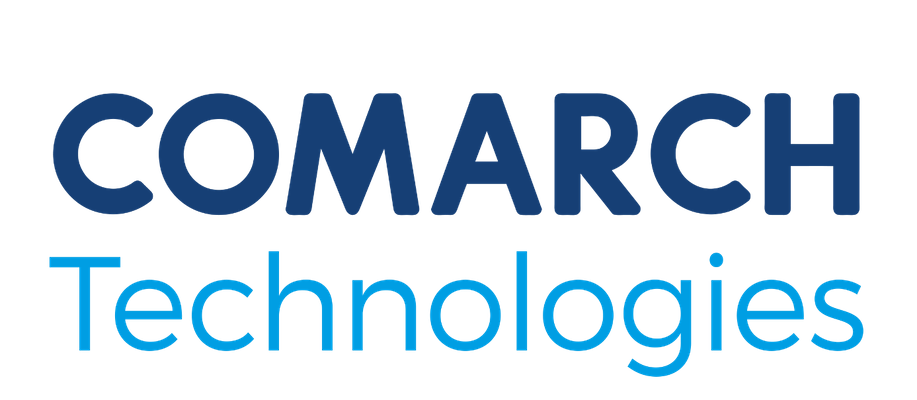
Komentarze
W dniach 14-16 maja 2025 roku w Centrum Edukacyjno-Kongresowym Politechniki Śląskiej odbędzie się Ogólnopolski Kongres Jakościowy 2025. To największe wydarzenie w Polsce poświęcone jakości, łączące wiedzę, relacje i biznes. Kongres stanowi unikalną o ...
Dziewiąta edycja Europejskiego Kongresu Lean przyniosła uczestnikom ogromną dawkę wiedzy na temat wdrażania efektywnych procesów i innowacji w różnych branżach. Organizatorzy podkreślali, że kluczowym przesłaniem wydarzenia jest przekonanie, że to, c ...
PON | WT | ŚR | CZW | PT | SOB | NDZ |
---|---|---|---|---|---|---|
26 | 27 | 28 | 29 | 30 | 31 | 1 |
2 | 3 | 4 | 5 | 6 | 7 | 8 |
9 | 10 | 11 | 12 | 13 | 14 | 15 |
16 | 17 | 18 | 19 | 20 | 21 | 22 |
23 | 24 | 25 | 26 | 27 | 28 | 29 |
30 | 1 | 2 | 3 | 4 | 5 | 6 |
- 08.07.2025 Otwarte szkolenie Lean Koromo
- 06.08.2025 Szkolenie Lean z grą Koromo w firmie Scanfil