Aktualności Lean
Papier i technologia XXI wieku współdziałają razem w intralogistyce – relacja z konferencji
Dodano: 2020-06-19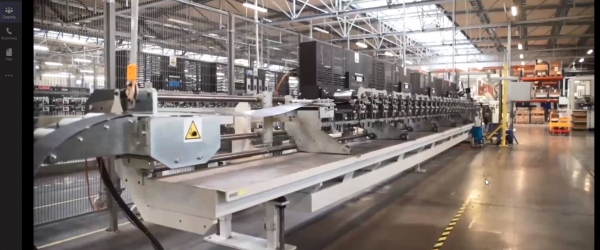
W Polsce wdrożenie raczej nie będzie motywowane oszczędnościami
Jako pierwszy na konferencji wystąpił Marcin Szczebak z CoLogis, który pokazał nam działanie m.in. AGVS – wózków widłowych automatycznie sterowanych. Rozszerzenie funkcji AGV o samodzielne pobieranie palet, to sposób na zautomatyzowanie tam, gdzie nie ma możliwości wprowadzenia kolejek milk-run. Pojawiają się jednak wyzwania dotyczące współpracy wózków autonomicznych oraz tych sterowanych przez operatora.
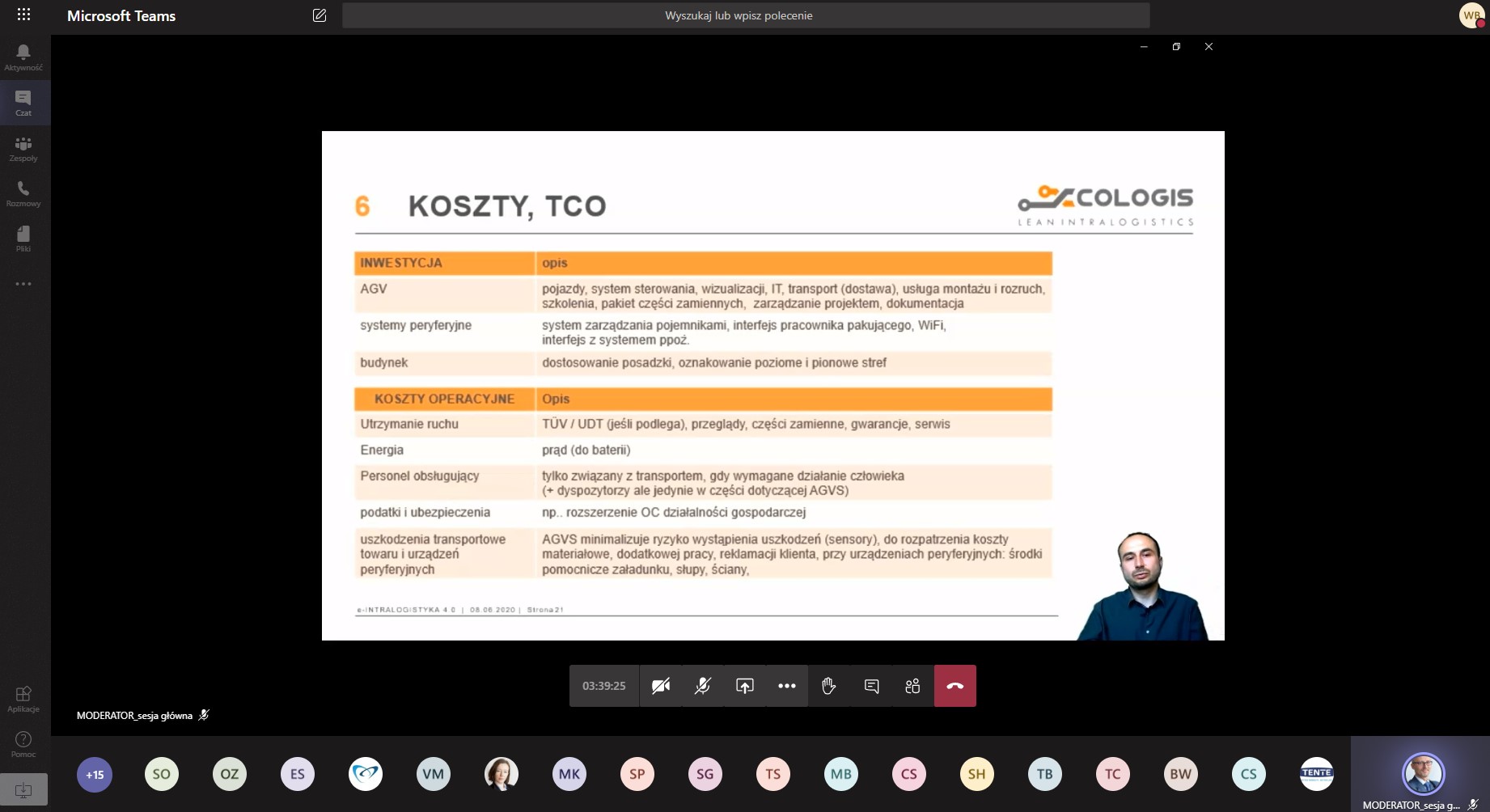
Wyzwaniem może być określenie wymaganej dla procesu ilość pojazdów. Musimy przyjąć, że raczej dopiero symulacja będzie to w stanie zrobić dokładniej. Powinniśmy liczyć się z tym, że prognoza będzie różniła się od wyniku symulacji zwłaszcza jeżeli nasz proces logistyczny jest dosyć złożony - co nie jest bez znaczenia na etapie zbierania i porównywania ofert. Rozbijając koszty wdrożenia, powinniśmy pomyśleć o kilku pobocznych aspektach. Należy zwykle doliczyć m.in. budowę sieci WiFi, często także wymiany podłogi, stacji monitorowania, ładowania. Jednak na przykład w niemieckich warunkach system takich wózków zwraca się po około trzech latach. W Polsce na tą chwilę, raczej jest to inwestycja opłacalna tylko w momencie, gdy zależy nam na testowaniu nowych technologii, jednak nie do końca uzasadniona ekonomicznie. Wdrożenie warto rozważyć również w strefach, w których istnieją ciężkie i niebezpieczne warunki pracy zagrażające operatorom. Jeśli natomiast chodzi o bezpieczeństwo użytkowania zautomatyzowanych wózków, możemy odnosić się do sporządzonych w ostatnich latach norm ISO i VDI.
Co zrobi AGV, gdy wystąpi sytuacja awaryjna?
Adrian Kaźmierczak i Daniel Kafel z Bridgestone Poznań przedstawili, w jaki sposób w ich fabryce funkcjonują wózki widłowe AGV przeznaczone do przewożenia palet, a także nietypowych materiałów, które dostarczane są w dużych szpulach. Pierwszy z prelegentów przedstawił porównanie dostępnych systemów bezpieczeństwa reagujących na styku z pracownikiem. Istniejące systemy omijania przeszkód są one bardzo ciekawe ze względu na brak potrzeby wyznaczania sztywnej trasy, jednak na tą chwilę trzeba wziąć pod uwagę, że osoba w momencie nieuważnego wejścia przed taki pojazd, nie do końca jest w stanie przewidzieć, jaki unik wykona ten wózek.
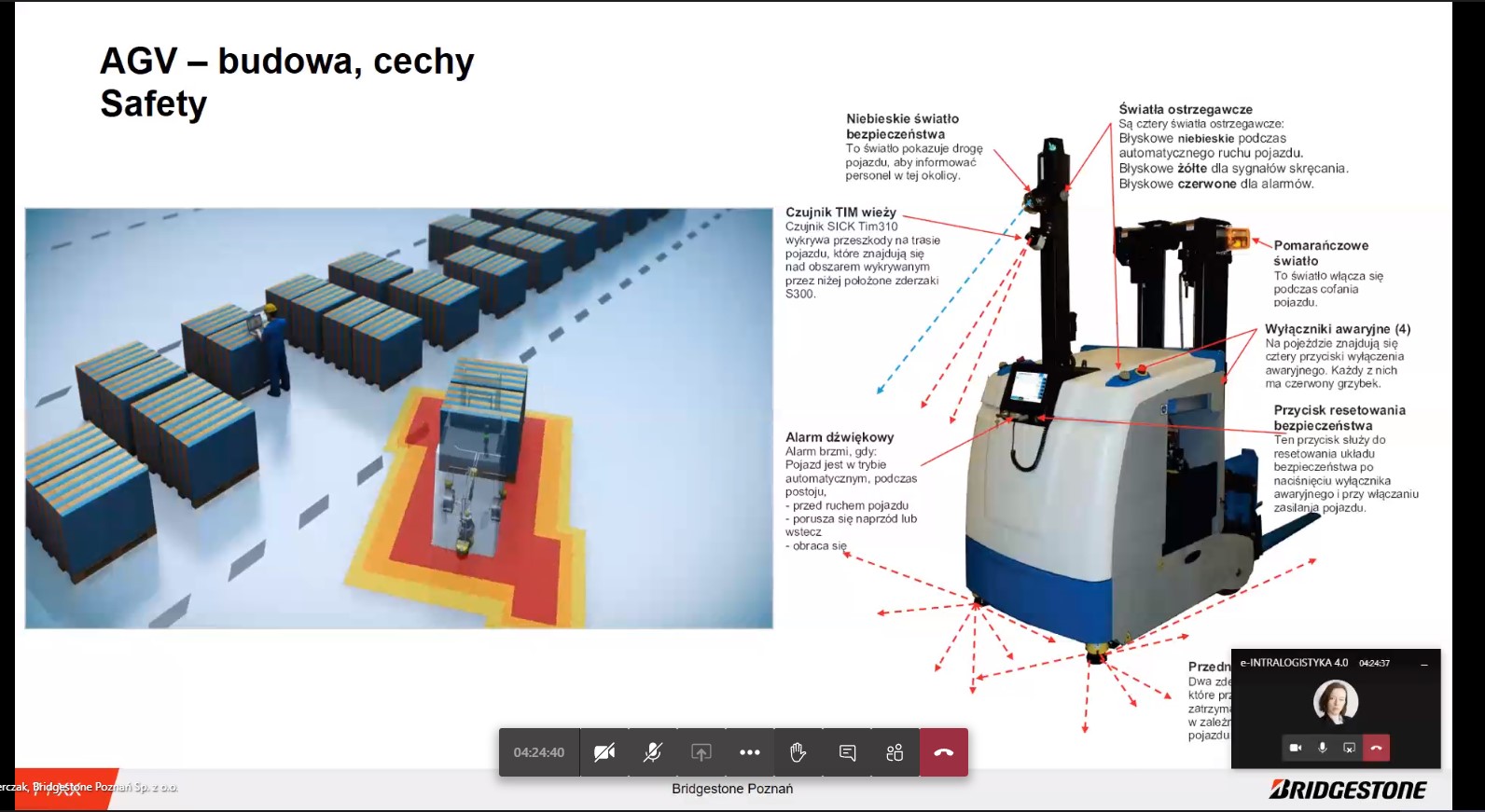
Dlatego ważne jest nauczenie pracowników nowych zasad poruszania się w hali, w którym pierwszeństwo ma wózek AGV, następnie wózek z operatorem, a w ostatniej kolejności pieszy. Jeśli wózek AGV wjeżdża na skrzyżowanie jest również to sygnalizowane świetlnie. Jeszcze większe znaczenie ma też dyscyplina w odkładaniu materiałów – w przypadku pozostawiania palet, czy innych elementów na drogach i w strefach manewrowania, narażamy się na zakłócenia w realizowaniu zadań wózka. Powinniśmy też zwrócić uwagę na elementy wiszące ponad drogą, które również mogą powodować błędne decyzje robota i przestoje.
Musimy też pamiętać, że szybkie podmiany materiału na linii z powodu awarii lub też zmiany planu produkcyjnego, są właściwie niemożliwe – dlatego wprowadzenie AGV na linię wymaga też współpracy z planistami. Powinniśmy przy tym wdrożyć procedury awaryjne, w których jasno określone są momenty, kiedy powinien wkroczyć wózek tradycyjny z operatorem, a kiedy nadal trasę jest w stanie obsłużyć wózek automatyczny.
Zapas mniejszy o 30 godzin, powierzchnia o połowę
Janusz Blinkiewicz z Volkswagen Poznań pokazał nam, w jaki sposób w poznańskiej fabryce w 108 sekund dostarcza się 2500 części. Zapoznał nas ze strukturą zakładu, a potem pokazał, co przyniosło firmie przejście z pojedynczego zamawiania materiałów „na żądanie” do ustrukturyzowanego systemu Kanban – w dodatku papierowego. Można byłoby sądzić, że przejście na papier, to krok wstecz. Jednak uzyskane wynik świadczą o czymś zupełnie innym.
Przykładowo, jeśli mamy 40 godzin buforu, to jest to znacząca różnica w stosunku do obecnych 12 godzin, które utrzymywane są po wdrożeniu usprawnień. Prelegent wspomniał również, że elementem wymagającym dodatkowego przemyślenia był wyładunek towarów z kolejek, a to ze względu na wiele jednokierunkowych dróg w zakładzie. Jednocześnie celem jest dynamiczne sterowanie z tzw. dworca, co oznacza, że jeden pociąg jest w stanie obsługiwać różne trasy tymi samymi wózkami. Janusz Blinkiewicz zwrócił uwagę również na aspekt ludzki stwierdzając, że jeżeli osoba ma szerokie spojrzenie na procesy i na to, co dzieje się w firmie, to upatruje, niezależnie od dotychczasowych jej umiejętności, duży potencjał do rozwoju.
Wirtualna wizyta w firmie
W ostatniej części pierwszego dnia znaleźliśmy się w zakładzie farmaceutycznego koncernu Curtis Health Caps. Przedstawiciele firmy Paulina Suchanecka, Jakub Wojtaszak i Piotr Przybylski przeprowadzili nas poprzez cały proces produkcyjny - magazyn wsadu, proces kapsułkowania, wycinania, suszenia, preinspekcji, sortowania i pakowania, a także magazyn wyrobu gotowego.
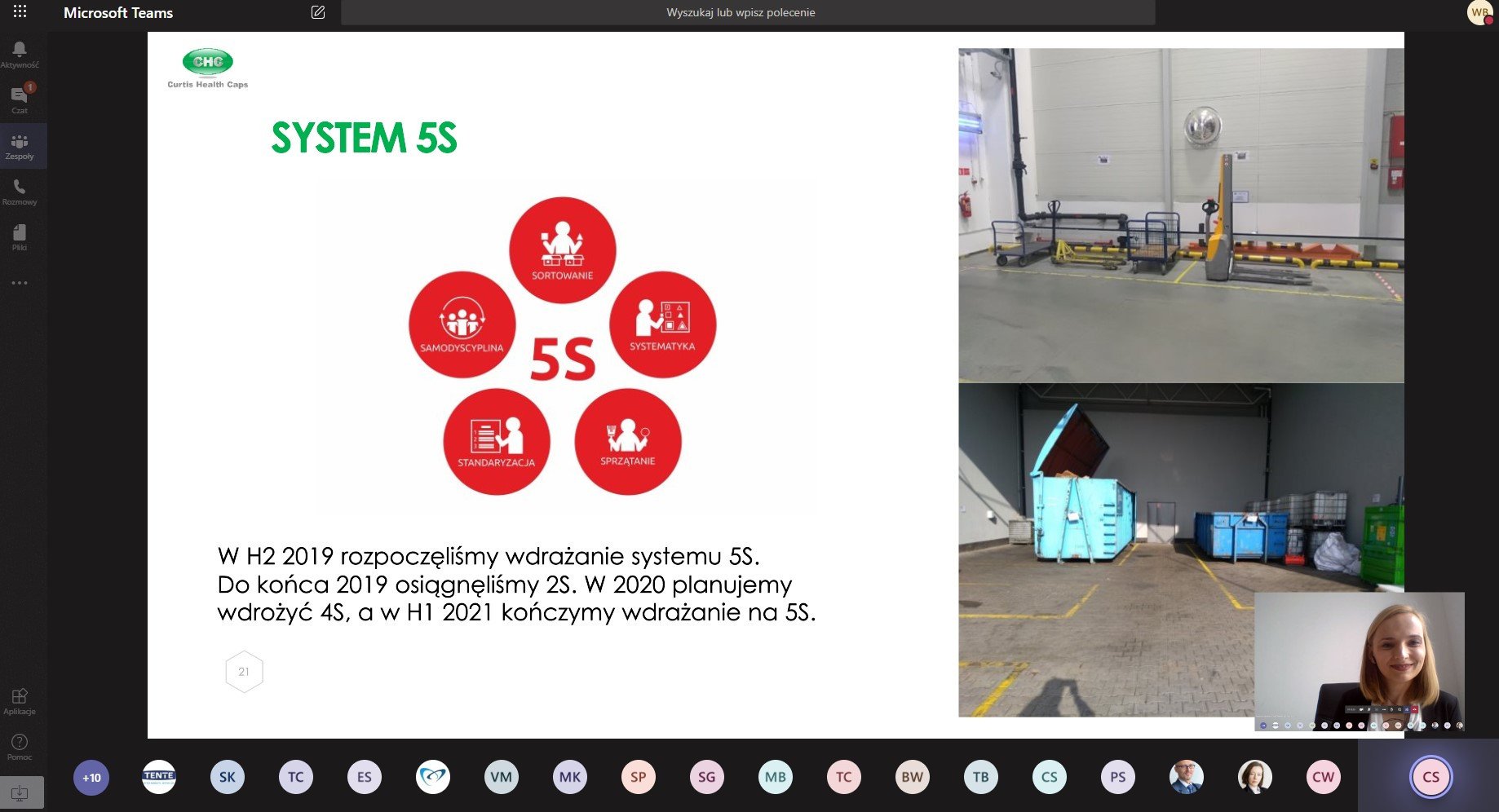
Magazyn wysokiego składowania, to obiekt o powierzchni ponad 3 tys. m2 i 5 tys. miejsc paletowych. Posiada cztery strefy temperaturowe, przy czym, w większości produkty są przechowywane w strefie 15-20 st. C. W ubiegłym roku rozpoczęto tu 5S, które wspomaga tak ważną w tego typu zakładzie czystość. Jest stosowane także zarządzanie wizualne, m.in. także poprzez palety – białe palety są dostępne tylko na obszarze produkcji, nie mogą wychodzić poza niego, a materiały pomiędzy paletami są przestawiane przez manipulator ciśnieniowy. Produkcja w zakładzie realizowana jest w oparciu o konkretne zamówienia klientów.
Jakie odczucia po wirtualnej wizycie? Wymaga skupienia, gdyż oglądamy ją przez ekran komputera nie czując całym sobą zakładu. Będzie zapewne jeszcze bardziej ciekawa, gdy będziemy mieli możliwość płynnego przesyłu na żywo przez oprogramowanie do wirtualnych spotkań np. filmu 360 stopni, bądź skorzystania wręcz z rozwiązań VR. Oglądanie fabryki na monitorze, można porównać do oglądania filmu z gór. Widzimy cały obraz, jesteśmy kierowani przez prowadzącego jego tokiem myślenia, jednak ciężko wyłapać szczegóły, które zauważamy, gdy jesteśmy bezpośrednio w tym miejscu osobiście. To oddalenie utrudniło też zadawanie bardziej szczegółowych pytań. Jednak szacunek należy się za to, że organizatorzy wraz z gospodarzami przygotowali materiał specjalnie na tę okazję, a trzeba przyznać że był on dosyć długi i wyjaśniono w nim sporo niuansów dotyczących przedstawianego procesu.
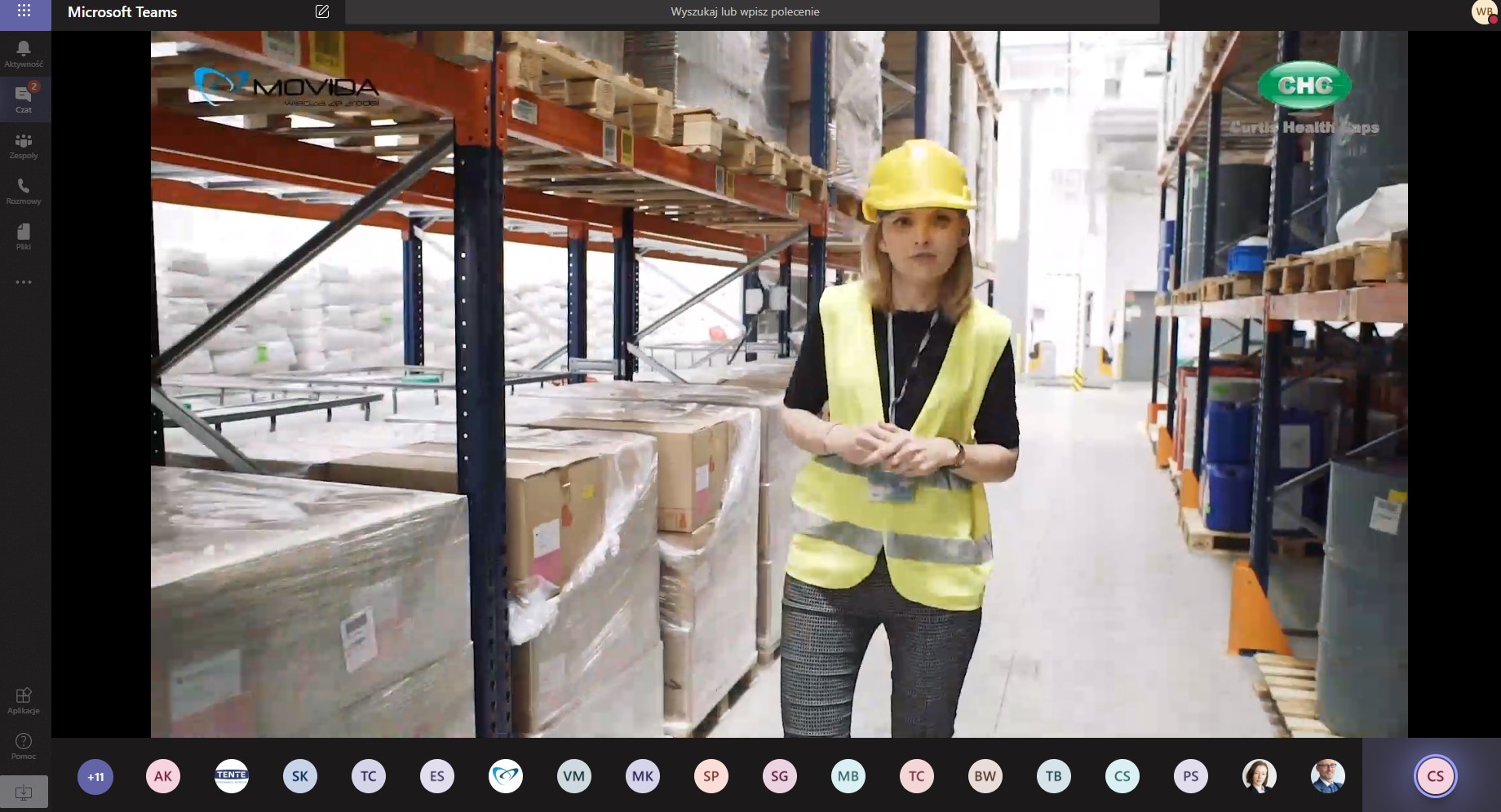
Metamorfoza procesu logistycznego
W drugim dniu pierwszym prelegentem był Łukasz Balcerak z Fabryki Napędów ABB. Mówił o Kanbanie, przewidywaniu produkcji dla poszczególnych modułów, sposobie przekazywania materiału na produkcję i ewolucji regałów na samej produkcji. Początkowo stosowano mało elastyczne pod kątem zmian, ciężkie regały, a teraz wszystkie są oparte o systemy rurkowe, co więcej, konstruowane przez ich docelowych użytkowników – tak by zapewnić jak największą i najbardziej wygodną dostępność materiału. W zakładzie wprowadzono również wysoki skład i antresolę, która pozwoliła na rezygnację tysiąca palet na magazynie zewnętrznym.
W ABB wykorzystywany jest także system Click by light, który jest dodatkową prewencją przeciwko pomyłkowym pobraniom materiałów. Pracownicy wiedzą, nie tylko czy pobrany towar jest odpowiedni, ale także otrzymują informację, jeśli dany komponent wymaga przeliczenia.
Zakład ma też duże doświadczenie z Kanbanem, który w pewnym momencie został dodatkowo przeniesiony na linie produkcyjne. Zmiana podejścia doprowadziła do zwiększenia ilości Kanbanów z 1050 do 6000 cykli. W tej chwili 80-85 procent materiału jest dostarczana w pierwszej godzinie od zamówienia (wcześniej do 24 godzin). Stosowane są tutaj Kanbany masowe na pojemnikach, ale też Kanbany, które są przeliczalne na każdą sztukę.
Następnie mieliśmy okazję zobaczyć kilka projektów z zakładu ABB, które eliminowały między innymi oczekiwanie, nadmierne przetwarzanie, nadmierny transport. Na co zwrócił uwagę prelegent, to że już same procesy obracania pustych pojemników generują spore straty, czy też podobne zadania, jak zmiana usytuowania koszów na śmieci przy regałach, która dała rocznie 80 tys. zł oszczędności. Okazuje się, że nawet zmiana tras, które powodują ciągłe otwieranie bram, również dla firmy przynosi ogrom korzyści dla zapewnienia stałości dostaw.
Wzrost mimo ostatnich wydarzeń
Małgorzata Bednarska-Lisowska z firmy Velux wprowadziła nas w temat planowania produkcji, pokazując w jaki sposób firma zmieniła ten proces – co dało m.in. siedemdziesięcioprocentową redukcję zmian w założonym wcześniej planie produkcji. Plan jest mrożony na tydzień, bądź dwa. Ale możliwe jest jego zwiększanie nawet o 10%, co sprawia, że produkcja dodatkowo jest uruchamiana w sobotę. Prelegentka podkreśliła, jak ważne jest to, by następny proces był zaplanowany dopiero w momencie, gdy poprzedni został już przygotowany.
Przed zmianami w zakładzie plan był na cały dział, nie było poziomowania produkcji, były piki, brakowało też informacji, kiedy startujemy i w jakiej sekwencji. Teraz jest to dla wszystkich widoczne, a dodatkowo istnieje możliwość porównania planu z realnym czasem produkcji. Tematami, które są omawiane później na spotkaniach, to odchyłki w zgodności w stosunku do założonego planu produkcji. Jeżeli realizacja jest poniżej 98%, docieramy do przyczyny takiej sytuacji.
Poruszony też został aspekt ludzki. Czas liderów, który poświęcany był na zastanawianie się, co produkować, został uwolniony i przeznaczony m.in. do planowania szkoleń i ich przeprowadzania wśród swojej brygady. W cały projekt weszło także planowanie zasobów ludzkich, co dało redukcję kosztów nadgodzin o 60%.
Mobilność i bezpieczeństwo
Ostatnią tego dnia była prezentacja przygotowana przez Katarzynę Siudak z firmy Tente, która zajmuje się produkcją kół do procesów intralogistycznych. Koła w różnego rodzaju wózkach mogą stanowić o tym, czy operator lub operatorka będzie mogła przemieszczać dany regał ręcznie. Tam, gdzie nie wjedzie wózek widłowy, można zastosować koła z samodzielnym napędem – taka platforma, np. sterowana przez operatora może przejeżdżać w miejscach, gdzie jest intensywny ruch pieszych. Problemem mogą być też sytuacje, gdy kółka regałów są zablokowane w pozycji skrętnej, a są przewożone na ciężarówkach lub wózkach AGV – okazuje się, że również istnieją rozwiązania, które automatycznie, poprzez sprężynę przy każdym podniesieniu przywracają te kółka do jazdy na wprost.
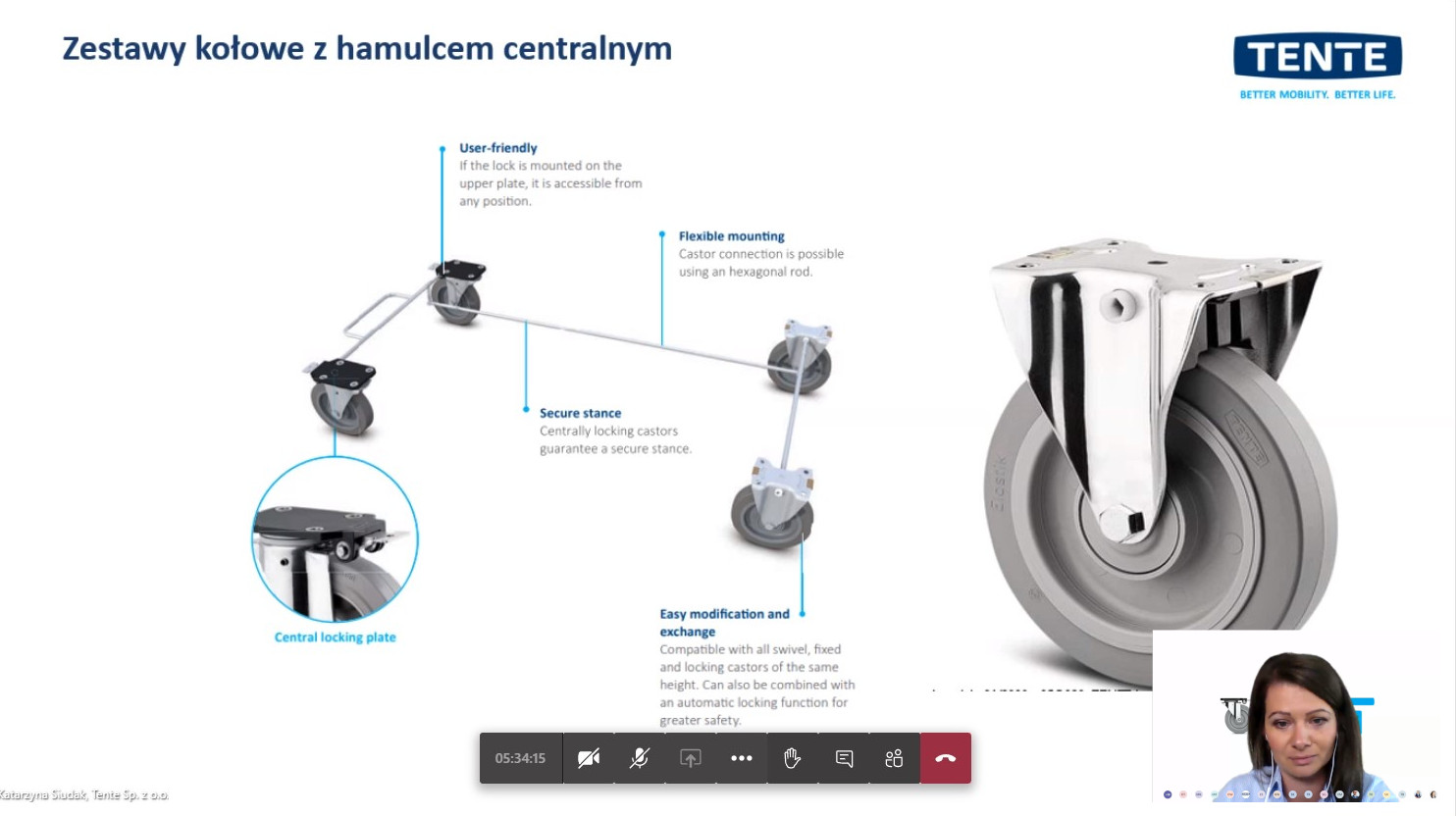
W świecie fabryki przerzuconym do komputera
Konferencja on-line, czyli dwa dni przed komputerem. Trzeba przyznać, że prelegenci przekazali ogrom wiedzy. Bardzo szczegółowe prezentacje i dużo ciekawych faktów bezpośrednio z miejsc, w których toczy się życie produkcyjne. Forma on-line wymagająca jest skupienia i dyscypliny, by przy nadarzającej się okazji nie uciec myślami do innych zadań i maili, ale to już indywidualny wybór każdego z uczestników. Tak jak i podczas konferencji, gdzie obecność jest fizyczna, a myśli mogą uciekać, a mózg podpowiadać, by sięgnąć po komórkę. Na drugiej strony szali stoi minimalizacja czasu i kosztów na logistykę. Stąd, jako forma uzupełniająca, e-konferencje mogą w przyszłości stać się stałym punktem wśród uczestników pragnących bez dalekich wyjazdów pozyskać wiedzę na interesujący ich temat.
Pozostałe aktualności Lean
-
Ogólnopolski Kongres Jakościowy 2025: Wiedza. Relacje. Biznes.
W dniach 14-16 maja 2025 roku w Centrum Edukacyjno-Kongresowym Politechniki Śląskiej odbędzie się Ogólnopolski Kongres Jakościowy 2025. To największe wydarzenie w Polsce poświęcone jakości, łączące wiedzę, relacje i biznes. Kongres stanowi unikalną okazję do zdobycia praktycznej wiedzy, wymiany doświadczeń oraz nawiązania strategicznych kontaktów biznesowych.
-
Nowoczesne podejście do doskonalenia procesów - relacja z IX Europejskiego Kongresu Lean
Dziewiąta edycja Europejskiego Kongresu Lean przyniosła uczestnikom ogromną dawkę wiedzy na temat wdrażania efektywnych procesów i innowacji w różnych branżach. Organizatorzy podkreślali, że kluczowym przesłaniem wydarzenia jest przekonanie, że to, co jest dobre dzisiaj, jutro może już być jedynie wystarczające.
-
Bezpłatna Konferencja – Cyfrowa Transformacja w Biznesie
Jak rozpocząć proces zmiany i zadbać o rozwój technologiczny firmy? Już 24 października odbędzie się Konferencja, podczas której zostaną przedstawione najnowsze trendy w zakresie wdrażania i udoskonalania procesu cyfrowej transformacji.
Technologie wspierające Lean
PARTNERZY SEKCJI:
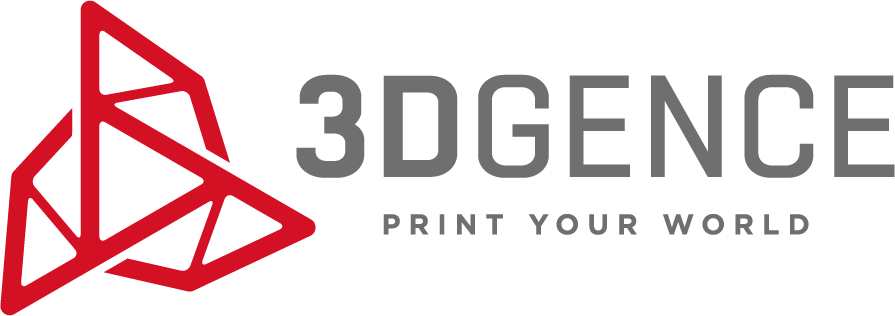
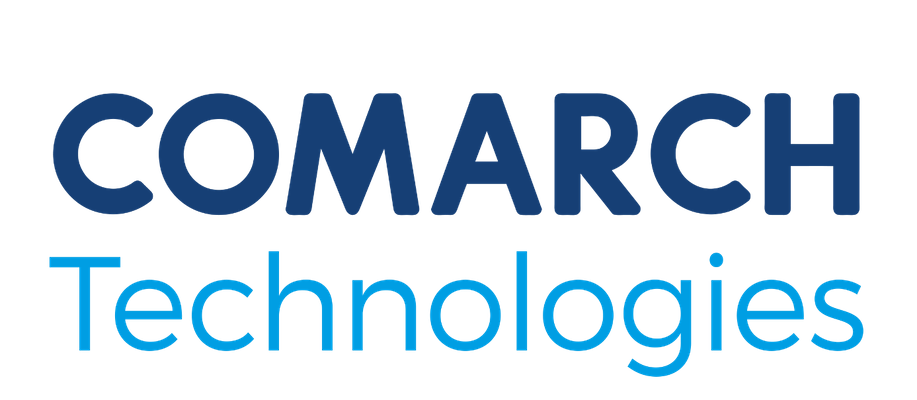
Komentarze
W dniach 14-16 maja 2025 roku w Centrum Edukacyjno-Kongresowym Politechniki Śląskiej odbędzie się Ogólnopolski Kongres Jakościowy 2025. To największe wydarzenie w Polsce poświęcone jakości, łączące wiedzę, relacje i biznes. Kongres stanowi unikalną o ...
Dziewiąta edycja Europejskiego Kongresu Lean przyniosła uczestnikom ogromną dawkę wiedzy na temat wdrażania efektywnych procesów i innowacji w różnych branżach. Organizatorzy podkreślali, że kluczowym przesłaniem wydarzenia jest przekonanie, że to, c ...
PON | WT | ŚR | CZW | PT | SOB | NDZ |
---|---|---|---|---|---|---|
1 | 2 | 3 | 4 | 5 | 6 | 7 |
8 | 9 | 10 | 11 | 12 | 13 | 14 |
15 | 16 | 17 | 18 | 19 | 20 | 21 |
22 | 23 | 24 | 25 | 26 | 27 | 28 |
29 | 30 | 1 | 2 | 3 | 4 | 5 |